编辑推荐: |
本文主要介绍了数字孪生的智能制造内涵及其在数控加工的应用 相关内容。望对您有所帮助。
本文来源于搜狐,由火龙果软件Linda编辑,推荐。 |
|
1 引言
数字孪生在学术界和工业界已经引起了广泛的研究和应用探索,作为物理世界的数字化映射,数字孪生应该如何助力智能制造的发展是当前该技术发展的关键。在某一项技术的广泛应用之前,需要经过严谨的概念定义与确定的实践验证过程。但是,在近几年数字孪生的发展过程中,却存在概念不统一、解读不一致、实现有偏差等问题。其原因在于尽管现有研究对数字孪生的架构和组成做了一些抽象的描述,但数字孪生的内涵及其潜在思想并未被论证清楚。2003年,Michael
Grieves教授首次提出“镜像空间模型”的概念,随后由美国国家航空航天局(NASA)正式命名为“数字孪生”。但这个定义仅说明了数字孪生的表现形式,对其内涵思想、实现方法、适用范围都未作明确的规定和解释。造成了后人在解读数字孪生时,产生了莫衷一是且较为混乱的表达定义。
2017年,Rikard Söderberg等指出数字孪生的作用在于将设计与预生产阶段常用的仿真能力拓展到实时运行端,并对产品与生产系统进行优化,这一观点较为忠实的反映了数字孪生的原始目的;刘检华、熊辉等在回顾研究Michael
Grieves教授的研究中总结了数字孪生体的概念模型的组成主要包括:实体产品、虚拟产品和数据信息交互接口;陶飞等提出数字孪生车间由物理车间、虚拟车间、车间孪生数据和车间服务系统组成,以实现物理融合、模型融合、数据融合与服务融合;Benjamin
Schleich和Nabil Anwer等提出采用增强容差表达能力的皮肤模型来加强数字孪生的模型表达能力。2018年,戴盛等针对数字化从产品定义,对从数字样机到数字孪生的发展过程进行了综述,强调了高保真的建模仿真、高置信度的仿真预测、高实时的数据交互以及大数据应用是数字孪生的支撑技术。2019年,陶飞等又提出了数字孪生的五维模型,包括物理实体、虚拟实体、服务、数据以及连接。上述研究对数字孪生概念的推广起到积极的作用,使得研究与产业界逐渐开始重视数字孪生在智能制造中的价值与地位。但很多概念研究只是对如何实现数字孪生进行总结,并未解释清楚数字孪生所要解决的具体问题,也并未辩证与其他现有技术的区别。有些定义还存在一定争议,比如数字孪生是否包括物理实体?服务是否为数字孪生必要的组成部分?连接是否越实时越好?仿真的保真性与实时性如何并存?数字孪生与其他概念(数字样机、硬件在环仿真、多物理场仿真)的区别与联系?2020年,张霖提出了对模糊的数字孪生概念定义的冷思考,并强调了建模和仿真是实现数字孪生的关键技术;Xun
Xu等对数字孪生的基本概念、与CPS和IoT的区别与联系、关联技术、研究趋势等做了系统性的综述。过去三年内,关于数字孪生的论文发表数量在显著递增,但将近40%的论文都集中来自于少数几个小组或机构的研究学者,同时也存在着内涵理解不清、缺乏参考模型、研究案例较为初级等问题。
缺乏对实际案例的抽象和总结是数字孪生的另一个问题。尽管数字孪生的概念引发了众多国内外制造业的关注,但各企业对数字孪生的理解却不同。自2004年开始,工业界的许多国外大型公司都开始采用数字孪生技术在产品设计、制造、服务等方面针对具体问题进行很多有益的尝试。法国达索公司研发的3D
EXPERIENCE平台,支持通过和用户交互反馈信息不断改进信息世界中的产品设计模型,并反馈到物理实体产品改进中。德国西门子公司基于数字孪生理念构建了整合制造流程的生产系统模型,形成了基于模型的虚拟企业和基于自动化技术的企业镜像。美国ANSYS公司利用其强大的有限元仿真能力开发了数字孪生解决方案,注重分析运行时(As
Operated)的数据并将其反馈至设计时(As Designed),从而实现优化。美国的STEP Tools公司开发了可以对加工质量进行实时监控的数字孪生机加系统,集成了STEP、STEP-NC、MTConnect和QIF等工业标准,是目前面向数控加工全要素建模数字孪生方向开发时间最长,以及技术完整度最高的系统,2019年波音应用该系统的STEP-NC数据流生产了100万左右的工件。英国的Emulate3D公司开发了Demo3D/Emulate3D/Sim3D系统,可以在车间级仿真的基础上实现与PLC系统的通信对接,从而达到对虚拟工厂进行柔性配置和动态开发和模拟控制的目的。这些研发工作引起人们的高度关注,并在很大程度上加速推进了数字孪生的发展进程。但与其他技术类比,在工业界依然缺乏对数字孪生的统一理解和标准定义,各个公司的数字孪生系统的定位、重点以及要解决的具体问题也不尽相同。
为了理清数字孪生的真正内涵,本文参照历史上存在及成功过的经典概念的特性,对数字孪生的抽象概念进行重新解读。对照面向对象编程的动态绑定及多态特性,分析与数字孪生的内在关联。提出与讨论了软件危机与制造危机的相似之处与可借鉴的解决方案。论证了数字孪生的运行时多态仿真是有别于现有技术框架的重要特点。综合比较与讨论了数字孪生与数字样机、硬件在环仿真、多物理场分析的区别与联系。采用UML类图确定了数字孪生与其他系统之间的关系模型,以发展出逻辑自洽的区分一个系统是否为数字孪生的关键原则。总结与分析了数字孪生发展的主要问题与瓶颈,以形成可行的数字孪生实施准则。最后,以面向数控加工的数字孪生系统为案例,对本文提出的“面向孪生的制造”的新模式进行原理阐述与理念验证。
2 数字孪生的抽象内涵
2.1 数字孪生概念模糊的原因
一般经典的概念都会经历从抽象到具象的过程。但当下引起广泛关注的数字孪生则有所不同。自数字孪生的概念被提出以来,其内涵反而变得越来越模糊。这种情况,与一个具有大影响力和长生命力的概念相比,有很大不同。举例而言,制造业在历史上产生了很多抽象概念,都成为了解决具体问题的经典方法;比如,JIT、精益制造、参数化设计、数字样机等,开始都是源于某一概念。在计算机领域的发展历程中,类似具有影响力的抽象概念更为普遍;比如,面向对象、泛型编程、面向切面编程等。根据历史的概念总结,可以推论,一个可能经典的概念应该具有以下几个特点:
1)内涵抽象、方法普适而问题具体;
2)与现有方法存在排他性的维度区分;
3)能够产生较大的社会经济效益。
例如,面向对象的概念是抽象的,但是面向对象解决了设计大型程序时规范的架构思想和工具,这个优点是面向过程语言难以逾越的,因此C++和Java等面向对象语言获得成功,成C/S架构与B/S架构的主流语言;参数化设计思想规范了CAD的设计过程,以及提供了模块化修改的可能,因此,发明了参数化设计概念的PTC公司(PTC即参数化设计的缩写)在历史上使得“其他CAD软件在一夜间变得落伍”。因此,要使数字孪生的概念产生经典的效果,完全满足以上三条特点,还需解决以下疑问:
1)数字孪生通常被解释为“连接物理世界的数字化镜像”,物理世界的数字化镜像是一种方法或手段,而不是具体要解决的问题。通过定义,可以合理推论,数字孪生与数字样机、硬件在环仿真、多物理场分析等已经形成了一定应用效应和成熟商业软件的历史概念存在很强的关联性,或者可以推论数字孪生是上述三类概念之和,这三类概念所要解决的问题都是“更为全面的表达与更为精确的仿真”,那么是否可以认为数字孪生也是要解决“更为全面的表达与更为精确的仿真”的问题呢?
