编辑推荐: |
本文主要介绍了APQP
(产品质量先期策划)相关内容。希望对大家有帮助。
本文来自于微信公众号 Quality质量与检验,由火龙果Anna编辑推荐。 |
|
项目开发过程目前存在的痛点
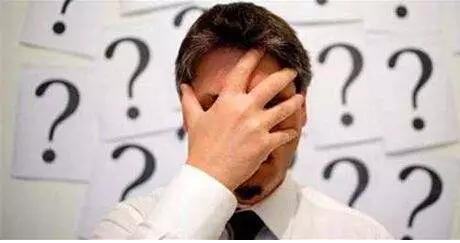
l 项目开发人员更迭多,项目人员能力不足;
l 管理层参与度低,项目开发过程监控需提升,内部hot issue上升和支持不足;
l 开发各阶段认可流程缺少、执行或细化不足,风险识
别、预警不足;
l 新项目APQP开发具体交付标准理解不清;
l 项目无自驱管理机制;
l 前期开发与制造工厂协同不够;
l GP12执行效果薄弱;
l PPAP临门一脚,质量堪忧;
l ……
APQP简介
01什么是APQP
APQP是项目管理的工具

全称为Advanced Product Quality Planning,即产品质量先期策划。
按照有序的步骤,把客户的要求(SOR/图纸/数模/标准)转换为质量稳定的供货。
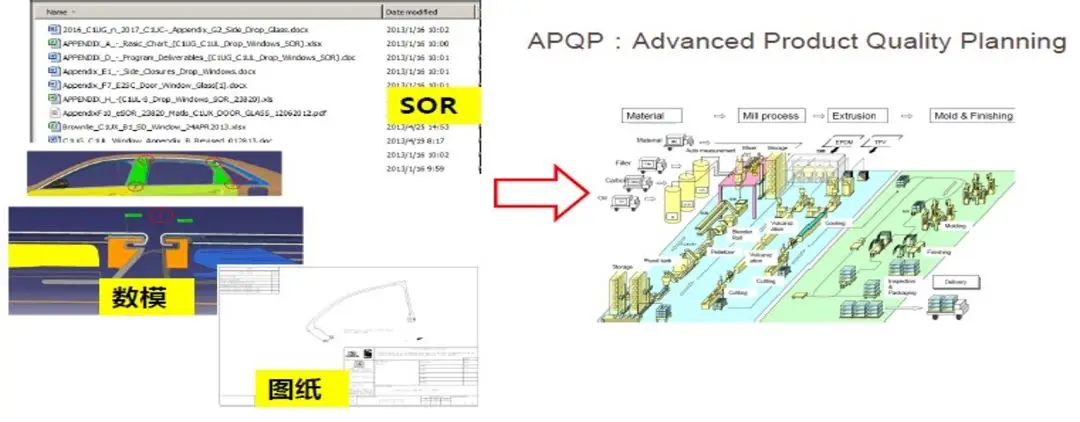
3W1H: When/What/Who/How
三大要素:交付/质量/成本
APQP应用的意义
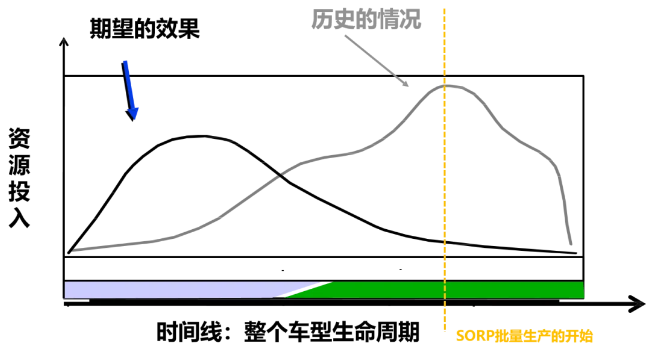
02
APQP任务
17项任务
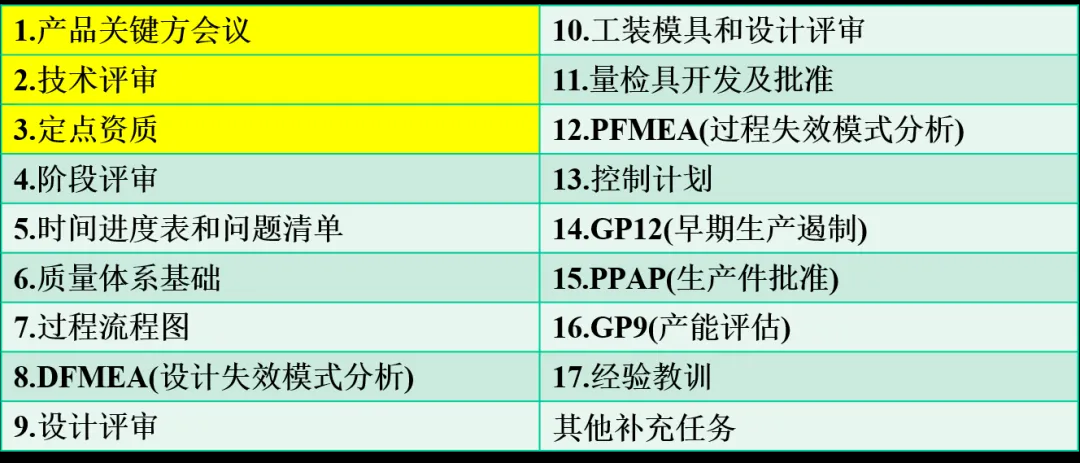
任务1~3由SGM 主导;
任务4的第一阶段由SGM主导;
其他任务都由供应商主导。
任务分类
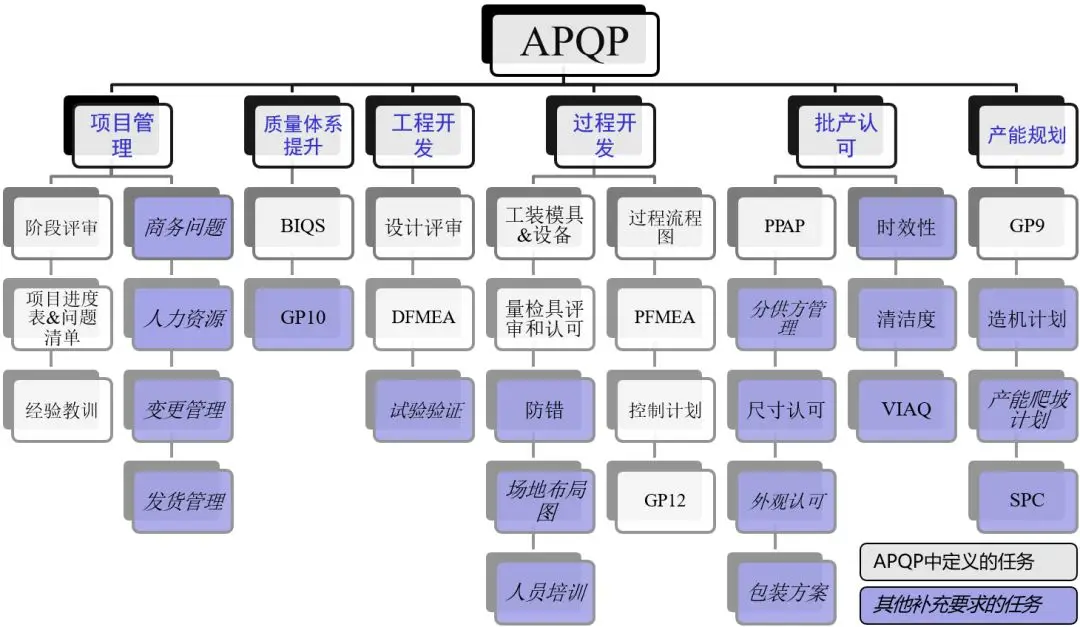
03
进度跟踪
