编辑推荐: |
本文基于系统工程的思想理念,提出应用
MBSE 科学开展飞机智能装配体系能力建设的方法,并在成飞公司开展应用实践,取得了阶段性成果,初步实现智能制造中“精准执行、动态感知”的局部特征。
本文来自于微信公众号壹航智库,由火龙果软件Linda译、推荐。 |
|
一代飞机,一代技术,现代飞机功能要求朝着超机动、超巡航、长寿命、高可靠、高隐身的方向发展。新一代飞机在材料、结构、工艺、功能上都与上一代飞机有很大的差异,复合材料用量比大幅提升,整体化结构大量使用,以数字化为基础的制造技术逐步取代以刚性定位、手工钻铆为主的工艺技术。以往三代飞机以模拟量传递为主的装配技术体系已无法满足新一代飞机的装配需求,迫切需要构建基于数字化、网络化、智能化的智能装配能力,实现我国飞机装配技术体系的升级换代。
近年来,高校、研究院所及相关企业在智能装配领域开展了许多积极的探索与研究。智能装配工艺设计与仿真方面,以上海交通大学为代表的单位研发了虚拟装配仿真系统并实现工程应用
[1–2],成飞、西飞等多家主机厂对全机装配单元进行仿真验证,提前发现并解决产品设计、工装设计、工艺设计中影响装配的潜在缺陷与问题。飞机装配生产线建模与仿真方面,相关研究成果已应用到装配生产线规划中
[3–4]。
自动化、数字化装配系统建设方面,以清华大学、浙江大学、中国航空制造技术研究院为代表的单位,面向新一代飞机装配需求研发了飞机大部件对合、部件自动制孔等数字化装配系统,解决了装配过程中的瓶颈问题
[5–8]。装配车间智能管控研究大多集中在智能装配排产、仓储管理与物流调度算法等方面,而对体现管控智能的基于大数据挖掘的自主决策分析、基于仿真模型的数字孪生技术方面的研究较少,也尚未实现成熟的工程应用
[9–11]。
综上所述,我国在智能装配领域各单点技术域上紧跟国外研究成果,突破了一系列关键技术并取得重要成果,特别是以数字化装配、装配仿真为代表的智能装配技术已实现工程应用。然而,飞机大部件智能装配能力建设涉及领域多、范围广,多学科、多专业交叉融合特点显著,是一项复杂的系统工程,现阶段单点技术突破与应用并不等于全局最优,如何采用先进的方法对智能装配体系能力建设进行整体性规划、全局性优化,已迫在眉睫。因此,提出基于MBSE
科学开展飞机大部件智能装配体系能力建设的方法,逐级明确和细化飞机大部件智能装配能力建设需求与技术方案,构建相应的数字模型并采用仿真技术进行不断验证、迭代优化,最终实现智能装配能力效用的最大化。
基于 MBSE 的装配能力总体设计
MBSE 是一种以模型为中心的系统工程层次设计方法,应用具有图形化的建模语言构建系统模型,在系统设计初期运行测试模型实现对系统功能逻辑的分析、测试和验证,以达到消除预期问题、减少项目成本以及降低项目风险的效果。目前
MBSE 已经在波音、洛马、空客等航空企业中得到广泛应用,在飞机设计与制造过程中取得了良好的应用效果,大幅提高了工作效率,减少了设计与制造缺陷,缩短了周期和成本。