2)数字样机重在模型,硬件在环仿真重在连接,多物理场分析重在仿真,这几乎涵盖了一般的数字孪生概念研究中所强调绝大多数要素。但数字孪生并不等于数字样机+硬件在环+多物理场分析;因为,如果是这样的话,就违背了第二条原则“与现有方法存在维度区别”。维度是不能对已有方法进行简单的加法来实现的。例如,采用面向对象方法,无论花多少时间,都是无法达成泛型编程(模板元编程)的效果。
3)数字孪生能够产生较大的经济效益。例如,现在国内许多工厂都在开展数字孪生的项目(大部分采用的是Unity3D+数据库的解决方案)。那么,这些数字孪生系统具体在解决企业与工厂的故障诊断、数据监控、智能排产等问题。不过这些问题与MES、ERP等系统的目标又有些趋同,而不具有技术性的排他性。此外,难以发展出内涵抽象、方法普适而问题具体的效果。
正因为如此,数字孪生的概念在当前的发展过程中变得越来越模糊。企业对数字孪生的解释也莫衷一是,重点各有不同。为了解决上述问题,本文试图用参照性分析的方法,对照面向对象与数字孪生两种概念,来获得具有一定严谨性的解释。
2.2 面向对象编程与面向孪生制造
面向对象是一个成功的概念,对应的方法包括继承、重载和多态。其中,继承解决了is-a的耦合关系,重载提供了函数参数决定行为的运行模式,多态使得统一的接口可以绑定不同的行为。这三种方法提供了对同一族类进行批处理的可能,提升了大型程序的开发效率,这对面向过程语言来说是维度性的提高。其中,C++的多态是通过虚函数来实现的,而虚函数是通过函数指针的功能完成的。函数和虚函数非常像,但是体现的思想截然相反。数字孪生与仿真也存在类似的比较问题,他们很像,但体现的思想却截然不同。事实上,函数和虚函数体现的思想与仿真和数字孪生体现的思想是可以参照对应的。函数与仿真类似,体现的是静态绑定的思想;虚函数与数字孪生类似,体现的是动态绑定的思想。以下给出编程语言中,静态与动态绑定的定义与对比:
1)静态绑定:函数的行为在编译时决定,而且在运行时不能变;
2)动态绑定:函数的行为在运行时决定,而且在运行时可以变。
套用类似的思想,传统仿真可以理解是静态绑定的:仿真的行为在仿真阶段确定,数字孪生是动态绑定的:仿真的行为在执行阶段确定。就如同虚函数本质还是函数(通过函数指针来实现)一样,数字孪生的本质还是仿真,只不过是动态绑定的仿真。这就可以解释,为何数字孪生与仿真如此相像,却又存在相互对立的关系的原因。动态绑定是面向对象的前提,没有动态绑定就无法实现多态,也就是无法实现面向对象;因此,动态绑定意义重大。而面向对象对比于面向过程的高维优势是显而易见,这就可以满足一个经典概念的三条特性。以下给出制造仿真的静态绑定与动态绑定的定义:
1)静态绑定:仿真的行为在制造前决定,而且在制造时不会变;
2)动态绑定:仿真的行为在制造时决定,而且在制造时可以变。
根据数字孪生是动态绑定的仿真这一定义,继续分析与拓展。
首先,由于需要实现动态绑定,就必须与物理端通过一定的频率进行数据同步。数据同步可以通过连接来实现,但是不一定必须通过连接完成。例如,在数据采样频率要求比较低的装配场景,人工输入误差数据完全可以满足操作要求,温度可以通过连接采集,同样也可以通过红外视觉采集,形式并不重要,关键是数据的实时获取。从数据到仿真模型的传输过程中,还需要关注一个重要的问题:数据如何转换为信息,因为只有有效的信息对仿真模型才有意义,具体结合业务的信息才是有作用的。
其次,数字孪生需要建模与仿真技术作为支撑。这就如同虚函数需要函数作为支撑一样,脱离仿真技术谈数字孪生是无意义的,也只能形成虚的概念,或者与已有技术趋同,或者毫无实际用处。在讨论仿真技术时,需要注意,不同领域的建模与仿真技术有很大区别的。只有深入理解了不同仿真技术的基本思路与优缺点,才能确定需要动态绑定的数据与信息,实现解决具体业务问题的升维方法。例如,机器人的模型重在运动学与动力学,而制造模型重在几何与工艺的表达,差异性很大,不能单以建模进行简单统称;运动规划的仿真重在实时性,而有限元仿真重在计算精度,不能用仿真一言以蔽之。
再次,数字孪生的动态绑定的最终目标是为了实现多态式的仿真。多态可以统一控制接口,以及自适应决定仿真与决策的行为,从而为顶层系统提供批处理的可能。在产品的加工阶段,多态仿真可以单个加工工件与加工设备进行个性化的仿真分析,从而采集大量的有用信息并进行统计分析;在产品的装配阶段,多态仿真可以记录单个产品在整体装配流程中产生的大量误差数据,形成个性化的装配产品样机,为数据分析、质量回溯、容差预测等提供依据;在产品的使用阶段,各个产品可以拥有自己的数字样机,记录在整个产品生命周期中的各类运行数据,提供各类运行服务,且可以进行整体统计与分析。
动态绑定本身并不是C++面向对象特有的,早在C语言的函数指针就产生了类似的概念。但是,动态绑定可以催生面向对象,而面向对象就是C++/Java等语言区别于C语言的最重要特点之一。从这个角度来看,动态绑定的仿真极有可能催生面向孪生的制造。而面向孪生的制造则可以有无限的遐想空间,且不必担心落入与传统技术的“趋同陷阱”。面向对象与面向孪生的相关概念对比见表1,由此可知,面向对象编程与面向孪生制造是很有可能产生较强的对偶关系。当前的产品制造流程几乎都是面向过程的,就如同上世纪70~90年代的C语言一样,一旦面向孪生的制造模式可以实施,极有可能再现类似面向对象的成功模式,从而引发新一轮的制造革命。
表1 面向对象与面向孪生的相关概念定义的对比
特性概念定义面向对象 面向孪生属性 类变量 数字模型行为 函数 仿真静态绑定 普通函数 运行(制造)前仿真动态绑定
虚函数 运行(制造)时仿真数字孪生={数字模型;运行前仿真;运行时仿真}模式 面向对象编程 面向孪生制造类
类对象={类变量;普通函数;虚函数}
从上述分析来看,数字孪生的意义非常明确,就如同类定义是实现面向对象编程的重要基础一样,数字孪生也是实现面向孪生制造的重要基础。因此,为了明确数字孪生的最终目的以及规范数字孪生的内涵定义,有必要对Michael
Gieves教授提出的概念进行补充:数字孪生是连接物理世界的数字化镜像,以实现动态绑定的同步仿真。之所以需要在数字化镜像的基础上进一步强调数字孪生仿真的动态绑定特性,是因为在计算机技术的发展历史上,动态绑定起到了从结构化编程转变为面向对象编程的桥梁的作用,这一变化在历史上是革命性的,而那场革命使得软件危机问题得以有效解决。例如,C++语言用以实现多态的虚函数是通过函数指针来实现的,所以动态绑定可以催生多态,而多态又是类与面向对象的重要基础。C/C++从动态绑定、多态到面向对象的演变过程如图1所示。