APQP进度表横坐标为时间线,纵坐标为任务线;时间线,把APQP分为六个Gate;
任务线,把APQP细化为多个子工作项;
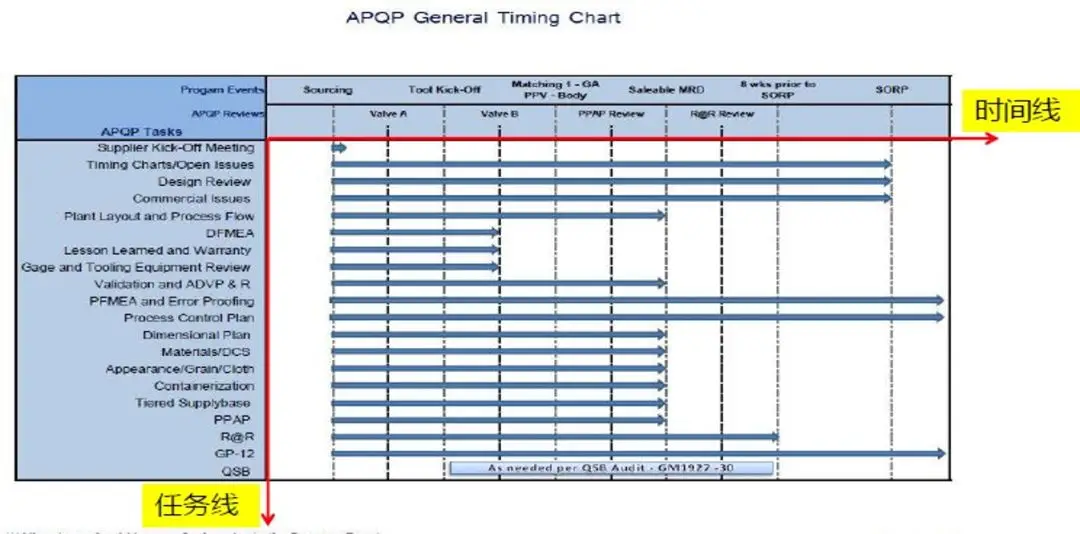
APQP 六个Gate 的建议时间设定
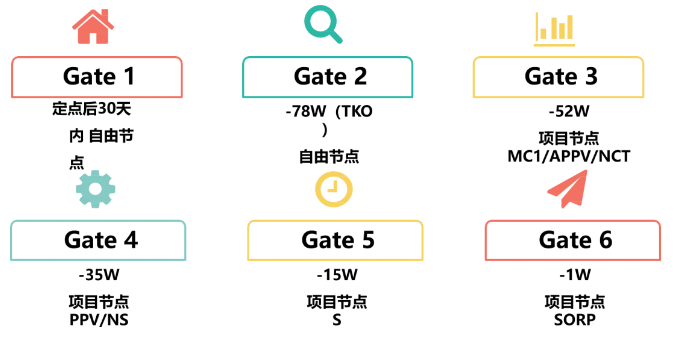
04工作重点
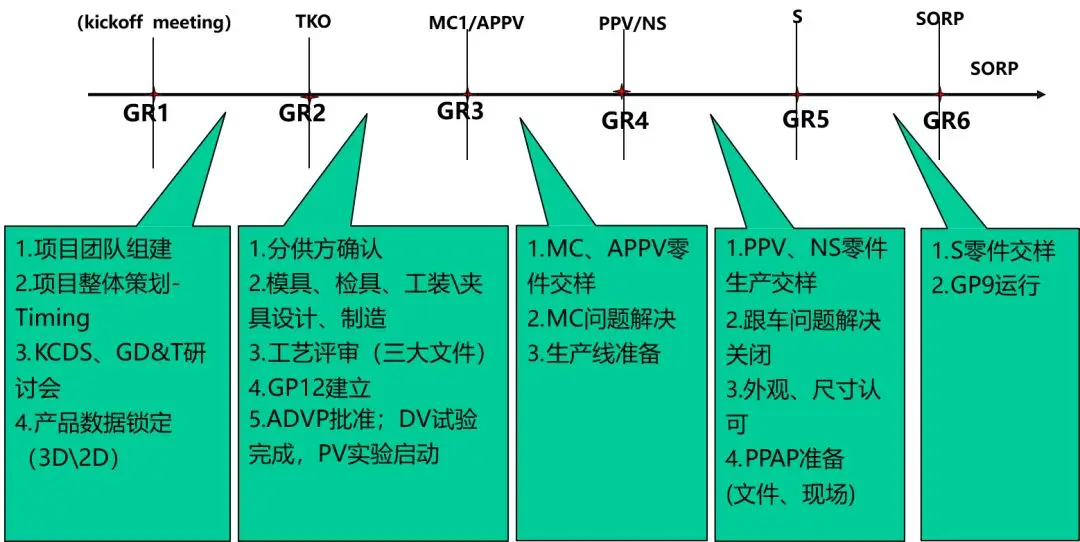
05
Gate Review监督机制
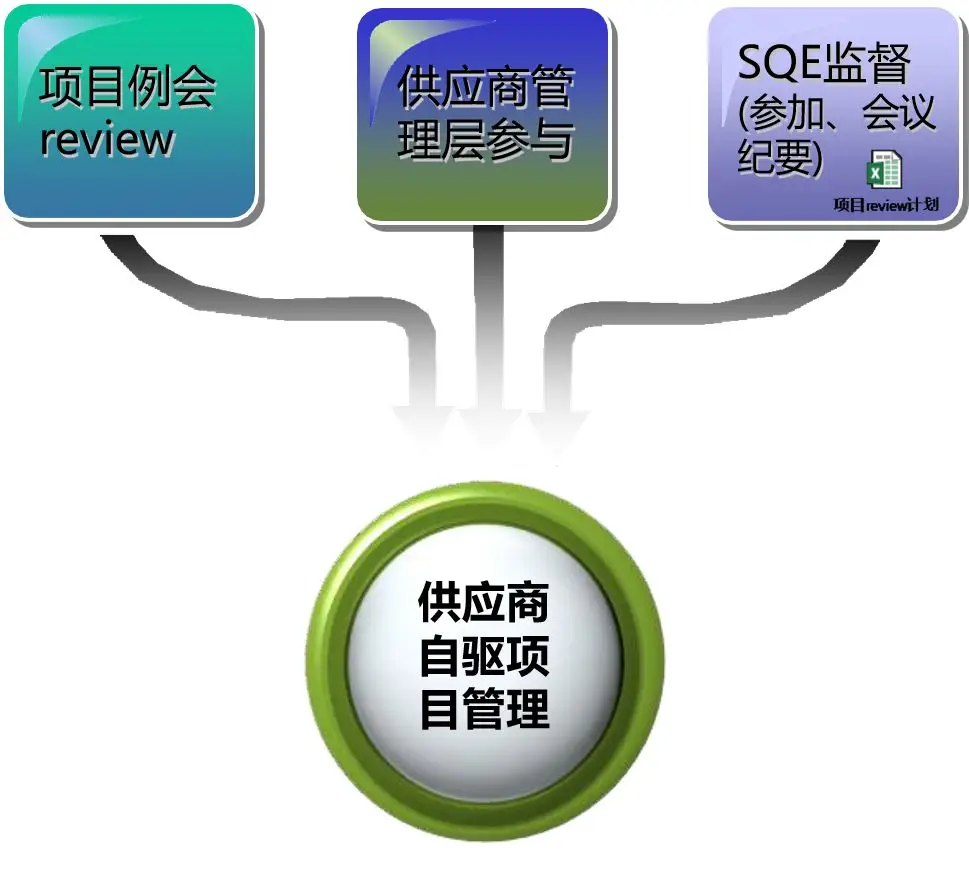
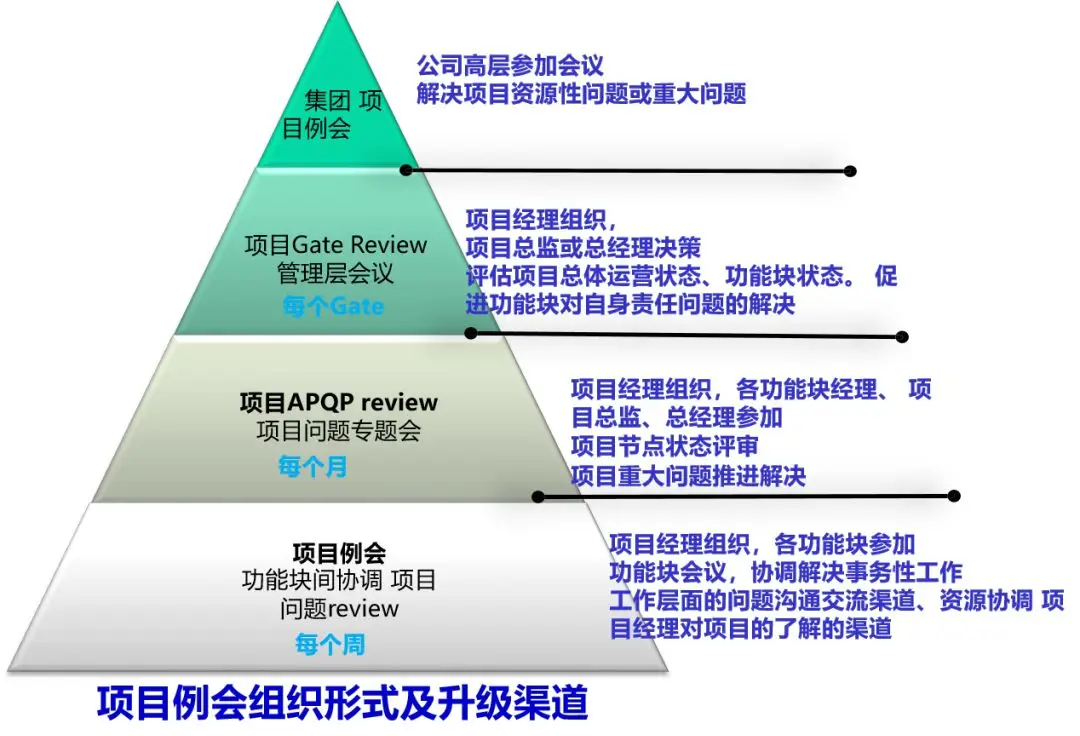
EP系统关注点
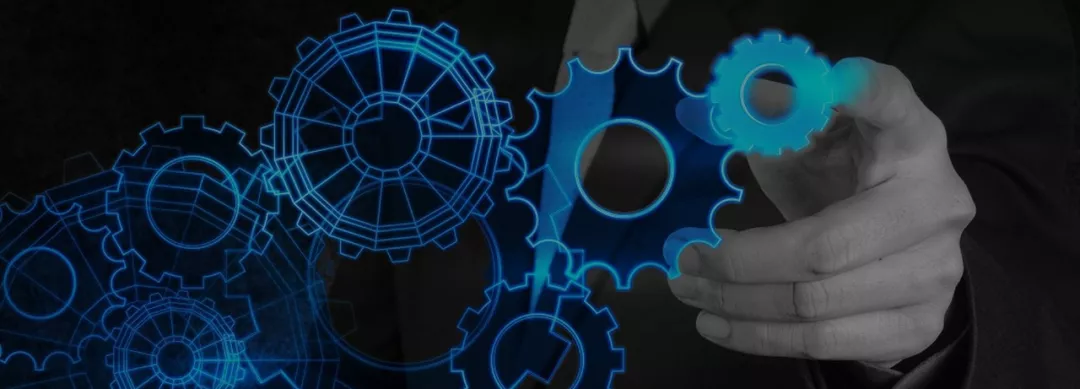
01项目基本信息
关注:任务号、APQP描述:某车型某项目、所属项目、制造供应商、项目经理、SQE。
02
零件号添加
可通过字体颜色判断零件号是否在系统中。
03
特殊工艺生产线认证
关注:特殊工艺、特殊工艺供应商、特殊工艺生产线、认证状态。
04
实验室认证
关注:实验室类型、实验室名称、证书状态。
05
工作项清单
关注:APQP Element、工作项、是否适用更改、风险状态、新增子任务、时间策划、完成状态、附件上传。
APQP工作细则要求
0
联系人清单
目的:
项目定点后,成立项目小组,明确各职能块项目人员以及联系方式
时间:
Gate 1项目定点后2周内
要求:
1.供应商项目开发团队,包括管理层及所有职能块(商务、工程、质量、生产、物流等)足
够授权的项目经理,明确支持项目的高层管理者。