基于 MBSE 的飞机大部件智能装配能力建设主要分为系统总体需求分析、系统功能分析、系统架构设计、分系统设计、实施验证
5 个阶段,具体如图 1 所示。
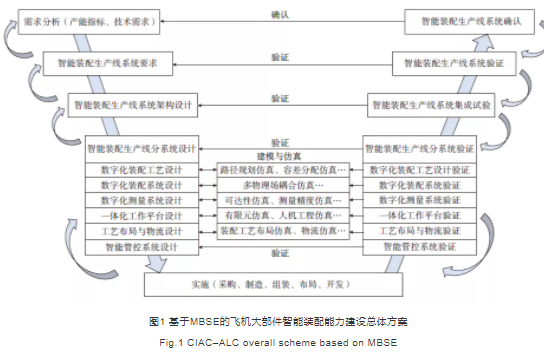
1 需求分析
系统总体需求分析是指对用户要求进行收集、梳理,形成系统顶层需求并建立系统用例模型。航空产品制造技术正朝着信息化、集成化、网络化和智能化的方向发展,对新一代飞机制造提出了高精度、低成本、短周期、多品种、高质量与高可靠性等全新技术需求。结合企业发展现状,飞机大部件智能装配生产线的总体建设需求为:满足新一代飞机研制优质、高效、低成本的需求,实现大部件装配与数字化环境的深度融合,装配效率提升
N1 倍;工艺、生产、物流、设备全维度信息化融合,总体产能提升 N2 倍,装配质量问题下降 N3 (%)。
实际上 {N1,N2,N3} 是根据用户需求、单位实际生产情况及长远发展战略综合考虑确认的,它们代表了系统能力建设的综合量化指标,这些指标具体还要分解到各个分系统层面。以
N3 为例,分解方式说明如下。
首先,对一段时期内的装配质量问题进行统计分析,得出各个分系统导致质量问题占比,依次分别为{M1,M2,…,Mi,…,M6},计算出分解到第
i 个分系统的指标 Qi=Mi*N3,即各分系统指标依次为 {Q1,Q2,…, Qi,…,Q6}。然而,由于各个分系统质量问题降低的难度系数不一致,设计难度系数集
{R1,R2,…,Ri,…,R6},其中∑ (i=6)Ri=1。组织专家采用层次分析法进行综合评价,计算出相对真实可靠的难度系数,最终得到各个分系统最终的质量指标
Wi=Qi*Ri。
2 系统功能分析
开展系统功能分析,明确满足总体需求的系统各项功能要求。着眼全局,针对工艺流程中的瓶颈环节、痛点问题,综合采用数字化、网络化、自动化、智能化方法,构建装配工艺设计功能模块、数字化装配功能模块、数字化检测功能模块,以及计划调度平台、设备管控平台、物流运输智能管控平台、仓储配送管控平台,为飞机大部件智能装配系统架构设计奠定基础。
3 系统架构设计
系统架构设计是指通过系统功能分析和分配来构建功能架构,并根据现有的技术条件,把功能架构 “映射”成物理架构,将功能分解、定义并分配到相关的部件及组件上,从而完成具体方案的设计。在此阶段主要完成生产线系统架构的总体设计。
飞机大部件智能装配系统总体架构如图 2 所示,由精准执行层、数据收集层、数据处理层、平台应用层构成,其中:
(1)精准执行层包括数字化装配系统、数字化测量系统、集成工作平台、仓储、物流、工装、工具等生产资源及产品;
(2)数据收集层则通过 PLC、 DNC 采集器、RFID、条码技术、手持终端、传感器等信号采集和传感设备实现对装配系统工作状态、设备运行情况、产品加工状态、物资储运情况、工人位置、状态信息等的采集;
(3)数据处理层通过运用大数据、云计算等实时分析技术将收集到的海量数据进行实时检测、传输与分发、处理与融合,然后将异构、多源、分散的现场数据转化成可用于智能决策的标准化制造信息;