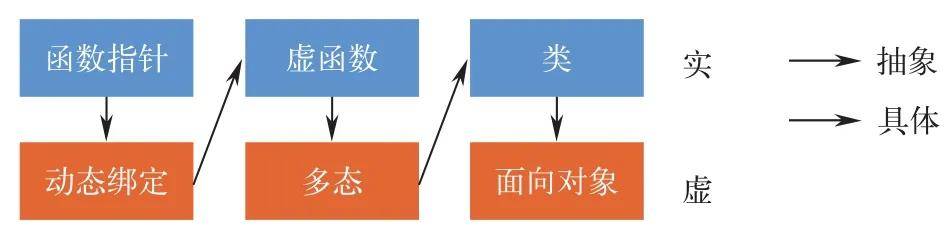
图1 从动态绑定到面向对象的演变过程
2.3 软件危机与制造危机
上世纪70年代前后,计算机行业爆发了著名的软件危机(Software Crisis)问题。所谓软件危机,指的是落后的软件生产方式无法满足迅速增长的计算机软件需求的矛盾;也就是说,并不是软件开发的可行性问题,而是软件开发的效率问题掣肘了计算机软件的发展。当前生产制造环节中的自动化装备(数控机床、工业机器人等)主要还在执行与硬件绑定的结构化语言(G代码、机器人代码等),这种工作模式与上世纪60~70年代计算机普遍使用的汇编语言本质上并无差异,如图2所示。相比而言,当下的智能制造行业是否也存在类似的制造危机(Manufacture
Crisis)的问题呢? 既然落后的计算机编程方式(汇编语言)是导致软件危机的根源,那么落后的数控机床编程方式(G代码)是不是导致制造危机的根源呢?
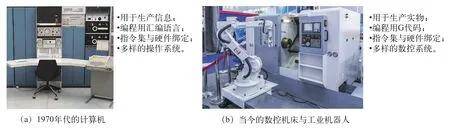
图2 1970年代的计算机与当今的工厂自动化设备
本文认为,当前的制造业确实存在类似的制造危机——落后的产品生产方式无法满足迅速变化的个性化产品制造需求。在工业4.0与智能制造的提出之时,单件小批量产品的制造是一个典型的目标问题,反应了个性化(多样化)产品的制造需求。随着认识的深入,可以发现,多样化的产品制造需求不仅仅存在于单件小批量的生产过程中,大批量生产的产品同样可能需要根据实时数据进行动态工艺调整,这时每个产品的制造过程也可以呈现出程序的多样性。这种多样化的编程方式给工艺人员带来了巨大的编程压力,使得柔性制造的方法很难大规模实施。具体而言,CAD/CAM的工艺员需要针对每台机床设备的配置进行G代码的后置,造成即使加工同一零件,也需要进行适应不同机床硬件配置的编程与仿真。车间生产线为此必须固化所有的加工流程,任何的状态变化都很难被原有的生产流程所兼容。在这种情况下,加工程序的多样化需求就会给现有的生产模式带来巨大的挑战。
1975年,Frederick P. Brooks在其所著的对软件工程产生深远影响的著作《人月神话》中提出:面向对象是当时可能解决软件危机的最富希望的方案。迄今为止,事实证明了这一论断是正确的。通过类的抽象封装与继承、多态的模块化设计,面向对象可以有效地对抗软件需求的多样性,从而极大地提高编程效率。既然面向对象是解决软件危机的有效方案,那么面向孪生是不是解决制造危机的有效方案呢?数字孪生组合的运行时仿真能力能够给制造危机的解决提供一种可能,利用孪生体的封装性和多态性可以类似于面向对象,为制造装备、工件、资源建立孪生对象。CPS组合数字孪生的架构为这种新型的制造模式提供了支撑条件,从而可以创造出“一切皆孪生,孪生即服务”的新概念。一切皆孪生(Everything
is a Digital Twin)的意思是,任何需要参与到任务协作的对象(如机床、工件、刀具等)都可以是孪生体;孪生即服务(Digital
Twin As a Service)指的是,在具体实施数字孪生时可以采用CPS的微服务架构,让孪生体的表现行为与微服务并无二致,从而可以更好的与其他服务相互融合。体现这一思想的具体案例将在本文的第5章给出。
发挥出数字孪生的作用的前提是建立相应的使用与开发原则。在面向对象理念的长期发展过程中,总结了许多非常经典的应用原则,如单一责任、里氏替换、接口隔离、迪米特原则、依赖倒置和开闭原则等。不按正确的原则构建的面向对象软件程序往往达不到好的效果,同样不按正确的原则构建的面向孪生的制造系统也可能难以面临多样性制造需求的挑战。面向孪生的结构化模型与开发原则如图3所示。
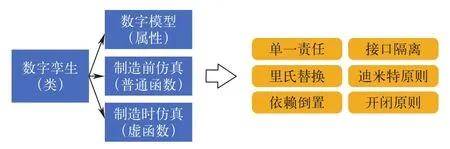 图3 面向孪生的结构化模型与开发原则
3 数字孪生的技术差异
从数字孪生的概念提出伊始,就与很多技术产生了不可分割的关联。其中,仿真技术与数字孪生的联系最为紧密。在解释数字孪生概念时会提到:数字孪生是物理世界的数字镜像,这很像仿真,但数字孪生比仿真更多。其实,可以大胆的定义,数字孪生是一种广义的仿真,是传统仿真技术的拓展和延伸。虚函数当然还是函数,只不过是动态绑定的函数;数字孪生也是仿真,只不过是动态绑定的仿真。基于这个观点出发,重点阐述数字孪生与其他技术的差异与联系。
3.1 数字孪生VS数字样机
数字样机,指在计算机上表达的机械产品整机或子系统的数字化模型,其作用是用数字样机验证物理样机的功能和性能。从定义看出,数字样机重点在于数字化模型。这一定义与数字孪生几乎一致,只要将数字样机连接到物理端,就是目前研究与应用界翘首以盼的数字孪生。但是,事实并非如此。如果真这样理解,完全可以将数字孪生等效为数字样机的一个拓展应用,不可作为一个独立的概念进行发展。借助静态绑定和动态绑定的定义,可以这样理解数字样机和数字孪生的联系与区别。数字孪生可以借助数字样机作为基础,就如同仿真也可以用数字样机作为对象一样。在这个角度上,无需对两个概念进行对立分析,或者说,数字孪生就是数字样机的一种派生。
但是,数字样机却不是数字孪生。根据数字样机的作用可以看出,数字样机重视对物理对象的数字化,以达到在数字环境下对产品或设备进行数字化表达与仿真实验的目的。一般,这种数字化表达与仿真实验都是在产品或设备的研制阶段完成,之后就几乎不再改变了。同一批次的产品和同一型号的设备都将遵循数字样机的设计与分析结果,来获得统一的生产质量和较高的生产效率。不过,当产品或设备内部存在差异时,数字样机是无法完成最优规划的。例如:在数控加工中,由于刀具磨损、机床老化造成的对同一零件的最优工艺的差异;发动机装配中,复杂装配误差的累积造成了同一批次的发动机的寿命和一致性存在显著区别。这时,采用统一的数字样机模型是难以反映不同产品与设备的差异性的。针对上述问题,就需要采用数字孪生的动态绑定功能来组合多样与时变的设备状态以及产品偏差。经过动态绑定时变多样数据的数字孪生系统就可以根据静态的数字样机与动态的运行数据来进行综合预测分析,从而推理出动态调优的控制策略,达到产品质量最优和成本最低的目的。这时,尽管产品、设备、工艺是一致的,在具体生产过程,每个数控工件、每台发动机使用的工艺参数却都可能不一样,但整体效果却是最优的。这种制造模式很像面向对象设计的多态(同一接口绑定不同的行为),因此可以将这一模式称为多态制造。由于多态在执行时不需要脑力干预,所以这一做法将极大地减轻或取代脑力成本。更进一步,这一原理如果可行,同样可以应用于单件小批量的生产当中,实现减低成本与提高效率的目的,从而部分达成智能制造的个性化制造的目标。