2.客户项目开发团队,包括:采购员、DRE、SVE、 SQE 、ME、PCL、外观工程师、检具 工程师、模具工程师等
交付物:
联系人清单
1
Timing(时间进度)
目的:
参考客户的项目节点,供应商正向编制项目进度表,明确项目开发关键节点和各个 任务模块时间,保证项目按节点实施。
时间:
Gate 1项目定点后2周,每阶段review,贯穿整个项目开发过程
要求:
1. 节点的设计是基于项目状态的正向,而不是SGM要求节点的倒推;
2. 项目Timing包含但不限于:模检具,工装,实验,产线,人员招聘/培训,PPAP,包装物 流,分供方等子计划;
3. 至少每次阶段评审时需更新Timing,任何信息变化(节点,EWO,关注点等)都应实时更新Timing,并与PDT保持沟通;
4. 任何影响到项目进度、交样进度的问题,应及时向SQE报警。
交付物:
注意格式要求
2 Open Issue(问题清单)
目的:
项目交流工具与方式,有效跟踪项目开发中的问题点和当前阶段的问题关闭状态 p时间:Gate 1项目定点后,每阶段review,贯穿整个项目开发过程
要求:
1. Open Issue内容包含但不限于: 完整、准确的问题描述插图说明,问题发生阶段/来源,严重度,
责任人,根本原因分析,长短措及断点,解决状态等
2. 问题收集:任何零件、项目相关的信息都应记录在APQP问题清单中
内部问题,项目管理、商务问题、工程开发、过程开发、批产认可、产能规划、分供方管理、 质量体系;
外部问题,设计评审、设计验证、尺寸匹配、现场造车(装配、DR/DRL、GCA)等
3. 根本原因分析要深入,问题处理彻底
4. 实时更新open issue,并与PDT保持沟通,风险问题及时上升报警;每次阶段评审时需 review
