编辑推荐: |
本文介绍了FMEA:失效模式及后果分析,希望对大家有帮助。
本文来自于知乎,由火龙果Anna编辑推荐。 |
|
我觉得有必要先写在前面:
很多人都在纠结,Failure Mode and Effects Analysis,明明是FMEA,为什么还是有人,甚至是专业的从业者念做FEMA呢???
其实大可不必纠结,英文本身就是个极为随性的语言。道理和ISO一样,ISO全文:International
Organization for Standardization,按道理简写应该为IOS,不过还是调换了一下字母顺序来获得比较方便的发音,这样一来避免了英语的发音困扰(双元音字母),二来又有了希腊语“ISOS”,意为“平等”的含义以及英文“Isonomy”(法律之下人人平等)的含义,强调在ISO组织内会员国或区域代表,不论其大小,仅能有一位代表,每位代表的权利与义务是相等的。
所以FMEA,通常会被读为FEMA(菲玛),一样是因为英文发音的问题才做出的改变。我在知乎上看到有人因为有人用FEMA就大呼对方外行,其实大可不必。本文中还是会用FMEA,毕竟书面语言简写还是要遵循规则的,不过以后遇到有人念做FEMA,各位也不用奇怪。
一、内容
产品设计成熟时,可靠度分析工作由正面的应力分析、容差分析等,转向以物品失效为出发点的分析工作。这便是FMEA:Failure
Mode and Effects Analysis, 失效模式及后果分析。该分析方法具有两个特点:
是一种风险评估工具
是一种预防性的可靠度技术,用来描述系统化的活动
二、目的
FMEA分析的目的是:
发现与评估产品制程中潜在的失效及影响
发展能够预防或减少这些潜在失效发生的具体措施
将上列整个过程加以文件化
降低异常发生频率与品质成本
利用表格为主要工具进行分析
在设计阶段早期发现问题及早谋求解决措施
三、历史
整个FMEA分析的历史实验,要从二战结束冷战开始说起。二十世纪40年代后期,美国空军正式采用了FMEA。后来,航天技术/火箭制造领域将FMEA用于在小样本情况下避免代价高昂的火箭技术发生差错,其中的一个例子就是阿波罗太空计划。二十世纪五十年代,NASA与美国空军的X系列试验机项目如火中天[1],FMEA被用于分析飞行控制系统。二十世纪60年代,在开发出将宇航员送上月球并安全返回地球的手段的同时,FMEA亦得到了推动和发展。二十世纪70年代后期,福特汽车公司在平托事件之后,出于安全和法规方面的考虑,在汽车行业采用了FMEA。同时,他们还利用FMEA来改进生产和设计工作。于是在70~90年代,无论是军事还是各专业的行业协会,都相继提出标准和程序的书面定义和改进FMEA的方法。
1985年欧洲的国际电子工业协会IEC推出IEC812(现在的 IEC
60812),提到FMEA及FMECA(failure mode, effects and criticality