从上述分析可以看出,数字孪生的推崇者并不需要急于摘清数字孪生与数字样机的区别,甚至可以大胆的承认数字孪生就是is-a数字样机,即数字孪生与数字样机之间的关系是继承。但是,数字孪生继承于数字样机,又组合了时变多样的运行数据,因此数字样机并不是数字孪生。这一关系,如果画成UML类图,就如图4所示。
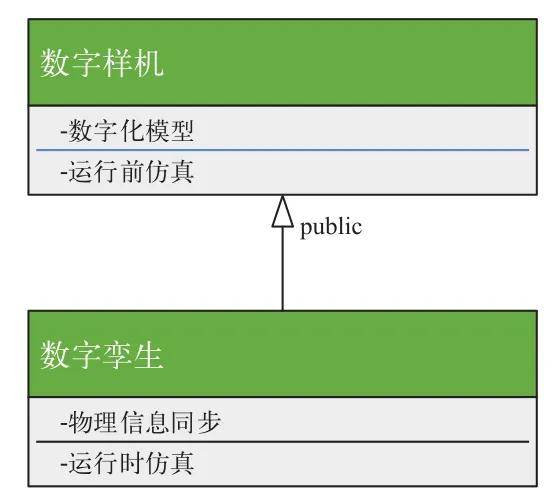 图4 数字孪生与数字样机之间的继承关系
根据面向对象中继承的里氏替换原则:父类能够存在的地方,子类一定能存在;子类能够存在的地方,父类不一定能存在。这就说明,数字样机存在的地方,数字孪生就一定能存在;数字样机所需要实现的目的,数字孪生一定能满足(前提是这是一个完善的数字孪生系统),因为“A
digital twin is-a digital mock-up”。一旦意识到数字样机与数字孪生的这种关系与计算机科学存在等效关系时,需要非常谨慎的对待数字孪生的概念定义了。因为,计算机科学是非常严谨的,对规则的定义非常严苛,对逻辑的反例零容忍,不容随意对数字孪生冠以各种虚无的定义,否则极其容易在实践中陷入自相矛盾的境地。历史上,不能形成严谨定义以及逻辑自洽的编程语言几乎全被淘汰了,这就是数字孪生技术目前所面临的最大威胁。
C++的发明者Bjarne Stroustrup曾说明,面向对象的逻辑关系非常容易让人在具体执行过程中陷入误区。is-a的耦合关系是非常严谨、严苛和残酷的,现存的数字孪生研究中有很多都不符合is-a
digital mock-up的定义,不能实现数字样机的功能的系统不能被称之为数字孪生。原因很直接,不如此定义将难以辨别数字孪生与其他现有系统的区别;例如,示波器不是数字孪生,尽管示波器可以实现对电信号进行实时采集与分析的功能。
3.2 数字孪生VS 硬件在环仿真
硬件在环仿真(HIL)指的是以实时处理器运行仿真模型来模拟受控对象的运行状态,通过I/0接口与被测对象相连接。根据定义,可以看出硬件在环仿真的重点在于仿真系统与物理对象的连接。显然,数字样机并不是硬件在环仿真的关注重点,所以可以确信硬件在环仿真不是数字孪生。但是,仿真、连接这些元素又是数字孪生所需要的。其中,仿真能力是数字样机本就具备的功能,由于缺乏多样数据作为支撑,其更大的意义在于运行前的准备阶段。正因为如此,这两种仿真其实存在很大区别:由于硬件在环仿真系统需要对现场数据进行跟随,对实时处理能力要求更强,所以可能会损失仿真精度;数字样机的仿真偏向于准备阶段,对时间效率要求并不高,而更追求仿真的保真性。硬件在环仿真的实时性恰恰是数字孪生所期望的,许多研究对此产生了极大的兴趣,不过也会因此产生“只要实现了硬件连接和仿真分析就实现了数字孪生”的误解。不能忘记数字孪生是数字样机这一定义。如果将数字孪生看成传统数字样机的升级版,数字孪生将承担着向下兼容的义务:数字孪生系统在与物理系统连接之前,首先应该满足数字样机的功能,即数字化模型是必不可少的。
由于缺乏模型的支撑,使得硬件在环仿真所针对的仿真对象是确定固化的,其结构与参数无法随着时变与多样数据的变化而变化。这使其在面对多态式仿真的需求时无所适从。为了满足仿真的实时性,硬件在环仿真系统(如图5所示)会将确定的模型用上位机开发好,然后以机器码的方式烧录到高性能控制模拟器。这种方式虽然尽最大可能获得了高效性,但是代价是损失了仿真系统对模型的理解和多态的柔性。没有模型,将失去时变多样数据的载体,因此只能应用于确定性的场景当中,无法获得运行时多态仿真的效果——绑定不同物理对象时具有不同的仿真效果。仿真模型的建立与修改主要在上位机完成,这时开发系统对模型是理解的,对修改也是柔性的,将这种柔性称之为开发时多态。
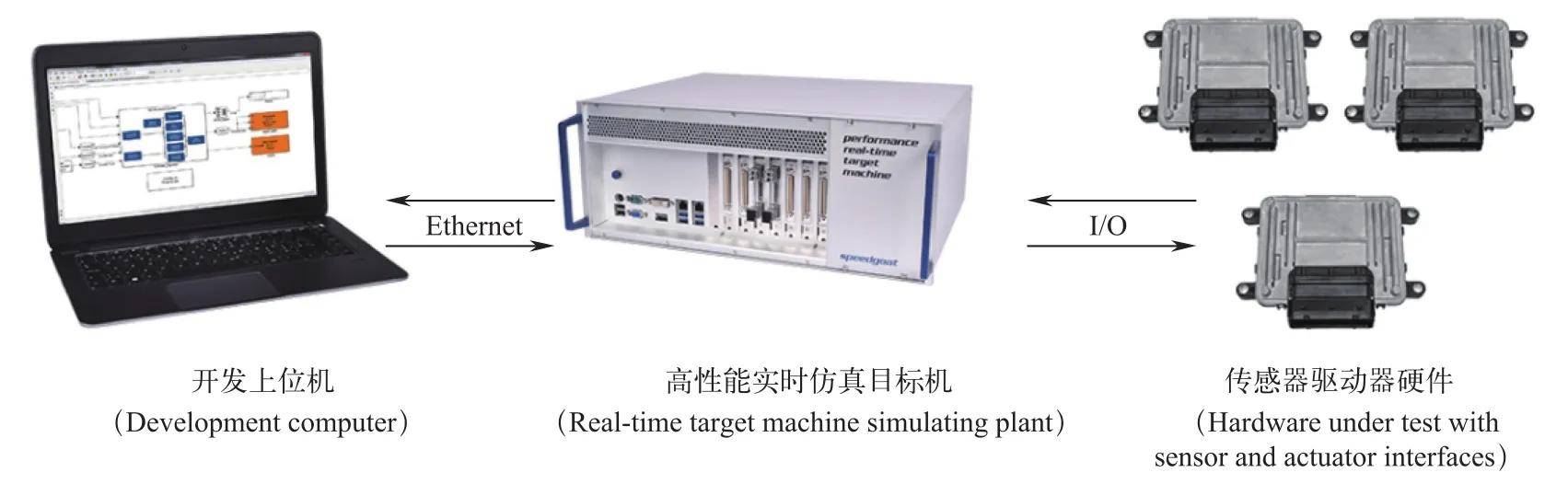 图5 硬件在环仿真的软硬件架构及工作原理[19]
然而,缺乏模型并不意味着硬件在环仿真系统的技术落后。正因为硬件在环仿真舍弃了对模型的理解,才能够用二进制的计算方式实现对硬件系统实时模拟。这一优点是数字孪生系统无法比拟的。这也就暗示着,不同的技术有其不同的适用范围,数字孪生也有其缺点,并不能一统天下,取代所有其他相关技术的地位。考虑到当前计算机架构的计算极限,需要认清:fast/good/cheap,三者取其二,不可取其三。不同的问题需要采取不同的技术思路解决,尽管有些应用看起来类似,但是响应的最优解决方案却存在着根本的区别。
由上述分析可以看出,数字孪生与硬件在环仿真的关系在于组合,如图6所示,即数字孪生并不等同于HIL,只是利用了HIL的部分功能——“A
digital twin is implemented in-terms-of a HIL”。数字孪生期望借助硬件在环仿真的数据采集能力和实时仿真能力来实现运行时仿真的目的。由于动态绑定是多态的前提,只有实现了运行时仿真,才有可能实现多态式仿真。然而,数字孪生仿真与硬件在环仿真又有所区别。由于数字孪生需要关注对历史数据的关联以及将来趋势的预测,数字孪生的仿真需要理解与更新模型。相比而言,硬件在环的仿真不需要关注模型随时间的变化,所以并不需要关心模型本身,而尽可能多的将计算资源放在对物理对象的实时模拟方面。但是硬件在环仿真的开发调试阶段是需要了解模型本身的,也需要能够柔性动态修改模型的结构和参数来获得开发柔性。因此,数字孪生真正组合的是硬件在环仿真开发时的仿真能力。这一做法类似于计算机语言中运行时多态和编译时多态的区别。硬件在环仿真只能支持开发时多态,理想的数字孪生系统既可以实现开发时多态,又可以实现运行时多态。运行时多态是面向对象的基石,编译时多态是泛型编程的基石。尽管这些专业的计算机概念在理解上有点晦涩,但确实是影响当今主流技术的思想根源。
 图6 数字孪生与硬件在环仿真之间的组合关系