open issue;
5. APQP问题清单是经验教训的积累,不应删除任何已完成的内容。
交付物:
格式要求,满足要求即可
3
Lesson Learned(经验教训)
目的:最大限度地利用以往项目中获得的知识并总结现有项目中碰到的问题,避免重复讨论 同样的质量问题与设计问题,同时总结本项目的经验教训,为后续项目提供参考。
时间:
Gate 1开始,每阶段review,贯穿整个项目开发过程(模具TKO之前2周,产线评审、三大 文件)
要求:
1. L&L来源:供应商经验教训数据库(总部或海外兄弟工厂,工厂内部,新项目,现生产, 售后),类似车型的问题清单,类似产品EWO更改清单;
2. 供应商在启动会议时需开始组织经验教训清单,列出以往类似项目的质量问题与设计问题;
3. 项目开发过程需不断完善经验教训清单,并在各阶段评审进行回顾,并确认每条经验教训都有对应措施并被落实;
4. 确保制定正式流程规定在经验教训的基础上更新FMEA和控制计划;
交付物:
经验教训库;经验教训review记录
4
SQSpecialSOR
目的:
充分理解与识别SOR内容(包括Special SOR),转化为供应商内部具体的开发信息
时间:
Gate 1拿到SOR要求,Gate 2 将其解读并落地(deadline TKO前)
要求:
1. 采购会将SOR统一发给供应商;(Special SOR从SQE处获得)
2. 供应商充分解读对于SOR里关于技术要求,质量要求,包装物流要求进行评审,形成SOR评审报告提交SGM项目团队确认;
3. 如有无法满足SOR要求的问题需及时向SGM项目团队
提出并沟通;
4. 对于SGM SOR的各项要求如何满足的方案评审, 并落地到相应控制措施;
