现代企业的竞争格局正在向立体化、多元化方向发展。消费者除了要求产品具有良好的性能、时尚的外观和可靠的质量以外,还希望有个实惠的价格,这是买方市场的普遍特征。目前国内汽车消费已经呈现出多元化的格局,消费者开始追求个性化,要求产品特性能与自身的需求、喜好相符。桑塔纳独占国产轿车市场的局面已成为历史。目前上海大众已有普桑、桑塔纳2000和帕萨特三个轿车产品系列,与赛欧在同档次竞争的紧凑型轿车也在准备生产中。一汽大众除了捷达和奥迪A6之外,一款档次低于帕萨特的轿车摫磾即将下线。大众汽车中国投资公司负责人曾经说过,未来几年在中国的合资企业要达到的目标是,建立一个完整的覆盖所有级别的汽车产品体系。
对于企业来说,一方面为了满足消费者多元化的需求,既要具备强大的新产品开发和设计能力,不断推陈出新,又要能掌握降低产品制造成本的秘诀,取得竞争优势;另一方面激烈的市场竞争迫使产品更新换代的速度日益加快,产品的寿命周期不断缩短,企业开发新产品所承受的商业风险越来越大。比如拿国产轿车来说,八十年代中期上市的普通桑塔纳轿车兴盛了十多年,至今仍在生产,而桑塔纳2000型轿车的生产周期只有6-7年左右即需改型,通用别克轿车也比预计要短,今后新产品的寿命周期还将进一步缩短,大约为3-4年。上海通用正式投产3年来,每年都能推出新的变形车以满足市场的需求。面对市场求变的特性,企业只有更快、更省地开发出更新、更好的产品,才能取得竞争的相对主动权。从世界范围来看,许多大的汽车集团公司比如通用、大众等在技术开发上不惜重金的同时,也开始注重彼此合作和共同开发,压缩单个新产品的开发费用,提高产品的竞争能力。历史也多次证明,许多原本具有较好市场前景的产品,由于缺乏有效的成本控制而导致最终的失败。因此可以说,新产品开发的前期策划和费用控制已成为现代企业经营管理的一项重要的工作之一,这一点对于国内的汽车生产企业具有很强的现实意义。
一、前期策划和费用控制的必要性
首先、2001年内中国将加入WTO,5-6年的保护期以后进口汽车可以轻松进入中国市场,而到那时国内的汽车生产企业会面临一次大的洗礼,那些技术落后、规模较小、成本偏高的企业将被淘汰出局。据权威机构分析,目前在高关税的庇护下,国内轿车的售价约高出世界平均水平60%-80%左右,而国内汽车零部件价格也高出25%-30%左右。即便考虑到正常关税保护和成本降低,我们与国际水平也存在着相当大的距离。加入WTO无疑给中国的汽车工业敲响了警钟,催促我们必须尽快降低产品成本,以适应国际市场竞争的需要。
轿车进口关税变化预测表
时间 |
2000年 |
2002年 |
2004年 |
2006年 |
整车关税率 |
80%-100% |
55%-70% |
30%-40% |
20%-25% |
零部件关税率 |
20-30% |
16%-24% |
12%-18% |
10%-12% |
其次、新产品开发工作对产品制造成本的影响作用越来越大,特别象汽车这种前期投入大,资本和技术双密集型的产业更是如此。传统的成本管理只注重产品生产过程的成本控制,忽视投产前的产品开发和设计的成本管理。产品投产后,降低成本各种作业消耗,提高生产效率当然是降低成本的一条途径,但如果产品本身设计不合理,存在过剩功能,造成先天的成本缺陷,产品一旦投产,降低成本的潜力就不大了。俗话说得好:“凡事预则立、不预则废”,据内部测算分析,如果新产品前期策划和费用控制得当,产品的最终制造成本可以节约20%以上(包括材料费用和工装模具的减少)。因为完善的前期策划一方面可以减少产品设计过程中不必要的失误,降低工装模具和专机制造成本,充分利用现有的机器设备,压缩固定成本;另一方面也可以合理选用合适的原材料和通过国产化等效替代同步化等一系列措施迅速降低材料成本,提高产品合格率,节约变动制造成本。
再次、加强新产品开发的前期策划和费用控制也是提高企业自身管理水平的内在需要。第一、轿车整车开发的周期相对较长,主机厂在推出新一代车型之前往往先对老车型的装饰性部件进行更改设计,满足消费者求新求变的心理需求,适当延长整车产品生命周期,因此车部件的生命周期普遍要短于整车的周期,这就给汽车零部件的生产经营增加了难度。第二、汽车零部件在新产品开发中,部分设计需要委托国外合作者进行,相应增加开发和设计成本。以模具为例,据测算和分析,同样的模具,进口价格是国内制作的一到二倍左右,因此从某种意义上说,加强新产品开发的前期策划,提高自身的开发设计能力将有助于我们减少设计和模具费用的支出,大大降低产品制造成本。第三、新产品国产化工作进程缓慢。一个产品一般需要10个月-1年的时间。由于新产品采用了大量的进口零部件,再加上产品质量要求较高,可能导致一定的亏损。在国产化之前产品制造成本很难大幅度下降,削弱了企业的盈利能力,甚至造成“产品投产之时就是亏损之日”的尴尬局面。如果在开发前期就做好VE工程,尽可能考虑产品制造成本因素,就能取得主动权,避免不利结果的出现。