(4)控制平台层包括计划调度平台、设备管控平台、物流管控平台、仓储管控平台,该层具备一定的决策与自学习、自适应能力,可在指导飞机装配过程中不断地丰富专家知识库,利用专家知识库对不同状态的制造信息做出相应的决策,并对执行层进行精准控制。
4 分系统设计
根据系统的功能特性及专业特点,将复杂系统解耦,将生产线系统架构分解成 6 个相互独立、复杂程度相对较低的分系统:实现工艺顶层策划、仿真、工艺文件编制等全过程数字化的装配工艺设计;实现关键装配工艺环节的数字化装配系统;实现飞机部件装配精度在机测量及评价的数字化测量系统;实现集“气、电、网”于一体的集成工作平台;实现均衡生产节拍、提高生产效率、保证生产资源利用率且满足工艺流程的工艺布局与物流;实现有效提升数字化装配单元的自感知、自诊断、自优化、自决策和自执行能力的智能装配管控系统。
各分系统建设同样基于 MBSE的小 V 循环模式。在各分系统设计初期,即软件、硬件设施投入生产之前,根据各分系统的设计需求建立相关数字模型,用于直观清晰地描述系统运行的功能和状态。然后对数字模型进行仿真分析,迭代验证各分系统设计的准确性和完整性,以确保分系统设计及需求的正确性,减少后期能力建设实践过程中的迭代验证次数。基于
MBSE 的各分系统建设方法详见后文。
5 试验验证
根据飞机大部件智能装配能力建设总体架构和智能装配生产线分系统设计,将试验验证分为两个阶段。
第 1 阶段,对数字化装配工艺设计、数字化装配系统、集成工作平台等进行技术攻关,逐步建成具备基础数据收集功能以及网络节点布局合理的数字化装配单元,并完成装配单元需求、设计完整性和正确性的验证。
第 2 阶段,开展制造网络连接、制造规划与执行技术、智能化物流配送等智能装配软件工具平台的构建,通过虚拟生产与现实生产相融合、生产计划实时调整、生产过程智能管控等技术的实施,逐步建成基于数据决策和智能网络系统的大部件智能装配车间,满足生产线产能指标和技术指标的需求。
装配生产线分系统设计
1 装配工艺设计
数字化装配工艺设计(图 3)是基于三维数模,以数字量传递为基础,通过软件工具、仿真平台来实现工艺顶层策划、工艺设计、建模仿真、工艺文件编制等过程的全面数字化。MBSE
框架下的数字化装配工艺设计流程如下:
(1)从承接设计要求、指导现场生产的需求分析开始,结合项目总体目标以及当前的工艺能力条件,开展装配工艺设计的总体架构设计,完成顶层工艺策划。
(2)根据总体架构设计,结合工艺流程逐步开展工艺分离面的划分、 MBOM 顶层设计、容差分配方案设计、装配流程设计、三维工艺布局设计、装配工艺文件编制、工艺规范规划与编制等分步设计,完成装配工艺方案的初步设计。
(3)通过容差分析、布局产能仿真、装配仿真、有限元等专业的CAM/CAE 工具进行建模与仿真,实现工艺仿真与工艺规划的无缝集成,开发数字化工艺设计工具,建立工艺知识数据库及资源库,实现基于工艺知识库的工艺文件结构化、自动化编制,提升工艺设计效率及质量。通过数字化工艺设计平台及使能工具的应用,验证工艺设计以及工艺方案的合理性,完成装配工艺方案的分步验证,并生成指导详细工艺设计、现场作业生产的指导性工艺文件。