交付物:
SORSpecial SOR解读报告及checklist
5
CommericialIssue(商务问题)
目的:
为避免由于商务问题的敲定,导致项目进度的延误
时间:
Gate 1 kick off 完成定点合同;
Gate 2 完成PO(Deadline 模具TKO);
要求:
1.项目kick off 之前应完成定点合同的审批,确认LCR,SDC等相关要求。
2. 模具TKO之前,应完成PO审批,避免影响模具加工 3.EWO文件的及时释放,避免影响项目进度。
交付物:
记录在open issue list
6
HumanResource&Operator(人员配备计划)
目的:
保证项目开发团队人员配置;确保新工厂/新产线人员按时到位,制定对口的、有效 的培训计划,使得员工的知识、技能、工作方法、工作态度以及工作的价值观可以满足。
时间:
Gate 1提供初版人员配置(主要项目团队);
Gate 3提供正式版人员配置(主要量产后人员) 项目启动后
Gate 5量产人员就位并完成培训
要求:
1. 项目启动后提供初始人员配备计划,包含项目开发人员配置及量产后各过程人员需求
2. 项目开发人员包含:技术,开发,质量,生产、物流等人员在项目定点后1M就绪,并完成项目相关培训。
3. Gate3前提供签字版的人员配备计划,确定正式的人员安排
4. 量产后各过程人员包括:生产、质量、物流等在Gate5之前就绪,并完成相关知识点的培训。
交付物:
人员招聘计划
人员培训计划
7
DesignReview(设计评审)
目的:
为规范产品的设计评审、验证,确保设计输出满足相应阶段设计输入的要求,SGM 与供应商如何确保设计规格在制造工装模具和量检具之前被充分定义