还有一点需要引起重视的是,实时的连接对于数字孪生系统是相对的。由于数字孪生并不像硬件在环仿真那样,需要极致地追求对物理系统的仿真模拟速度与数据采样的速度和容量,数字孪生对数据通信速度和实时性的要求并不是那么苛刻。一方面,尽管开放式系统和网络技术的普及让我们对设备与产品数据的索取能力得到了大幅提升,但是不容忽视的事实是,对数据通信的实时能力和信息能力永远应该持谨慎态度。实时能力,指的是以最小周期准时地获取物理对象的数据;信息能力指的是物理对象在数据中提供真正所需信息的能力。以西门子的数控系统840Dsl为例,用OPC-UA接口以小于100ms的速度进行数据采集时,有可能会显著影响数控系统的插补速度。这一影响对数控系统来说是极为严重的,因为可能因此而直接影响加工质量和生产安全。此外,由于数控系统运行的是G代码,其本身并不了解具体的加工对象,因此数控系统的信息能力也大打折扣。另一方面,应该仔细分析数字孪生模型对数据的具体需求。原则上,数字孪生系统对实时数据的采样应该周期越长越好,数量越少越好,而非尽可能的快和多。盲目而密集的数据采集一方面极大占用了控制系统的计算通信资源,另一方面消耗了数字孪生端海量的存储空间。在缺乏具体的业务需求的前提下,这些消耗是极不明智的。这也就意味着,只要能够满足信息获取能力,甚至物理连接也不一定是必须的。例如,在发动机装配过程中,由于装配工艺本身和误差数据的采样都相对非常缓慢,此外有些测量设备一般缺乏数据接口。这时,甚至可以依赖于人工输入来完成数据采集的工作。这一方式颠覆了人们对数字孪生必须要与物理模型进行数据连接的初步认知,其实信息索取和模型同步才是最终目的。一个严谨的概念定义,往往惧怕反例的存在,所以一般的原则是“依赖于抽象,而不要依赖于具体实现”。从这个角度看,数字孪生与硬件在环仿真的组合关系应该修改为如图7所示。
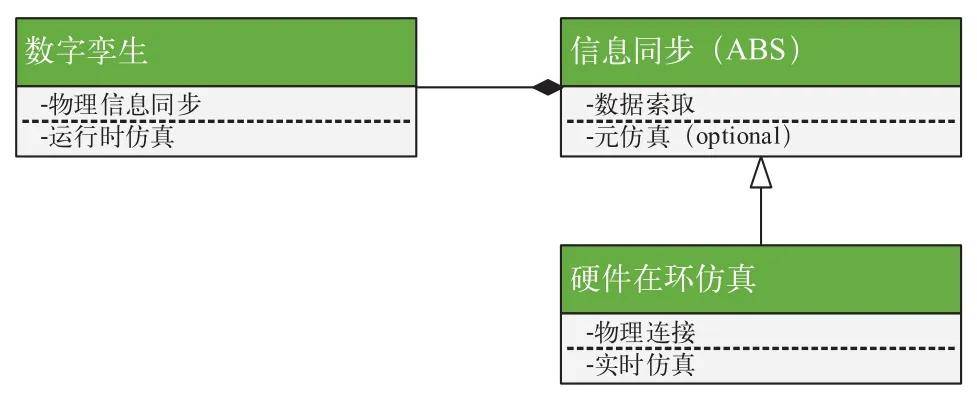
图7 修改的数字孪生与硬件在环仿真的组合关系
3.3 数字孪生VS多物理场仿真
多物理场仿真给了数字孪生无限的遐想空间。如果能够将这种多物理场仿真能力迁移到数字孪生系统中,将极大提升数字孪生的分析计算能力。但多物理场仿真的概念来源于有限元分析,有限元分析的关注点在于仿真的精度而非速度。一般高保真的仿真与实时仿真是相悖的,不可轻易同时要求。仿真精度与仿真速度的关系是成指数曲线关系的。与通信速度一样,数字孪生对仿真精度和速度的要求需要调和出一个平衡的状态,或者损失仿真精度,或者损失仿真速度。所谓的多物理场,也与具体业务相关,理性的原则是能不仿真的则不仿真,亦或是采取分时复用的机制。正因为如此,面向数字孪生的多物理仿真机制存在大量的变形。以机器人动力学仿真为例,如果追求保真性,就如同ADAMS类型的软件,尽可能保证模型精度,以及执行通用而高精度的仿真,因此仿真速度就难以实时。另一个思路更多存在于一些专业的机器人仿真器中,如在V-Rep(已更名为CoppeliaSim)的仿真环境中,几何模型与动力学模型是分开建模的。动力学模型并不需要严格遵循机器人的几何形状,转而采用一些简单的方块、圆柱、球体等多个单元体组合而成(如图8所示)。采用这种策略,虽然损失了一定的保真度,却极大地提升了仿真速度,使得机器人的准实时仿真成为可能。类似的策略也存在于基于CAE与基于CAM的加工仿真算法中。这一策略再次提醒了“三者取其二”的理性原则。如同程序的时间复杂度与空间复杂度不能兼得一样,数字孪生也必须在仿真的精度与速度方面做一些取舍,而不同的取舍方案可能带来在实现原理上的根本的不同。理性的选择应该在满足需求的前提下,不强求数字孪生系统的保真性,相反应该尽可能降低仿真的复杂性,以换取数字孪生所需的实时性。所以,在有些研究当中提及的高保真、高实时、高动态的要求,在实践中是很难同时满足的。如果勉强而为之,反而得不到最优的性能平衡,从而违背了多态仿真的初衷。
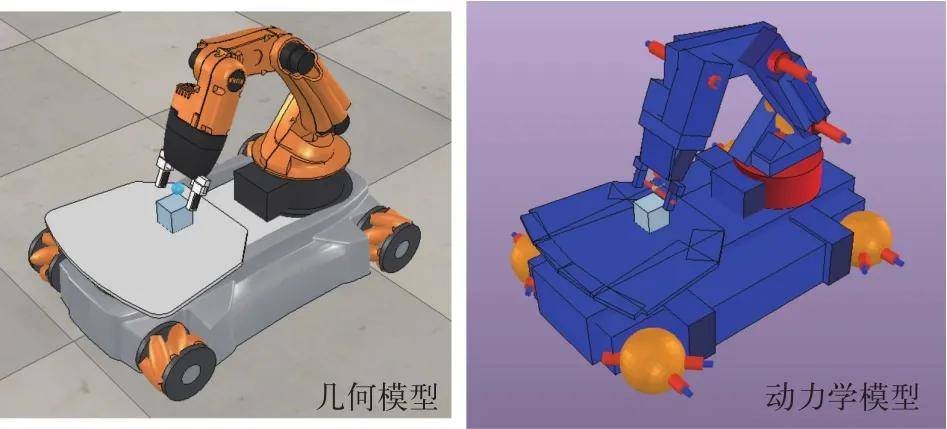 图8 实时机器人仿真平台CoppeliaSim使用的几何模型与动力学模型
由于数字孪生关注运行时多态的仿真行为,因此这种精度换速度的策略还是很值得推崇的。即使运行时仿真不能完全满足精度要求,还可以采用数字样机提供的运行前仿真(无需关注实时性)来实现对基本趋势的保证。运行前仿真不需要消耗运行时的计算资源,所以可以在一定程度上换取运行时仿真的速度和精度。这种策略在模板编程中大量使用,用编译时间来换取运行时间和空间。借助这个思路和策略,甚至有可能如模板元编程一样,衍生出元仿真的新型概念(元仿真指的是将可以泛化的仿真对象在初始化阶段编译成不同的实时仿真模块,再通过运行时多态进行反射组合)。精度换来的不仅是速度,更能够为数字孪生带来多物理场的可能,在有限的计算资源与实时性要求的前提下,牺牲精度成为仿真的唯一选择。正因为这些限定条件,造成了数字孪生的多物理场仿真与有限元多物理场仿真存在很大的不同,更为研究仿真新原理提出了更多的需求。新原理同样需要与具体的业务结合,不同的物理特性催发的仿真方法可能大有不同。这些细节的区别不可用仿真一词涵盖。C++在模板编程的基础上,进一步拓展出STL模板的编程范式。这说明,仿真算法的原理性改变有可能产生数字孪生运行的新模式。
综合上述分析,数字孪生与多物理场仿真的关系可以较为明确了。数字孪生期望借用多物理仿真的概念,但实际的仿真原理却可能存在根本性不同,这就是数字孪生对多物理场仿真的排他性体现——离线仿真代替不了在线仿真。这是一种典型的私有继承的利用关系(implemented
in-terms-of)。所以,数字孪生与多物理场仿真的UML类图如图9所示。
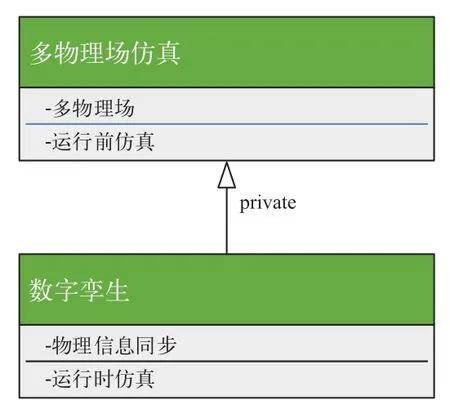 图9 数字孪生与多物理场仿真之间的私有继承关系
综上所述,基本可以看清数字孪生的全貌了,数字孪生的综合关系类图如图7所示。数字孪生,作为物理端的数字化镜像,从一开始就不是一个包罗万象的概念,所以如何衡量数字孪生的界限非常重要。虽然面向对象的概念也非常抽像,借助继承、重载、多态的关系定义,但是可以迅速而准确地判断哪些语言是面向对象的,哪些不是。同样,借助面向对象的定义方式,可以理清各种相关概念之间的区别与联系。进一步,就可以准确地判断哪些系统属于数字孪生,哪些系统不属于数字孪生。数字孪生的综合关系模型如图10所示。
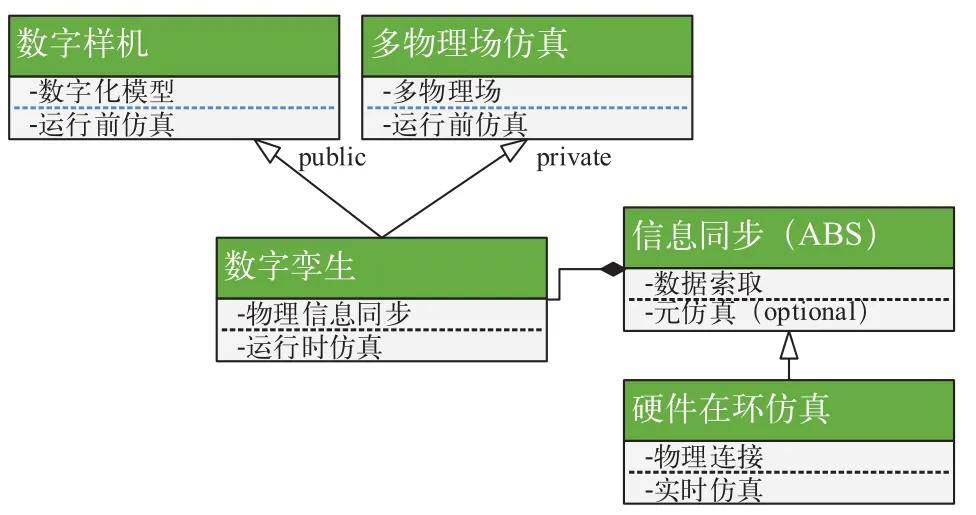 图10 数字孪生的综合关系模型