二、前期策划和费用控制的具体内容
上述三点阐明了新产品开发的前期策划和费用控制的必要性和重要性,良好的开端往往是成功的一半。接下去就如何进行新产品的前期策划和费用控制的方法和步骤进行论述。新产品的前期策划包括可行性研究(主要是对外部市场和内部能力的分析)、制定开发计划和提出开发费用预算,以及价值工程分析等四项内容,而费用控制则包括期前控制(费用预算)、期中控制(对比分析)、期后控制(最终评价)三个步骤。
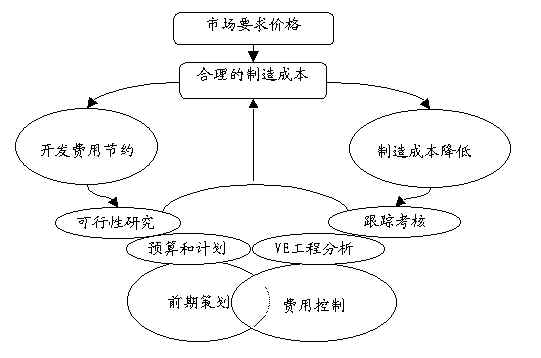
完善开发前的可行性研究可以提高企业新产品开发的成功率。现在许多企业不大重视可行性研究和分析,认为这项工作缺乏现实的可操作性,费时又费力,即便做了也只留于表面文章,没能落到实处。其实可行性研究是一项十分重要的工作,它包括市场前景分析、价格定位分析、目标成本分析、投资规模分析等多项内容,通过利用现代财务成本管理的多种方法深入分析,可以发现开发过程中可能会遇到的种种困难和问题,从而事先制定对策,做到未雨绸缪,并能充分利用现有的资源,合理安排投资规模,提高产品开发的成功率。可以说开发前的可行性研究是新产品能否成功的关键步骤。这里需强调一点,可行性研究必须注重全面的定量分析,减少主观判断,避免片面理解,特别是只看到好的一面而忽视分析潜在的风险。
制定新产品计划和费用预算有利于开发费用的控制。在可行性研究的基础上制定具体的开发进度计划和费用预算,这两项工作可以融合起来进行,开发计划为费用预算的制定提供技术上的支持,而开发费用预算则为具体的每一个阶段确定合理的支出规模,从资金上保证开发工作的顺利进行,提高开发的质量和效果。
开发进度计划分为前期设计和过程计划,具体包括日程进度安排计划、开发组成员间的协作计划、国产化进程计划、生产工艺的编制计划等一系列的分计划。
而费用预算需要先结合企业以往积累的经验数据和开发当时的实际情况的分析,确定总体投资规模大小,然后以开发进度为依据在时间上做合理的分配,并落实到相关部门作为今后跟踪控制的依据。各部门在总计划和预算的基础上制定相应的分计划和预算安排,使总计划和预算更加详细,明确,具有可操作性。无论总目标还是分计划都必须遵循两个原则:1、要比历史有所进步,比如制定开发费用相对节约比例和缩短开发周期等,2、要具有可操作性和适当的弹性,任何计划都需要最终实施才能实现,无法实施的计划不能称之为计划,另外为了适应环境的变化在制定计划时应保持相对的弹性。
制定好的费用预算需要执行并加以跟踪控制考核。在具体执行过程中需要注意以下几点:(1)重要性,即效率优先的原则,对开发过程中支出比例大的要重点跟踪,重点考核,比如模具制作、设备采购、设计费用等,这些费用支出的多少直接关系到总体预算能否实现,因此只有确保这些费用支出合理才能保证总体目标的最终实现。(2)动态性,即费用的控制必须和开发的进度紧密衔接,判断支出是否超过计划目标不是只看金额的绝对值,而是要和进度作比较,确定其合理性。(3)激励性,即有理有利的原则。一方面对于实现目标的部门应给予必要的奖励,提高参与人员的积极性,另一方面对于未实现目标的部门要分析具体的原因,对缺乏必要控制的部门进行处罚,提高相关部门的责任心和效率。
面的产品价值工程分析。我们不仅要分析产品整体的价值,还要对产品实施结构细分,从每个零部件中挖掘降低成本、提高价值的潜力,形成产品价值工程分析的树形支状网络。在产品的制造成本中,直接材料的比重最高,往往会超过50%。另外通过研究我们发现随着产品技术含量的提高和市场竞争的激烈化,产品材料比率和工费比率在不断提高。
某种汽车零部制造成本比例表
产品名称 |
A车(80年代) |
B车(94年) |
C车(98年) |
D车(00年) |
材料占销售比 |
42% |
48% |
53% |
68% |
工费占销售比 |
14% |
16% |
20% |
21% |