(4)对装配工艺设计进行架构验证及最终确定。
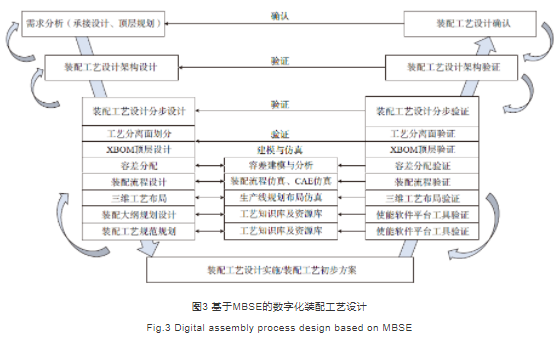
2 工艺布局与物流设计
从产能指标、产品运输安全的需求分析开始,通过对工艺分离面、装配层次、装配方法等工艺方案及厂房面积、结构的需求分析,完成厂房工艺布局及物流设计的总体架构设计(图
4),然后对需求进行层层分解,以工艺流程为基础,结合生产周期逐步完成产能节拍、工位配比、工位布置、仓储系统设置、物流路径规划等分系统的设计,得到厂房工艺布局基本方案;通过数字化仿真分析工具从布局、流程、空间、人机效果等方面对各分系统进行仿真分析乃至优化,经过多轮迭代,找到最优解,确定满足工艺流程和生产节拍的布局与物流设计方案,在厂房面积、工位配置、物流路径等各方面达到精益化生产需求。
通过 DELMIA 软件分别建立厂房、飞机产品、工艺装备、设备等仿真模型,利用 Plant Layout
模块进行厂房三维布局,并在三维环境下按照产品装配顺序进行零件、组件、部件、运输设备等资源的合理性仿真,验证工艺布局和装配流程的可行性。利用QUSET
软件,对总体布局规划、产品工艺流程、生产节拍、设备参数、装配线布局及物流规划等内容进行了仿真验证分析,具体如下:
(1)生产瓶颈分析:依据飞机装配特点,采用设备负荷率分析方法进行生产线瓶颈分析,通常生产线中的瓶颈往往出现在设备负荷率相对较高的环节,具体表现为瓶颈设备加工繁忙,而其上游设备处于堵塞状态,其下游设备处于等待状态。
(2)节拍及产能分析:生产节拍是指生产线上连续出产两个相同产品之间的时间间隔,根据仿真后产品生产数据,可得到装配系统不同工序对应的工件产量及实际生产节拍,同时对工件通过主要工艺装备(包括设备、工装等)
的情况进行统计,包括 加工时间、阻塞时间、故障时间、闲置时间等,计算出不同状态在系统仿真运行过程中的占比,即可获得不同状态下设备的统计图,分析统计图可以直观评估设备利用率与设备负荷是否合理。
(3)对各分系统进行集成试验、集成验证及最终确定。
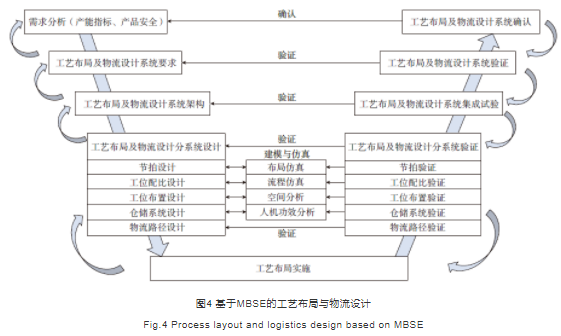
3 装配系统设计
数字化装配系统的本质是为实现关键装配工艺环节而构建的复杂数字化集成系统。在 MBSE 设计框架下,数字化装配系统设计的外部输入来源于飞机大部件智能装配生产线的功能和技术指标分解,特别是关于调姿对合、制孔、锪窝等关键装配工艺环节的功能和技术指标要求。针对特定外部输入,对实现关键装配工艺环节所需的系统结构、行为逻辑、参数定义、输出结果进行描述,从而建立相应的系统模型。基于系统模型进行机械、电子、软件及通信网络设计,在设计过程中基于系统模型的输出结果要求搭建仿真和物理测试平台进行测试验证和需求符合性检查,并将验证结果与需求的偏差反馈到设计端,促使设计优化迭代,最终形成与需求一致的物理系统,如图
5 所示。