时间:
Gate 1供应商与工程确定设计评审计划;
Gate 2完成设计评审。
要求:
1. 设计评审是着重于对设计的可制造性方面的评审;
2. 设计负责人(SGM/供应商)需确定时间召集KCDS研讨会, GD&T评审和数模评审;由
DRE、SQE、供应商及其他相关人员参加,定义关键产品特性与关键过程控制特性,评审数 模及GD&T;
3. 输出对应的评审会议纪要,记录评审问题并跟踪,直至问题有效关闭;
4. 需确认数据来源,版本确认,模流分析,GD&T和数模对应性等,对图纸中公差标注或工 艺要求有疑问,应及时和DRE、SQE沟通;
5. 供应商应与SGM 确认外观规范, 材料和性能测试要求, 并与SVE 确认试验清单, 如ADVP&R清单
6. 梳理适用的经验教训。
交付物:
设计评审计划
设计评审会议纪要
设计评审问题清单,记录在open issue list
8
DFMEA
目的:
在产品设计阶段,预先发现、评价产品可能潜在的失效与后果,及早找出能够避免或 减少这些潜在失效发生的措施,并将此过程文件化,为以后的设计提供经验与参考
时间:
Gate 1产品设计过程 p要求:
1.供应商若不负责设计,则向SGM设计工程师提供相关的经验教训,并支持DFMEA的开发;
2.供应商与设计工程师制定DFMEA评审计划,记录严重度9和10的风险问题并进行跟踪直至
问题有效关闭;
3.若供应商负责设计,则要保证所有分零件的DFMEA均已完成,并推动开发和实施;
4.DFMEA识别的关键控制点输入PFMEA中
交付物:
DFMEA评审计划及会议纪要
DFMEA评审问题清单,记录在open issue list
9
Validation Plan(实验计划)