analysis; FMECA失误模式效应与关键性分析法)在各领域的应用。英国标准协会在1991年为了类似的目的发行了BS
5760–5。整个八十年代在汽车行业中各大汽车厂商都相继采用FMEA进行技术失效分析。1994年美国汽车工程师学会提出SAEJ-1739标准,同年戴姆勒克莱斯勒、福特、通用汽车三大汽车巨头为了使相关供应商都能建立符合要求的质量体系,结合通用公司的“北美创优目标”、福特公司的“Q-101质量体系标准”、克莱斯勒的“供方质量保证手册”,于1994年8月发行质量体系要求(Quality
System Requirements)即QS9000标准。换句话说,要给美国三大汽车公司配套产品成为他们的供应商,就必须要达到QS9000要求。1999年戴姆勒克莱斯勒、福特、通用汽车都开始采用FMEA、以及ISO/TS16949标准内容。2006年,ISO/TS16949正式替代QS9000,成为国际的汽车行业通用标准。
尽管最初是由军事领域所建立的方法,但FMEA方法学现在已广泛应用于各种各样的行业,包括半导体加工、饮食服务、塑料制造、软件以及医疗保健行业。在设计和加工处理格式方面,FMEA已经结合到了产品质量先期策划(APQP),以便提供基本的风险化减手段以及实现对于预防策略的时机选择。汽车行业行动工作组(AIAG)要求在汽车的APQP过程中运用FMEA方法,并且还发布了详细的一份关于如何应用这一方法的手册。对于每种潜在的原因,都必须针对其对于产品或加工处理过程的影响而加以考虑,并根据相应的风险,确定所要采取的行动措施,并在行动措施完成之后对风险重新加以评估。Toyota已经进一步将这种方法与自己的基于失效模式的设计审核(DRBFM)方法结合在一起。现在,这一方法还同时得到了美国质量协会的支持。美国品质协会针对应用这种方法而提供有若干的详细指南[2]。
四、实施
FMEA的实施有五大要点:
强迫思考:具有适时性,事发前行为,非后见之明的行动(就是别放马后炮)
动态文件:结合系统性的矫正与预防措施
建构完整的标准化:以标准的设计与验证基准下进行预防与侦测
持续改善:以往的教训与知识累积
根据零组件失效资料由上而下推断系统失效模式及其效应,即演绎法
发现问题→解决问题→遇见问题
FMEA实施方式有五类方式:
将失效事件按严重等级区分
可归纳出所有的失效模式
以表格为分析的主要工具
只对硬件进行分析
失效模式及效应常应独立考虑
在FMEA实施中以设计产品制程尤为着重应用:
①新设计、新技术或新制程——需要使用FMEA分析
②修改现有的设计或制程——需要使用FMEA分析
③在新环境、地点或应用上,利用现有设计或制程——需要使用FMEA分析
④当既有的系统、设计、产品、制程或服务被考虑要改善时——需要使用FMEA分析
现行FMEA分析技术参考资料通常以以下三个:
美军标MIL-STD-1629A
国际标准IEC-812
美国三大汽车(通用、福特、克莱斯勒)发行的FMEA参考手册
五、FMEA开展场合与时机
越早越好