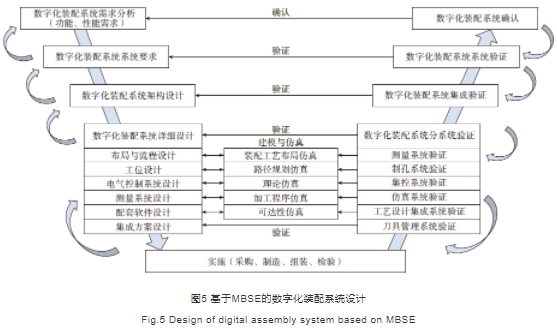
4 数字化测量系统设计
配质量的保障与优化提供精确、可靠、快速的数据反馈与支持。基于MBSE 设计框架,数字化测量系统设计的外部输入来源于基于
MBSE的飞机大部件智能装配生产线的功能和技术指标分解,主要包括被测特征(空间点、形貌等)、装配环境要求、测量效率及测量精度等。根据这些技术指标,从环境适应性、测量精度、测量可达性、测量效率等方面对数字化测量系统应具备的技术指标进行细化及系统架构设计。在此基础上,对数字化测量系统的组成要素,如测量工艺规划软件、测量设备组网方案、测量自动化系统等进行设计,并基于相关的数据模型和仿真软件对系统设计方案进行验证及优化。最终,通过设计优化迭代减小设计指标与输出参数之间的差异,最终形成与需求一致或接近的物理系统,如图
6 所示。
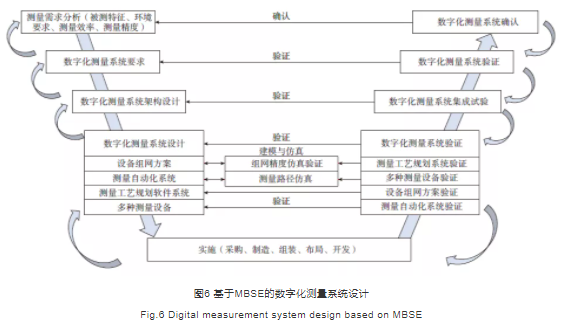
5 集成工作平台设计
集成工作平台集“气、电、网”于一体,是满足数字化装配需求的集成工作平台,融合稳定性、耐用性、制造工艺、安全美观以及人机工程、智能化装配发展方向需求等多个维度要求,实现工具按工位配置,工具、样板合理分类及形迹化管理。
MBSE 框架下的集成工作平台设计如图 7 所示,首先在系统布局设计阶段,根据后期装配加工的具体场景,梳理分析所需设备设施及操作流程,并将所需设备、工装存放架、工具柜、样板存放架、物流进出路线、操作区域及装配对象和工装等在工作平台上进行全要素布局设计,以减少对操作人员的管理难度和非增值活动浪费。其次,根据系统布局情况对集成工作平台的结构形式、尺寸规格以及所需的电气(照明)系统、气源系统、网络系统和附属设施(工具柜、样板架、电脑柜、生活物品柜等)等分系统进行详细设计,并通过有限元及可达性、人机工程等仿真手段对分系统设计准确性进行分析验证。
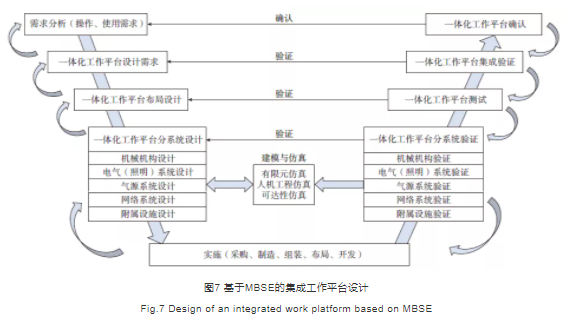
飞机大部件智能装配实施验证
成飞公司在构建飞机部件智能装配生产线过程中,对基于 MBSE的大部件智能装配能力建设方法开展实践,已完成对装配工艺设计系统、装配系统、测量系统、集成工作平台、工艺布局与物流设计系统、装配过程智能管控系统的初步验证。围绕飞机大部件数字化装配全过程,开展多段位自动化装配单元的建设,形成以数字化、网络化、自动化、智能化为核心的智能装配能力,实现了部件精确装配与数字化环境的深度融合,以及物流、工艺、制造、设备等多维度信息融合,并逐步建成了数字化装配生产车间,如图
8 所示。
装配工艺设计方面,开展工艺协调依据的规范化应用、工艺规范与管控、工艺数字样机等技术研究与应用,构建了层级分明、梯度清晰、功能完整的数字化工艺协调体系;开展基于
MBD 的容差分配、基于 MBD的 MBOM 顶层设计、基于特征的工艺文件智能编制等技术研究与应用,构建了完整的基于
MBD 的数字化工艺设计体系;发展装配仿真、流程仿真、生产系统仿真等先进综合仿真技术,搭建了面向工艺设计日常应用需求的工艺仿真与评审平台,实现了传统桌面式工艺仿真和