目的:
根据SOR要求,充分解读实验相关要求,制定有效的量检具和验证计划
时间:
报价时提供初版ADVP清单;
Gate 2制定ADVP(数据释放),并发给SVE、DRE进行确认(功能、耐久实验报告),提 供时间、评审时间、试验项目解读;(关注暴晒实验的等级:拿到耐光照等级进行确认),在
IVER前获得批准;
Gate 3 PV实验开始(Deadline VTC节点前1-2周),并完成GM3660批准或者PATAC工程
认可报告(Deadline VDC节点前)
要求:
1. 如供应商无需做DV实验,则需向DRE了解DV实验进度和实验结果,有效识别失效风险;
2. PV实验零件必须是正式生产地生产的零件,PV实验零件分供方必须与PPAP及量产一致;
3. 材料实验计划,需要确认是否存在新颜色原材料,是否通过原材料级实验认可;
4. 供应商跟踪实验进度,有问题及时报警PDT;
5. 型式试验条目
交付物:
被批准的ADVP DV/PV实验计划 GM3660/1411
10
Design Records(设计记录)
目的:
对最新的数模、图纸版本进行跟踪
时间:
Gate 1与工程确认3D2D释放计划,
Gate 2使用最新版进行模具、检具开发, 每阶段review数模、图纸是否为最新版本
要求:
1.与DRE沟通数模,GD&T发放时间计划
2.数模,GD&T来源与版本确认,并与工程确认;
交付物:
新产品信息开发确认表
正式数模,正式GD&T版本
11
EWO
目的:
形成EWO跟踪清单,记录产品更改,理解工程更改原因及意向,对EWO进行有效评 估和跟踪;同类产品L&L获取来源
时间:
Gate 1建立EWO跟踪清单,每阶段review,项目整个开发周期