根据本节的论述分析,可以总结出界定数字孪生的基本原则:
1)数字孪生首先是数字样机,不能实现数字样机的系统就不是数字孪生;
2)数字孪生组合了信息同步接口,可以实现运行时的动态绑定仿真;
3)数字孪生借用了多物理场仿真的概念,但其实施原理有很大不同。
3.4 数字孪生VS 其他概念
近两年来,随着数字孪生的普及和深入,人们越来越期望数字孪生与CPS、云制造、云计算、大数据、IoT、AI等产生紧密的关联。事实上,不同系统之间的松耦合才是应该追求的目标。不同系统的概念耦合不但会引发宏系统的资源枯竭问题,而且会使得本就模糊的数字孪生概念更加难以让人理解。
首先,不可用数字孪生的概念去外衍或对偶CPS、云制造等技术,数字孪生关注于运行时仿真,CPS关注于架构,二者定位不同。CPS可以组合数字孪生,但数字孪生却不可组合CPS。存在两种方式实现CPS对数字孪生的组合:①可以通过接口进行平等的对接,让数字孪生关注于边缘端,而CPS关注于服务端,形成边云协同的综合系统。这样做的原因在于当物理端或控制端难以支持CPS所需的信息支撑时,数字孪生系统可以借助其信息同步的数字样机优势实现物理端的智能代理的目的。②将数字孪生作为计算模块组合到CPS系统中,利用云计算强大的算力和一切皆服务(XaaS)的解耦机制,形成微服务架构和多个数字孪生镜像。让数字孪生镜像在云端动态组合,更有利于实现多态式仿真的目的。可以将第一种组合方式称为边缘孪生(注重于实时),第二种组合方式称为云孪生(注重于继承与多态)。边云协同的CPS系统可以体现在边缘孪生与云孪生的动态交互上。
其次,需要确保数字孪生系统的独立性。封装性是一个复杂系统需要坚持的必要原则,过度地扩展又会违背单一责任原则。数字化镜像是数字孪生的表现形式,动态绑定的仿真是数字孪生的核心目标。在明确的目标作为导引之下,数字孪生无法也不需要去涵盖与取代其他成熟概念及其技术地位。这一现象就如同面向对象一样,尽管可以在自身维度形成良好的逻辑自洽已经和广泛的应用场景,但是仍然无法涵盖模板编程与动态语言的应用范围。此外,认清数字孪生系统的独立性更有利于其实现与开发,只有边界清晰的目标才能得出合理的开发步骤。“先模型、再仿真、后连接”的实现顺序至关重要,本末倒置的开发方式将很有可能陷入“趋同陷阱”或“无用论”的泥潭。
再次,应当注意数字孪生系统的兼容性。所谓智能代理,应当尽可能模拟智能体的行为。智能手机APP接入AI、大数据、云计算等服务技术已经日趋成熟,将数字孪生兼容到服务架构中才是最有价值的发展目标。与其他服务与智能系统之间的兼容性越好,就能更好地实现松耦合,数字孪生系统的发展生命力就越强。这种松耦合形成于数字孪生的运行阶段,而非定义阶段。一个数字孪生可以利用AI、大数据来增强动态仿真分析的能力,但是不意味数字孪生的定义中必须存在AI、大数据或云计算。不必过分强调数字孪生与其他技术结合的特殊性,良好的数字孪生系统应当提供数据接入与接出的标准接口,以及遵循服务与被服务的统一机制,以“润物细无声”的方式融合到智能制造大框架的整体运行中。
4 数字孪生的问题与瓶颈
当前,在数字孪生的实现中,存在的问题还有很多。有些属于对概念的理解问题,有些属于在当前技术框架下的瓶颈问题。只有对现存问题进行正确的理解和有效的分析,才能形成可行的实施原则与理性的规范标准。
4.1 模型定义的具体性与严谨性
由于数字孪生继承于数字样机,所以首先要保证数字样机的可用性,才能够探讨数字孪生的派生特性。数字样机的核心内容在于建模。具体的模型需要由具体的制造目标决定。例如,对数控加工而言,基础模型包括几何与工艺模型。STEP-NC即直接符合这些模型定义的需求,完全可以复用于加工的数字孪生系统,从而减少了大量的建模工作。STEP-NC定义加工操作(operation)的EXPRESS定义如图11所示。由该例可以看出,STEP的模型定义使用了大量的面向对象设计方法,以保证模型具有严谨性和唯一性,因此不会引起歧义。正因为这种建模方法的普适性和通用性,所以STEP标准(ISO
10303)是ISO标准化组织定义的最大标准,具有最多的子标准。AP203、AP214业已成为不同CAD系统之间交换数据的最完善的标准格式。标准化的目的就在于:提供一套无歧义,具有唯一解释的标准实现模板,以保证两套或多套不同系统之间相互兼容。所以,如果在其他业务领域存在类似的建模需求,又没有现成的模型定义时,也需要对具体业务进行严谨的建模与设计,必要时也可采用面向对象的设计理念进行定义。建模过程最忌无目的虚化,即随意采用抽象组合抽象的定义方式,因为此类模型很容易被大量的反例推翻。缺乏细节、未经辩证思考的模型也有很大隐患,因此可能造成在执行时可行性与排他性的悖论。模型的内涵在于思想,模型的精髓在于细节。只有两者兼具并且经过反复论证无误的模型才可作为数字样机的基础使用。在此基础之上,发展出的静态与动态仿真技术才能得以顺利实施。
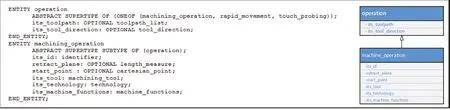 图11 STEP-NC采用面向对象对加工操作(machining_operation)的模型定义
4.2 数据采样的实时与兼容性风险
实时与高速的数据采样能力是当前数字孪生所期待的,从而产生了越实时越有利的数据采集评价标准。然而,数据采集需要从终端的控制器中获得,过于频繁的数据采集将大量占用终端控制的计算资源以及有限的实时带宽。由于控制器的硬件架构不期望过多的资源消耗在通信层面,实时控制任务一般会占据较高的优先级。所以,与高速数据采样的一般认知相反,作为物理端智能代理的数字孪生系统应该在满足信息同步的需求的前提下,尽可能的降低采样率。
即使保证了数据采样的安全周期,如果需要利用好有限的数据带宽,还需要针对数据采集的缓冲机制进行完善的设计。有些数据是周期性的,有些数据是易失的(volatile),有些数据是非易失(non-volatile)的。此外,在控制器繁忙与空闲状态的采样速度也会不同,也就是说存在速度波动的现象。这些问题如果不进行妥善设计,或者会因采样数据造成控制端的带宽浪费,或者容易造成数字孪生程序的堵塞情况。所以,绝对的实时是不可能达到的,有时需要合理的设计数据索取机制才能保证系统的同步工作。