消除或减少已知或潜在问题,强化顾客满意至最大极限,且面对的情形,很有可能相关的数据、资讯尚不明确。
FMEA口号:就你所有,尽全力所为
六、FMEA作业
FMEA分析的逻辑有点因果律的意味:
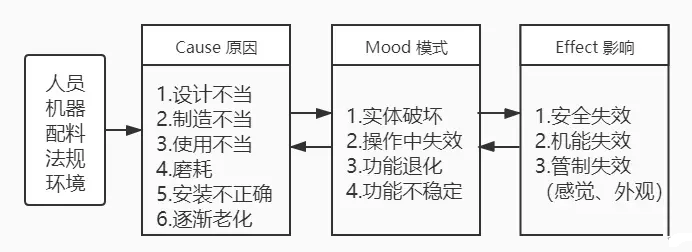
在FMEA作业内容包括:团队组成、资料收集、订定执行方案、计算风险、展开建议行动五个步骤:
1.团队组成(人选)
①跨部门团队组成→(设计工程师、制程工程师、生产管理人员、品保工程师......)
②跨层机人员
③遴选FMEA负责工程师
④灌以执行改善动作
2.资料收集
①有关产品设计方面的资料
②有关制造工艺方面的资料
③有关使用维修方面的资料
④有关环境方面的资料
3.订定执行方案
①表格形式
②分析设计或制程的层次
a.分析最底层次(即系统达到的最低线功能)以能够对其功能做完整描述为准
b.从高层次(即系统能够达到的完整功能)的分析结果判断
c.根据以往经验决定分析的最低层次
d.以刚好高于维修保养的最低层次为主(即最低线功能必须能够通过维修保养进行功能性恢复)
4.计算风险:
①严重度(每次失效模式取最大值)
②针对每一失效模式,采用最高计分的严重度乘以最高计分的发生率(SXO)。
③风险优先指数(RPN)为最高计分的严重度乘以最高计分的发生率,再乘以最低计分的侦测度
风险优先指数(RPN)=最高计分的严重度*最高计分的发生率*最低计分的侦测度
④风险优先指数(RPN)也可以用较高计分的侦测度(完全视目前管制方法的性质而定,依照AIAG、FMEA手册范例进行相应改变)。
5.展开建议行动:专注于重要的失效模式,列出潜在的失效模式:
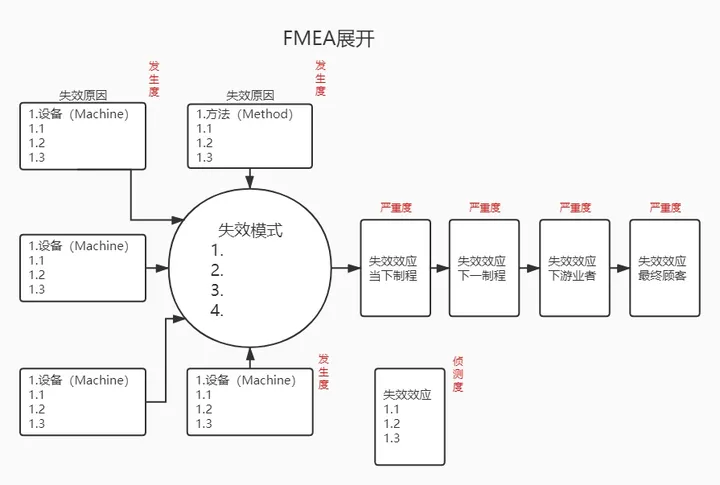
①从流程(或系统)中的必须输入项目予以考虑(人员、机械、材料、方法)
②经验与知识
利用过去类似产品(或流程)的失效记录资料(亦称使用者抱怨资料)
从可能的失效模式通过工程经验,预测出适用的失效模式。
③脑力激荡:最低效最无用的失效模式探索方法。
潜在失效模式通常依据经验可以分为四类:
①材料性失效:破碎、变形、黏沾、生锈、断裂......
②机械性失效:松脱、外漏、未传送扭力、打滑(未保持扭力)切入不顺、解脱过快、偏差......
③结构性失效:不能支撑、未完全支撑......
④信号失效:信号不足、信号间歇、没有信号、电磁相容性/射频干扰
*潜在失效模式应以“物理性的”或“技术性的”用语用词进行描述,而非以顾客观察到的现象用形象化的语言描述。
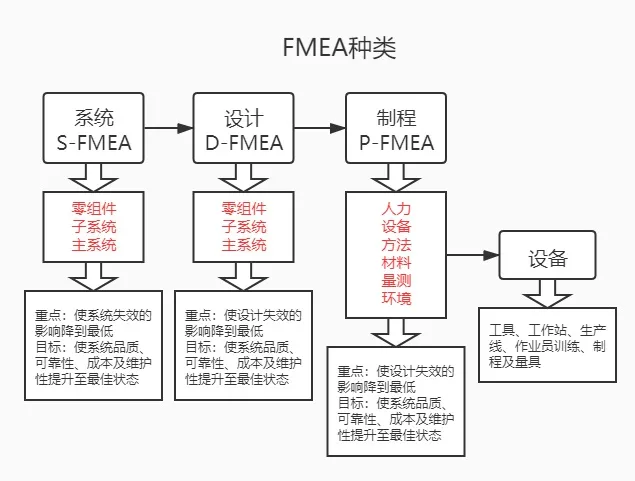
FMEA的管制计划中,最终获得的建议措施一定要是治本的,若出现治标不治本的建议措施指导意见,则说明前面的流程中,对某一项失效指标的分析理念与实际需要面对的问题产生偏差。
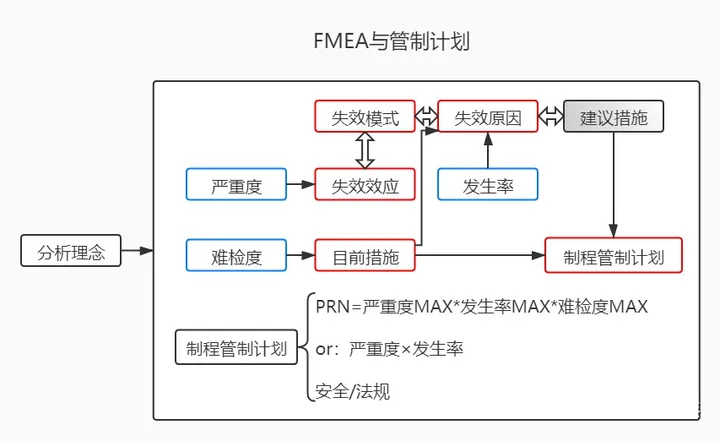
一般的FMEA分析中需要考虑的条件有:
Items/process/function:零件编号与功能
Potential Failure Mode:可能的失效模式
Potential Effects of failure:零件功能失效的结果(及其下一个制程的结果)
Potential causes of Failure:不适当的设计、不适当的材料
Detection Mrthods and Quality Control:现有衡量失误的方法,包括预防与检查措施
RPN
Recommended Actions:从RPN中能够选出显著的项目,列出每一失效模式的矫正行动
前面提到整个FMEA作业流程基于表格的文件化程序进行,这里以汽车行业的FMEA分析为例:
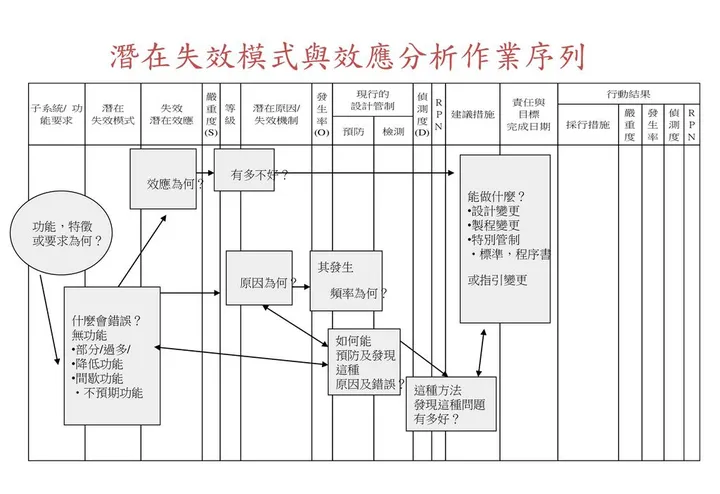
再次强调其中三个重要的量化分析参数:检测度、严重度、发生率。
可以参考前面文章法海:ISO国际标准认证——6.规划末尾对RPN风险指数评估方法的内容。
七、失效模式
每种产品都具有相应产品特质的失效模式,这里例举打印机与手电筒进行说明:
EXAMPLE1:打印机,使用理想状态:印出清晰的文字
可能的失效模式:
墨水匣:停止进墨......
打印喷头:产生噪音......
打印机轴承:卡纸......
纸匣:无法进纸
EXAMPLE2:手电筒,理想使用状态:提供300流明的照明
可能的失效模式:
没有灯光
暗淡的灯光
飘忽不定、闪烁的灯光
渐渐模糊的灯光
灯光太亮
从以上两个范例中,我们不难发现,失效的潜在效应,无非就是:
噪音、变粗糙、操作不规范、无法操作、外观不良、异味、不稳定、操作不良、间歇性发作、热现象、渗漏、校准不符......
而这里需要注意,失效模式、失效效应、失效原因三个概念所代表的名词是有所差异的:
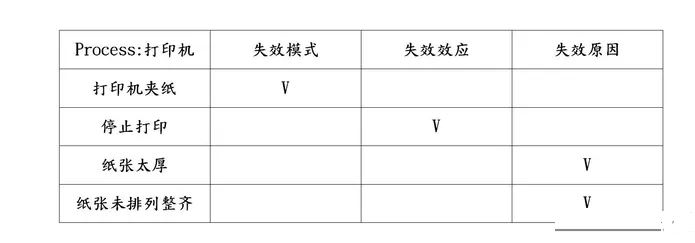
结合工程经验与理论知识,分析每个失效模式发生的可能原因。而找出这些原因,要么利用特性要因图,通过有理论、有逻辑的分析来寻找失效原因。但是,有时候发生失效的原因他就是很魔幻,当山穷水尽之时,也是要考虑前面称之为最低效浪费时间的方法:脑力激荡,意思就是瞎蒙,万一就蒙中了呢......
八、潜在失效原因/机制——发生度/发生率
失效原因通常属于材料外界因素导致:
①使用材料不正确②设计寿命假设不足③压力过大④润滑能力不足⑤保养说明不适宜......
失效机制通常属于材料内部因素导致:
①弯曲②金属疲劳③材料不稳定④变形⑤化学氧化⑥磨损⑦电子漂移⑧锈蚀......
发生率即是指:特定原因/特定机制在设计生命中可能发生的几率。即上面例举的各种失效原因/机制发生的几率。
发生率进行量化分析落实为参数数值,需要注意发生率的等级/分数,具有相对意义而非绝对意义。藉由设计变更或设计过程变更,才是降低发生率的唯一办法(设计查检表、涉及检查、设计指引)。在设计发生率评级时需要注意:
是否曾经使用工程分析,来评估在应用时所预期的类似发生几率?