VR 工艺仿真与评审的互补融合 , 大幅提升了工艺设计的效率与质量。
装配系统建设方面(图 9),开展多段位自动化装配单元的建设,完成了前机身、中机身、中机身对合、对合精加工、机翼等装配单元的建设,通过工业机器人、高精度数控机床、AGV
运输等先进设备的集成应用和综合管控,实现调姿、对合、连接、检测、制孔等装配过程自动化,单孔制孔效率提升
230%,单孔精度能力系统提升 400%,对合及精加工效率提升 100%。
测量系统建设方面,发展面向高精度、高效率飞机制造的数字化测量体系,使测量不仅仅是质量检测的手段,而且融入产品制造、装配的各个环节,形成产品质量的闭环控制。如图
10 所示,在激光跟踪仪、激光雷达等数字化测量技术的支撑下,各个环节所获取的测量数据能够形成统一的测量数据集,能够将原始数据、分析结果等数据反馈给上游的设计部门,为产品
/ 工装设计、材料选择、装配 / 制造工艺优化、测量方案改进等提供有效的数据支持。
集成工作平台建设方面(图 11),针对各工位工作平台的具体操作流程及所需设备设施,结合可达性、人机工程仿真对工作平台布局进行分析,找到最佳的平台布局方案,实现了对工具、样板合理分类及形迹化管理的目的,满足精益生产管理的要求。
工艺布局与物流设计方面(图12),结合流程仿真与工艺布局仿真,对生产节拍、生产参数调整及生产瓶颈等进行分析,评估飞机装配各段位间的生产布置,找出最佳工位布局方案,从而达到改善生产线物流运输、提高生产效率的效果。
飞机装配过程智能管控系统建设方面,以 PDM、ERP、MES、车间级信息协同平台等业务系统为信息源,综合应用虚拟车间构建与仿真、孪生数据构建与管理、模型轻量化等技术,建立虚实映射的“数字孪生”模型,构建了涵盖生产、设备、物流等业务的车间管控平台,基本实现了飞机装配多维度、分层级、全要素的可视化管控。
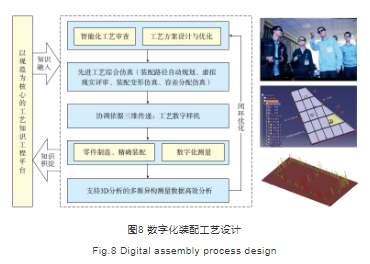
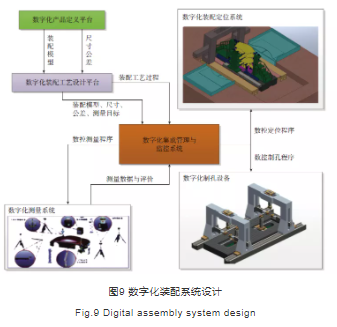
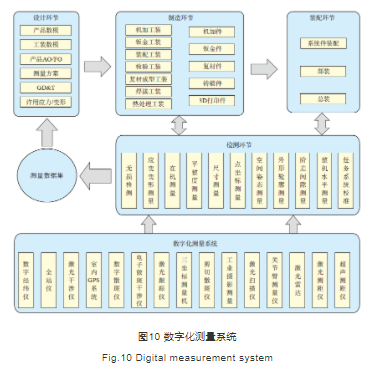
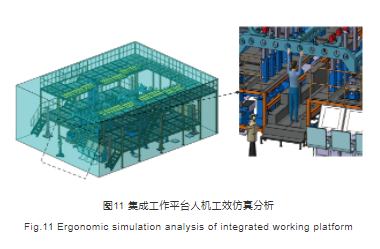
<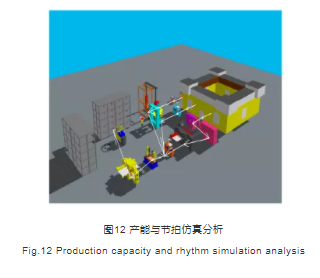
结论
飞机大部件智能装配能力建设是一项复杂的系统工程,需要采用科学的方法进行整体的规划建设与全局的持续优化。本文基于系统工程的思想理念,提出应用
MBSE 科学开展飞机智能装配体系能力建设的方法,并在成飞公司开展应用实践,取得了阶段性成果,初步实现智能制造中“精准执行、动态感知”的局部特征。在下一步工作中,将继续实践应用该方法,持续开展工艺大数据挖掘与决策分析、专家工艺数据库构建、增强现实辅助飞机智能装配、数字孪生等方面的研究,建成具有完整“精准执行、动态感知、实时分析、自主决策”特征的智能装配能力系统。
|