数据采样的另一个风险在于兼容性。尽管OPC-UA、MTConnect、SCADA等技术正在逐渐深化数据索取的标准化工作,但是由于版本不同和生产设备较长的使用寿命,现存的控制器接口及协议存在很大的不一致性。标准化工作永远是工业界的一个难题。例如,在世界上只有一种TCP/IP以太网协议的情况下,工业以太网的协议竟然存在20多种之多。不一致的数据采样接口和协议很容易“穿透”数字孪生的逻辑变量层,造成运行时多态仿真的兼容性风险。如何搭建一个隔离硬件的数据索取层,对于数字孪生系统来说,既是一个技术问题,也可能由此产生灵活的运行机制。
4.3 运行时仿真能力的取舍问题
真正的多物理场仿真是一个非常消耗计算时间的问题。仿真的规模不可能无限扩张,实时性与高保真性也是天然的对立。早在十几年前,计算机刚进入到后摩尔时代,免费的性能午餐已经结束了(即不可能简单的通过提升硬件来加速软件)。在这种情况下,数字孪生的运行时仿真只能在保真、实时与多态之中,三者取其二。如果优先保证实时与多态,那么数字孪生系统必须运行在边缘端,其保真度或者仿真规模就必须有所收敛;如果优先保证实时与保真,那么元仿真模式将变得非常有用,但同时损失了运行时多态;如果优先保证保真与多态,那么可以在云端生成多个不同的数字孪生镜像来实现,但受制于通信与数据分发的延时,实时性将大打折扣。
4.4 边缘数字孪生是过渡方案
数据采样在实时与兼容性方面的瓶颈,也预示着数字孪生技术似乎并不是最完美的解决方案。尽管与物理端绝对实时同步是一个美好的愿望,但是这也是一个永远无法达成的愿望。一般控制器内部总线的通信周期也仅达到(或者只需要)毫秒级。数控机床结合数字孪生的CPS架构如图12所示,其中边缘孪生系统起到了数控机床的智能代理的角色。最为实时的信息同步方式是内存交换,这也就意味着控制器与边缘数字孪生系统合而为一。这样的控制系统称之为智能控制系统。由此可以看出,数控加工的数字孪生系统本质上是为了适配现有非智能CNC的接口的过渡解决方案。真正的智能CNC不但具有更快的数据索取能力,而且数据中的信息量也会大很多。
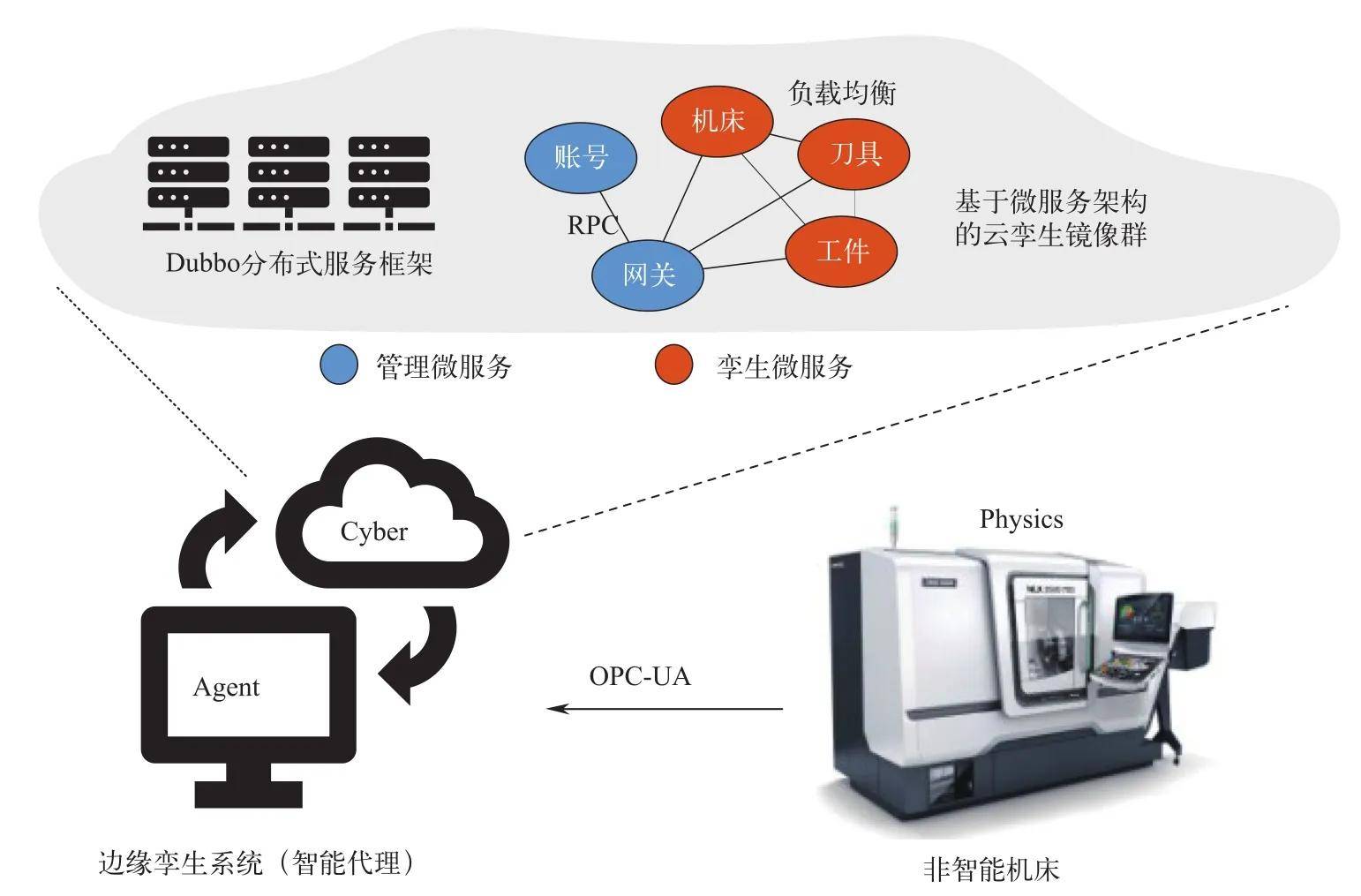 图12 非智能机床结合数字孪生的CPS架构(Cyber-Agent-Physics)
根据多态式仿真的内涵,机器人操作系统ROS就是一种符合定义的数字孪生系统。借助机器人仿真与控制组件MoveIt!和Gazebo,ROS控制的机器人可以完成一些智能的规划任务,这种规划能力有别于一般的工业机器人,在每次执行任务的时候轨迹规划都有可能不同(运行时多态)。但是,由于仿真系统与控制器绑定在一起,不存在实时数据通信的难题。因此,数字孪生的现有研究中很少提及这个标志性的案例。然而,这种模式却是数字孪生技术发展的未来。一旦兼容的智能控制系统成为了主流,狭义的边缘孪生的地位将被取代,而广义的云孪生系统将会成为主要的存在形式。如图13所示,采用ROS系统控制的物理对象可以无需边缘孪生系统而直接连接到云端。
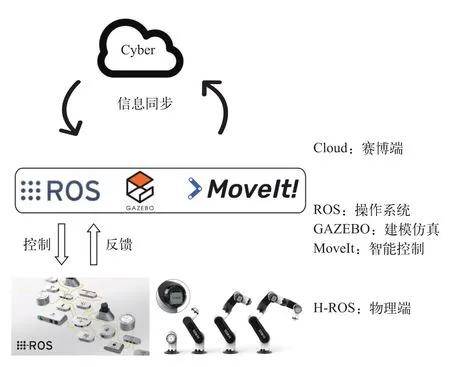 图13 智能ROS机器人的CPS架构(Cyber-Physics)
5 案例解析:数控加工的数字孪生
基于对数字孪生内涵的研究分析,以智能数控加工为研究对象,通过有机组合数字孪生系统的必要元素,构建了数控系统的边缘孪生系统GrapeSim及云孪生系统GrapeServer,论证数字孪生的实现方案和技术定位。该系统通过多个案例进行测试验证,并且在上海商飞试验生产线得到了应用与验证,如图14所示。
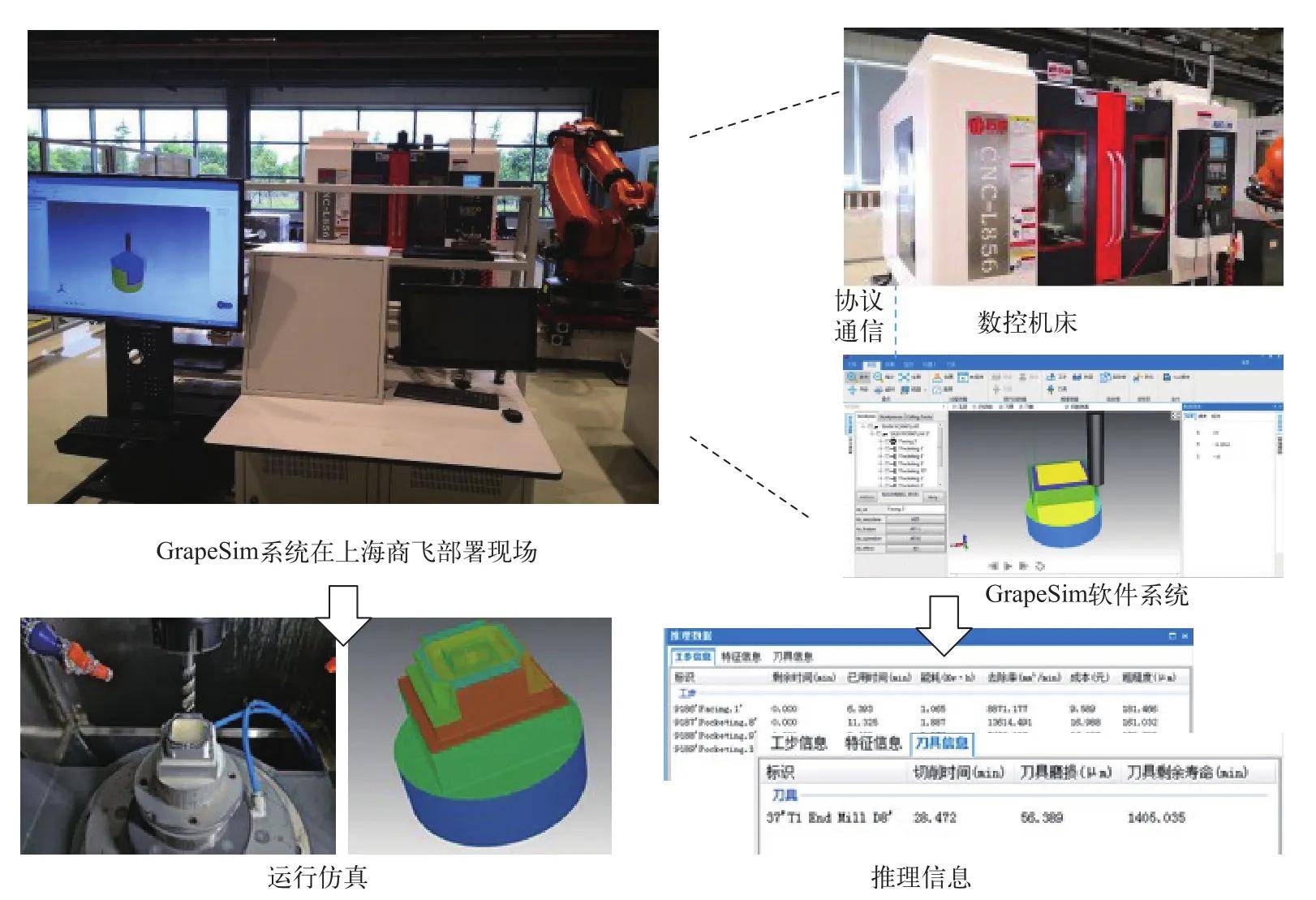 图14 GrapeSim软件在上海商飞车间测试验证
5.1 数控加工的数字样机
首先,根据“A digital twin is-a digital mock-up”的原则,GrapeSim需要实现数控加工的数字样机功能。当前,面向数控加工最完善的样机模型定义就是STEP-NC标准,例如:描述加工工艺的ISO
14649-11,描述加工刀具的ISO 14649-111,描述加工机床的ISO 14649-201。当前主流的CAD/CAM系统还不能直接输出STEP-NC文件,通过应用成熟的二次开发技术来解决这个问题,实现了针对UG和CATIA平台的STEP-NC后置插件系统,可以自动化地导出STEP-NC文件。如图15(a)所示,该文件包含全面的几何与工艺信息。以STEP-NC文件作为输入的GrapeSim软件系统,通过内部语义化的解析工具获取文件中包含的全部工艺数据,包括工件、刀具、刀轨、工步等。所有工艺信息可以在边缘孪生中集中呈现,如图15(b)所示,方便数控机床端快速浏览。同时GrapeSim系统中还集成了参数化几何建模内核,可以根据工艺信息自动构建工件、刀具、刀轨的三维模型,如图15(c)所示,用于加工过程可视化展示和初步校验加工程序。
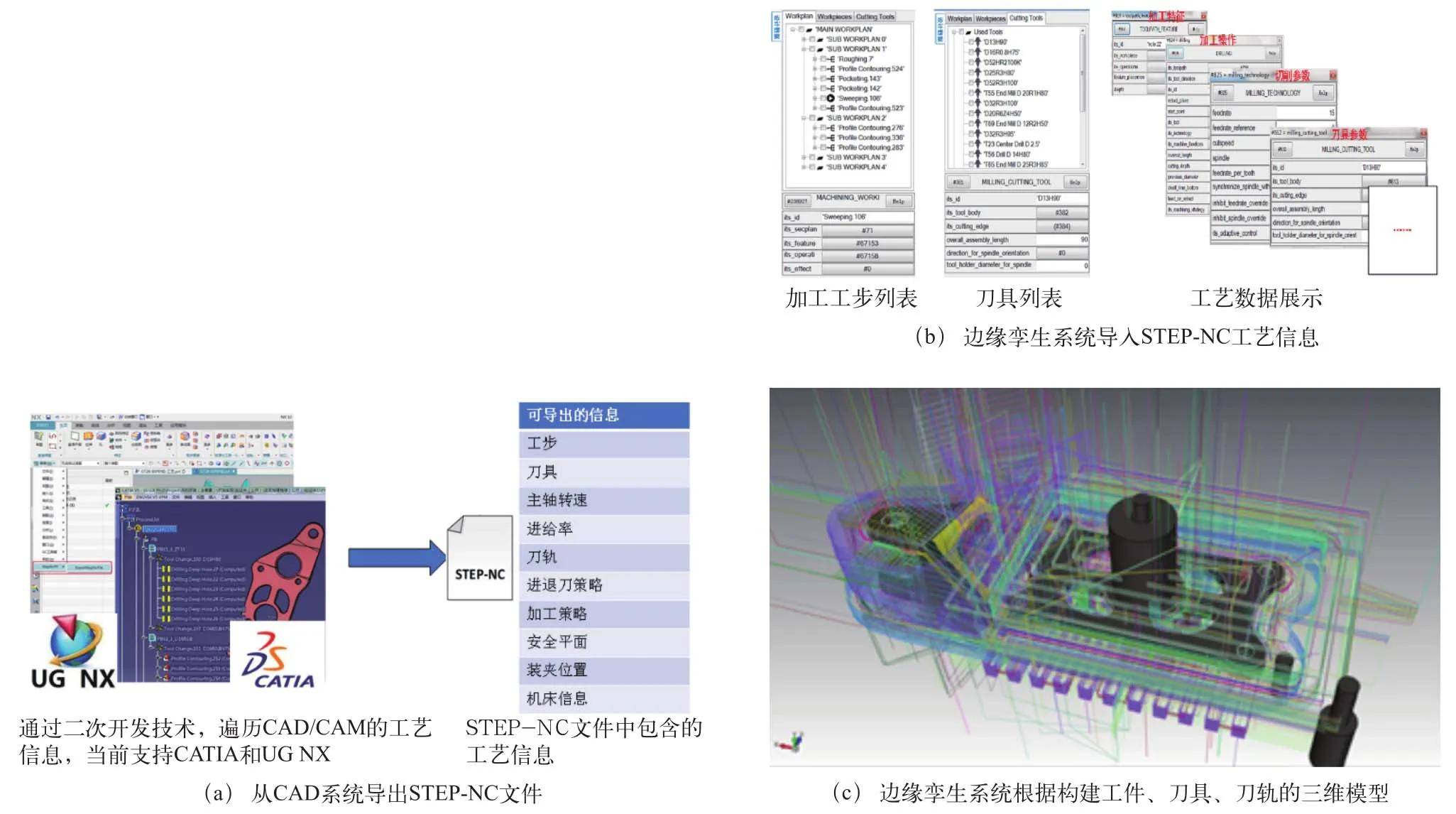 图15 CAD/CAM系统与边缘孪生系统的STEP-NC数据交互
有效的加工工艺模型还可以促进仿真更为精细化。例如,STEP-NC的特征信息可以大幅减少切削仿真预处理单元的分割数量。刀具和毛坯的布尔计算被限制在加工特征所定义的范围内,减少了计算量而提高了仿真效率。由STEP-NC定义的一个多加工特征组合而成的零件如图16所示。该零件的加工过程可以分解成三个特征,并针对不同的特征开发专用算法。
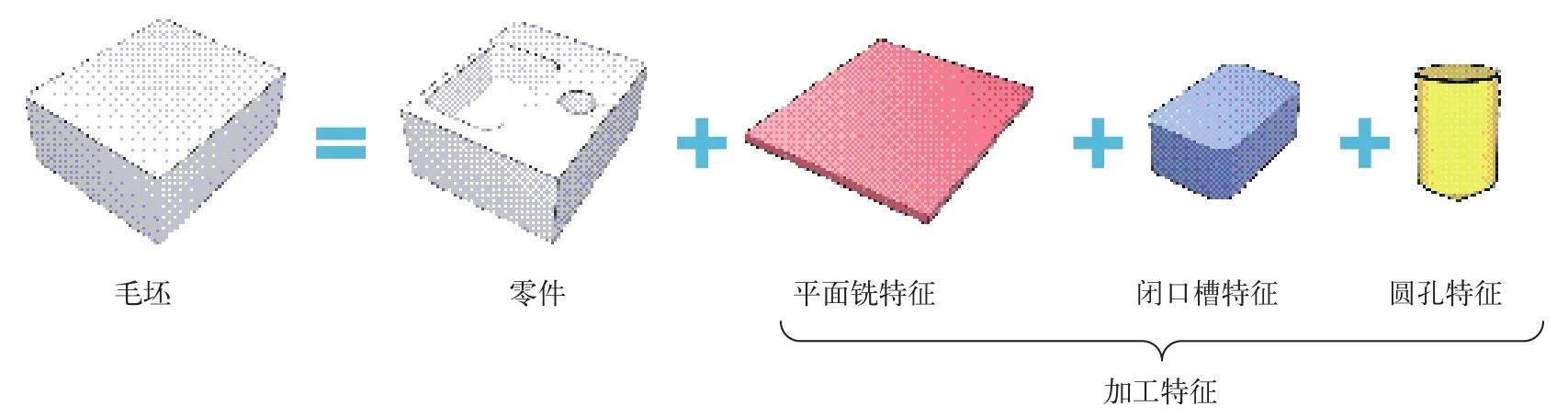 图16 加工特征、毛坯和零件的几何模型关系
在加工特征内部,可以根据加工工艺信息更精细地划分。例如粗加工和精加工的去除材料是不同的,而且材料被去除的过程存在差异。如图17所示,给出了一个槽特征的分割实例,针对粗铣和精铣可以采用不同的预分割模型。粗加工根据切深进行分层建立四叉树离散模型,精加工采用分层体素建立链表离散模型。这种过程中根据不同的加工特征与操作采取不同算法的仿真方式,兼顾了效率和精度,体现了多态式仿真的优势及数字样机模型(STEP-NC)对运行时仿真的重要性。
 图17 加工工艺对被去除材料的影响
5.2 信息同步的缓冲处理
为了组合信息同步能力,GrapeSim支持与不同数控系统的通信接口与协议,包括OPC-UA、OPC-DA、ADS等。需要指出的是,相比于现场总线工业以太网级的实时通信能力,这些基于TCP/IP协议的通信机制的实时能力受到了很大制约。在有限的带宽和采样周期的条件下,必然会存在缺失关键数据的现象。反映在仿真系统中,就造成了仿真结果与真实加工过程不一致的情况。如图18所示,加工仿真中获取的刀位点是通过机床通信技术实时获取的,而理论刀轨在p1点和p2点之间并不是一条直线。由于样周期的限制,刀轨的关键转折点可能会丢失,而加工仿真如果直接使用p1,p2作为输入,会造成虚拟工件的过切现象。