为了有效降低产品的材料成本,我们需要进行价值工程分析(VE),在保证产品基本性能不变的前提下,实现节约化设计和材料等效替代,提高产品的价值量。此外原材料成本发生的过程包括采购、库存、使用等各方面,只要每个环节都有效地控制一点点,则最终成本降低的水平将非常可观。除了材料项目以外,对于工费等成本项目,我们也应根据相对比重大小,逐项进行分析,减少不必要的工序,压缩加工时间,通过点的改变来带动线和面的提高。
5、一个开发项目完成以后,最后的总结必不可少,特别是开发费用的汇总计算和总结分析。运用比率分析、结构分析、趋势分析等方法,寻找偏离目标值(包括正反两方面)的项目进行原因分析,为今后的开发工作提供参考数据,积累经验。
三、对相关部门和人员的要求
整个新产品开发前期策划和费用控制是一项复杂的系统工程,需要得到相关部门的理解和支持,除了要广泛宣传,提高思想认识以外,还需要得到技术、人力和物力等各方面的配合。
对技术人员的要求。设计观念的创新:产品的成本并非仅仅在制造和流通过程中才可以下降,在设计(包括产品工艺等设计)阶段就应该考虑产品的制造成本。事实证明产品在前期策划和设计阶段降低成本的自由度要远远大于后期制造和流通过程,对降低成本可以起到事半功倍的效果。可以这么说,产品的设计应该包括技术设计和成本设计两个方面,缺一不可。由于开发工作中渗透了成本的内容,对技术人员提出了更高的要求,不仅要精通设计技术,还需具备一定的成本知识,树立“成本设计”的理念。在开发过程中不仅要做到设计合理,还要考虑到零部件的制造成本的降低。在同等技术条件下尽量选用通用件代替专用件,选用国产材料代替进口材料,选择结构简单、易于制造的设计代替机构复杂、难于制造的设计。总而言之就是将成本控制工作融入到设计的每一个角落。针对设计理念的新变化,我们要为设计人员提供相应的条件支持,第一、组织设计人员参加相关经济和成本知识的学习和培训,帮助他们自觉建立成本意识,把产品成本高低作为评价设计质量的又一项重要指标。第二、制作比较完整、详细的原材料和零部件价格目录和成本档案,供设计人员参考(简称产品设计成本库),节约材料成本。第三、会计和成本部门给予必要的咨询和建议,协助设计人员共同完成设计工作,使经济成本分析渗透到技术工作中去。
对材料分析的要求。设计中对材料的选用工作十分重要,不同的材料具有其特定的性能,而性能相近的材料在价格上也会有很大的差别,因此需要设计人员在具体选择时要能够熟悉材料的性能和价格。技术开发部要加强材料分析和研究工作,并制定较系统、完整的材料档案资料,提高设计中材料选用的合理性。另外、对新近开发产品的核心零件进行攻关,尽早实现此类重要零件的国产替代,并逐步形成本公司的核心零部件的制造和供应体系,扩大生产规模,以满足新产品开发和生产的需要。对相互协作的要求。新产品前期策划和费用控制需要得到各部门的理解和支持,其范围包括设计、工艺、专机、国产化、产品试制等方面,因此为了提高设计的效率和效果,节约开发费用,降低制造成本,需要相关部门能相互支持、相互协作,形成多维的开发体系。比如,在产品设计阶段就融入国产化的工作,在产品设计阶段就考虑成本预测和控制等。虽然原材料和零部件的等效替代是一个技术范畴,但对降低成本的贡献较大,如能在确保产品质量和性能的前提下实施有效替代,那么产品制造成本可以进一步降低。当然在实际实施过程中应坚持与主机厂协商,取得充分的理解和支持。
3 、对设计和模具开发的要求。模具费用占整个制造成本的比例较高,且这一比例是建立产量较大的基础上的,如果缩短实际的摊销年限(2
年内摊销完的话),那么模具费用的比例还会进一步的提高,另外企业尚待摊销的模具费用金额较大,一旦车型改型,经营风险会很高,因此提高模具自行设计和制作的能力是控制开发成本的又一项重要的工作。一方面要加大模具加工设备的资金投入,提高模具的生产能力,为今后大规模开发新产品提供有力的支持,另一方面应该给模具设计和制造人员提供更多技术学习和交流的机会,包括选派出国培训和学习。争取在较短时间内实现大型核心模具的自行设计和制作。另外零部件厂还要和主机厂就产品寿命周期、模具所有权和模具分摊年限的问题协商一致,以便取得主机厂的充分理解和支持,共同降低模具的成本。
综上所述,加入WTO 给中国汽车零部件厂商生产的经营和管理带来了巨大的压力。在5 年内汽车的产品制造成本必须每年降低5%
,与此同时还有许多新的产品等待着开发和设计,因此竖立“设计成本、成本设计”的新设计理念,加强新产品开发的前期策划和费用控制就显得格外的突出和重要。
|