是否有预防管制措施?
发生率评价等级分数为FMEA作业范围内的相对评分,并不一定是反应实际可能的发生率。
九、现行的设计管制——难检度/侦测度
侦测度更多的是尽可能希望把较罕见、低概率的失效模式压榨、逼迫出来,需要例举预防、设计验收/查证(Design
Verify,DV)等已完成或已提出的确保失效模式/原因/机制在设计考量下的设计适用性。现行管制都是针对相同的或类似的设计所使用的管制方法,管制措施有:设计审查、失效/安全设计(压力阀、数学计算)、线上/实验室测试、可行性评估、原型机测试、路上测试(实地测试)、车队测试(比对试验)......
整个实验小组应随时着眼于改进管制,例如实验室中创造出的系统测试,创造出系统模型式计算程序等等。
设计(DFMEA)管制类型即为两种:
预防:预防失效原因/机制或失效模式发生的几率
检测:检测失效原因/机制或失效模式,可藉由分析的方法或物理方法在大批量生产前检出。
防患于未然,虽然理想状况下预防的方式比较好,但是最终很大一部分的失效模式都是被检测这一方法检测出。而对预防中的失效模式预测越精准,所带来的失误成本就越低。
最终,所有的失效原因/机制,作为量化分析结果表示在FMEA分析中,即RPN风险指数(Risk
Priority Number)
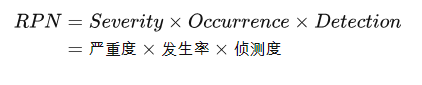
根据RPN可以获得两个目的:
确定是否对相应失效项采取措施
确定优先解决的项目
RPN原则:假设以1~10来表示严重度、发生率、侦测度三个参数由轻到重的程度,则RPN范围为1~1000
RPN越大,易解决者越优先解决;可设定标准来标定哪些失效需要解决的顺序。例如:RPN≥150失效原因应必须解决、50≤RPN<150应尽可能解决,无法解决必须加以严控、RPN<50可不加控制。
RPN<150:严重度(S)发生率(O)这两项较大的失效原因应优先加以改善,S=9~10、O=9~10的失效必须加以改善。
RPN标准设定的临界值,根据实际情况分析后应由FMEA小组成员具体讨论获得。
范例:
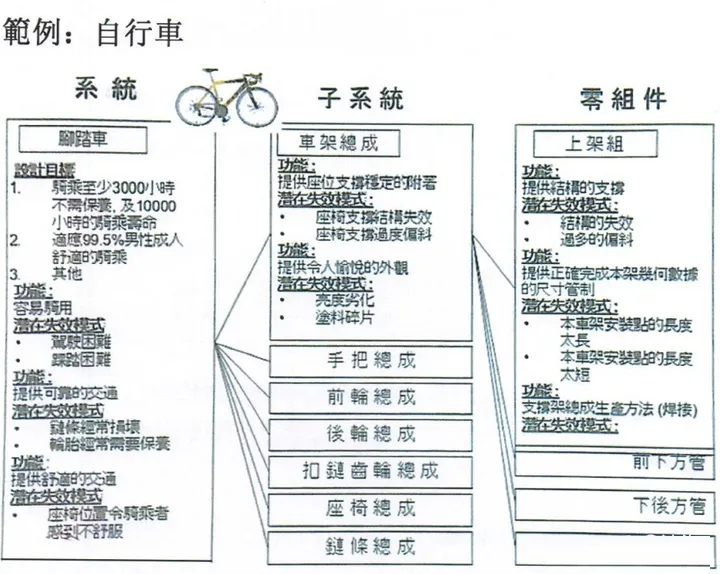