为了避免上述问题,需要开发工步搜索和刀位点插值算法,根据STEP-NC存储的理论刀轨补全原始的机床通信数据。其中工步搜索是指根据从数控系统获取的一系列相邻刀位点,搜索正在执行的加工工步。由于系统已经包含了STEP-NC表达的完整工艺信息,可以通过工步得到当前的理论刀具轨迹,因此这项功能是刀位点插值算法的基础。对于插值算法,根据刀位采样点正确对应到刀轨部分区段,并将两次相邻刀位点之间缺失的关键点进行插值,并调用仿真算法使得虚拟工件能正确地反应真实加工状态,图18中对比了是否应用插值算法的不同。
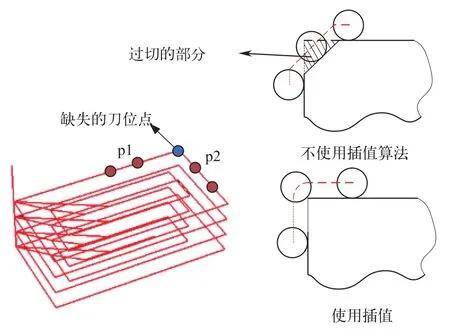 图18 缺失刀位点对仿真结果的影响以及插值的重要性
5.3 动态绑定的运行时仿真
运行时仿真能力是GrapeSim系统追求的核心价值之一。为此,系统针对实时切削仿真算法进行了深入的研发,在实现传统的切削仿真算法的同时,结合运行时仿真的问题与数字样机模型的支撑,进一步研究了特定条件的高效实时切削仿真算法。加工仿真算法可以分为几何仿真和物理仿真两大类。由于核心需求的变化,这两类仿真算法的原理存在巨大差异。动态绑定的仿真系统就体现在将这两类仿真计算结合在一个系统,并实现与真实加工过程的同步。
几何仿真算法关注的是毛坯几何形状在加工过程中的变化过程,并通过三维渲染技术提供可交互的零件模型浏览,如图19
(a)所示。对于常见的基于离散模型的加工仿真方法,布尔计算所占用的资源远小于毛坯三维模型的动态建立。受限于巨大计算量,毛坯的离散精度不能设置太精细,以保证仿真过程的实时性。而物理仿真关注的是刀具切削过程的受力情况,是一种物理度量,其原理如图19
(b)所示。物理仿真的计算核心是刀具和毛坯之间的接触区域,包括切入角、切出角等。毛坯模型的离散精度是决定物理仿真结果可靠性的关键因素,因此需要尽可能地提高毛坯离散精度。不同于几何仿真,没有三维模型重建负担的物理仿真可以使用高精度的毛坯离散模型。
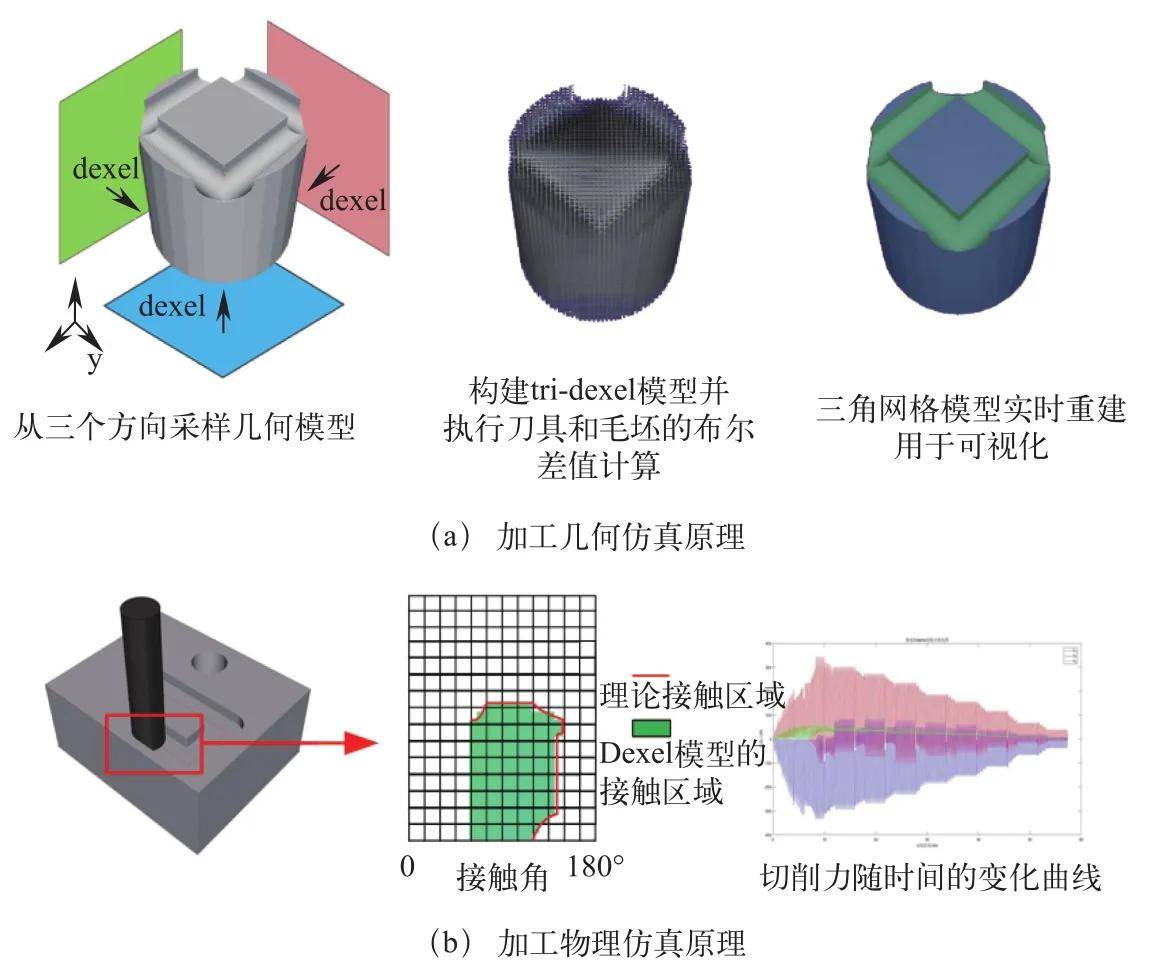 图19 实时加工过程几何物理联合仿真原理
加工过程的几何仿真与物理仿真的结合,验证了GrapeSim的虚拟系统的多态仿真特性,使得虚拟仿真可以从多个方面反应真实加工过程。现有的功能包括:被加工零件几何形状的同步跟踪显示,切削力计算,刀具磨损评估等多项数控加工过程评估。而同样使用数控系统的采样数据作为输入,几何仿真和物理仿真由于计算原理和结果输出的不同,表现出了多态的特性。多态的仿真一方面可以帮助数字孪生系统记录下每个零件的几何物理加工过程,便于未来追溯;另一方面又可以为动态自适应优化控制提供重要的分析依据,使得相同的加工工件产生多态的加工行为。
5.4 数字孪生在云端的镜像
如前所述,数字孪生与CPS的结合可以倍增其效能,前提是必须认清CPS与数字孪生之间的组合与被组合的关系。为了说明这一点,在此介绍GrapeSim与GrapeServer的基本架构与运行原理。对于GrapeServer而言,GrapeSim是一个边缘数字孪生系统,如图20所示。GrapeServer是运行在云端的CPS系统,管理了不同机床的4D云端镜像,每一个4D云端镜像都会通过账号系统与指定的边缘端GrapeSim建立长连接。所谓4D,指的是云端的机床镜像维护了机床信息的时间轴,而边缘端GrapeSim所呈现的可以被认为是这个4D镜像的当前时间切片。云端机床镜像具有很强的数据封装性,其目的旨在全面代理机床物理端。对镜像端的信息查询可以等同于对边缘端的查询;派发到镜像端的加工任务,会自动同步到GrapeSim;GrapeSim产生的实时数据与语义信息会自动同步到镜像端。比较直观的应用包括GrapeSim可以根据STEP-NC的刀轨定义与实时的数控位置信息推理出当前的加工零件与工步骤,而用户在任何时候都可以通过云端观察到当前工件的实时加工状态;同步到边缘孪生系统的STEP-NC文件可以根据当前机床的硬件状态(数控系统、刀库等)自动后置出匹配当前硬件的G代码,并DNC到数控系统中,由此实现屏蔽机床硬件以及“一次设计,到处执行”的多态加工模式;APP可以通过与4D机床镜像的连接,对机床加工状态进行实时监控。
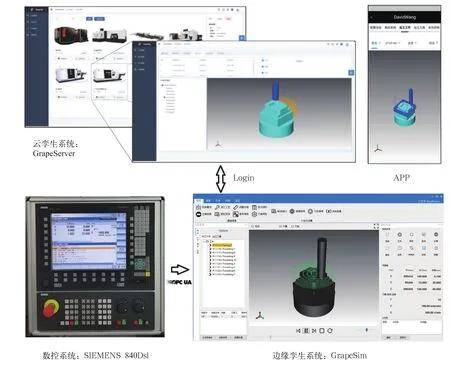 图20 边云协同的数控加工数字孪生系统
以上述的基本架构为基础,未来的机床数字孪生镜像可以向CPS系统提供数据服务,而CPS系统可以为数字孪生镜像提供智能服务。例如,CPS可以根据机床的能力、成本与任务繁忙程度,实现自动加工任务(STEP-NC文件)派发,GrapeSim再根据个性化的配置实现多态式的后置处理。CPS系统可以针对不同机床镜像的面向特征的加工过程数据进行工艺分析,并将总结优化后的工艺信息广播配置到其他类似的机床镜像中。机床镜像可以根据GrapeSim推理的刀具磨损状态信息向CPS系统发出换刀请求,而CPS则根据统计的镜像需求完成最优的换刀规划。
6 结论与展望
本文从面向对象编程的理念出发,分析了数字孪生的态绑定仿真的特性,探讨了面向孪生制造的未来智能制造运行模式。采用面向对象的建模思想,推理出动态绑定仿真的最终意义在于实现多态式仿真与分析。通过面向对象编程与面向孪生制造的对偶关系,推导出界定数字孪生的原则与规范。将数字孪生与数字样机、硬件在环仿真、多物理场仿真等技术进行对比,分析了数字孪生与各概念之间的区别与联系。提出“先模型、再仿真、后连接”的数字孪生实施原则。针对数字孪生的当前问题与瓶颈进行了讨论,以帮助梳理数字孪生系统实施的关键。最后,结合一个面向数控加工的数字孪生及CPS系统的开发案例,阐述本文所述的数字孪生内涵在具体实施案例的应用与体现。该系统已在上海商飞制造厂试验车间得到了应用与验证,部分验证了本文提出的数字孪生实施原则的实用性。需要指出的是,目前本文介绍的数字孪生系统还处于发展的初级阶段,未来还有大量的问题需要解决。不过,本文提出的组合数字孪生镜像的CPS系统将有助于实现把智能终端连成网络的阶段性目标,从而推动智能制造与工业互联网相关技术的发展。
|