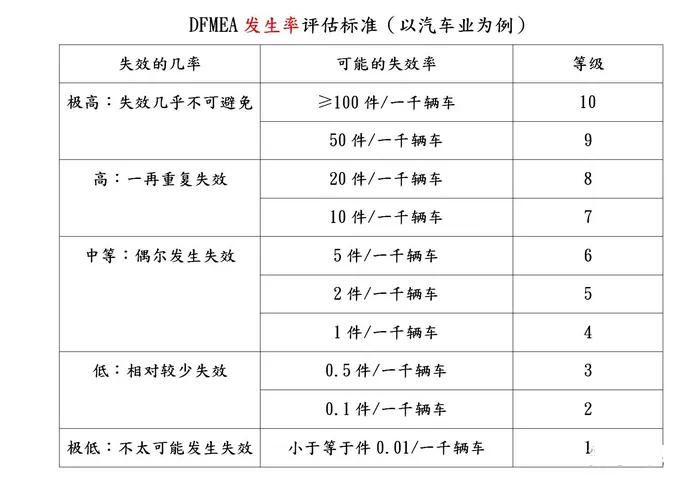
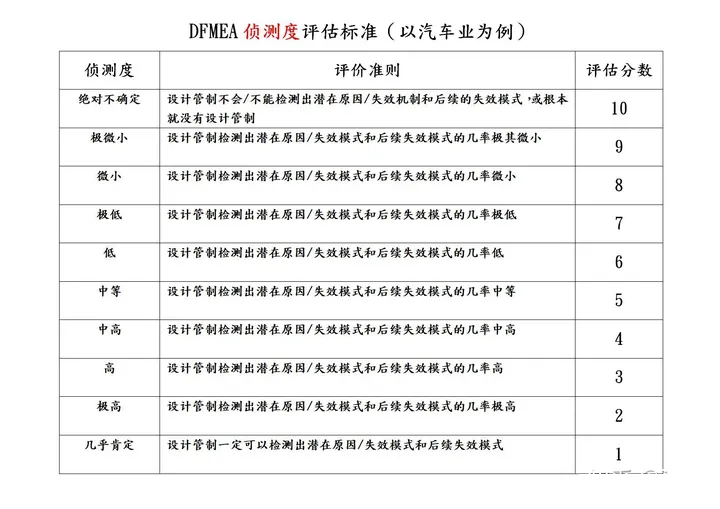
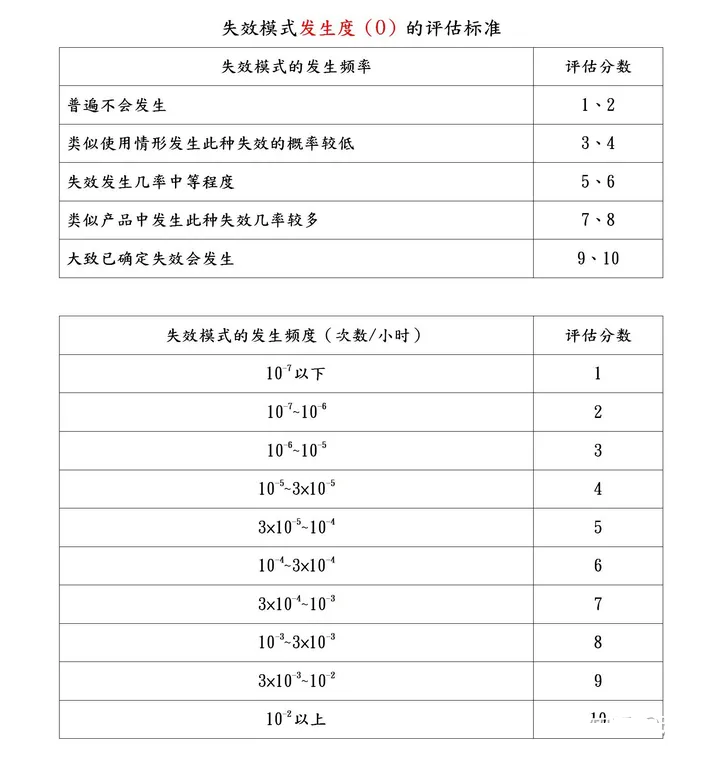
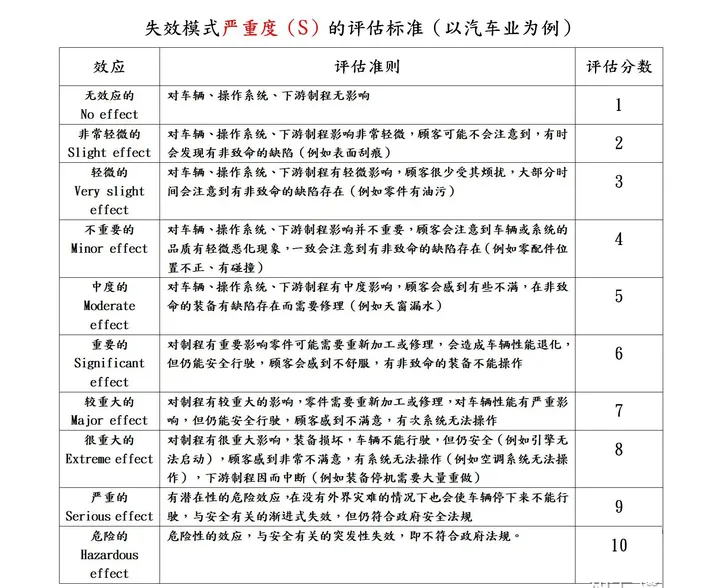
FMEA分析里面有相应的评估表格样本,不过平时我们也可以依照FMEA分析的原理,简单列出一个表格作为我们评估一件事情的参考,比如买房:
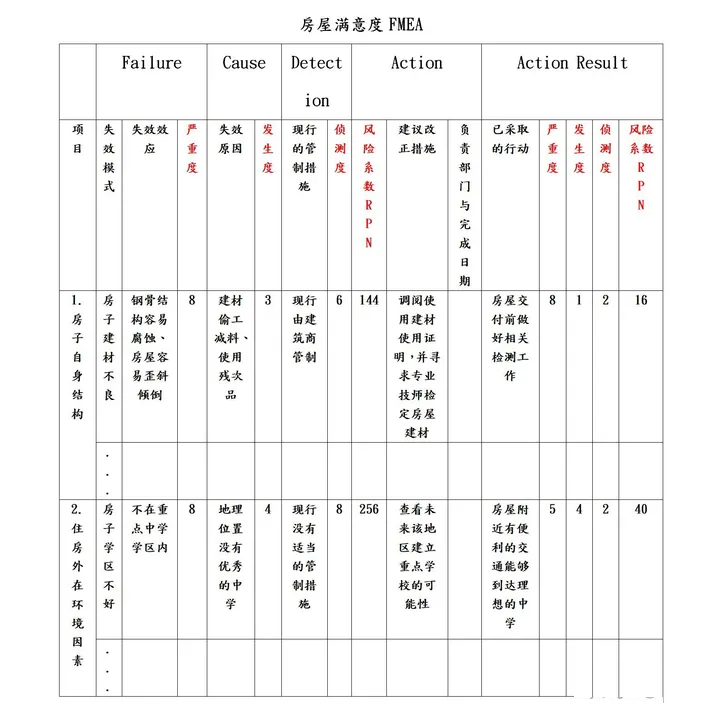
或者医院也可以拿来判断某病人是否合适于某种治疗
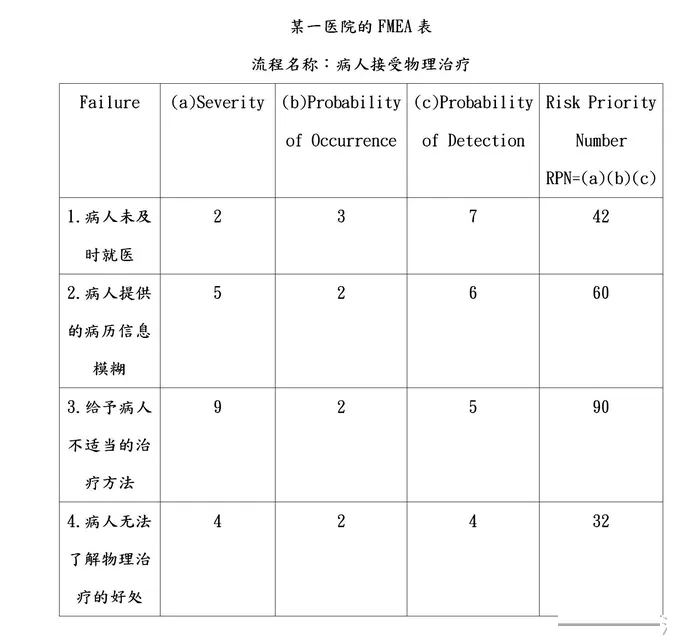
(建议非医学专业人士不要拿着这个方法瞎分析,该方法论都是基于各学科的专业基础之上的)
以上为FMEA:失效模式及后果分析的初步介绍与范例列举,该方法论为我们量化评估某一事件提供了一个有序的方法,在工程系统中具有重要用途。 |