要求:
1. 根据工程更改流程进行,做好工程更改评估,包括质量维度,商务维度,时间维度 ü质量维度(SQEDRE):工艺可行性、合格率、产能
ü商务维度(DREBuyer):工时、材料、合格率、人员、设备/工装/模具/检具 ü时间维度(物流DRESQE):修模时间、验证时间、断点时间
2. 工程更改文件必须经过书面确认,由DRE释放,采购员、SQE同意后进行实施,DRE输入 正式变更数模和GD&T
3. SORP后的工程变更需申请PTR
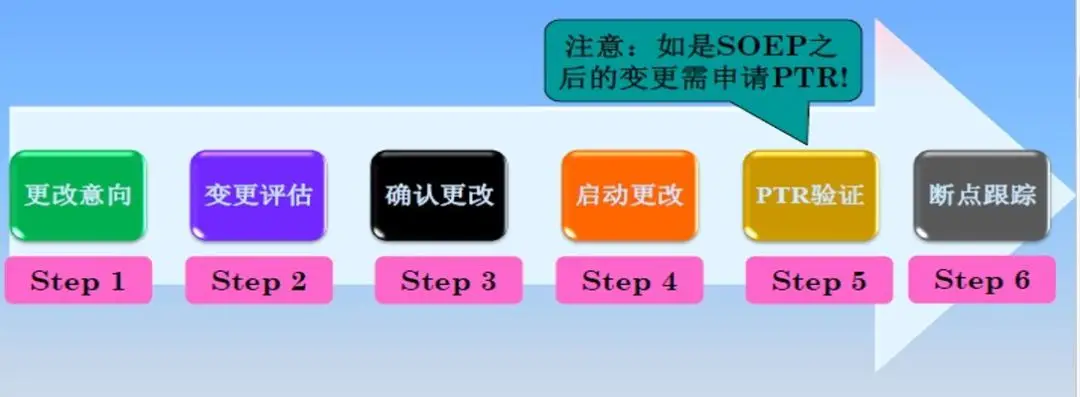
交付物:
被批准的EWO文件/EWO方案
EWO清单(履历记录)记录在open issue list—PPAP交付物
12
LayoutandProcess Flow(布局和过程流程图)
目的:
合理的生产场地和物流路线并形成过程流程图。
时间:
定点前完成初始Layout及流程图,每阶段review,
Gate 2明确Layout及过程流程图, Gate 4得到SQE认可
要求:
1. 生产车间现场所有用途不同的区域(成品区/半成品区/返修区/GP12区等等)都应有明确
的界限和标识,并应有相应的责任人负管理
2. 生产车间现场所有地面画线应清晰、美观,各类标识(地面标识、标识牌)都应完好有效
3. 生产车间现场所有物品摆放均匀应严格按照车间定置管理平面图进行
4. 关注GP12区域的规划,标准光源等
5. 合理的物流路线(原料区-机台/生产线-GP12区-发运区)
交付物:
场地布局图---PPAP交付物、过程流程图---PPAP交付物
13
PFMEA
目的:
PFMEA的开发、编制、更新、落地
时间:
1.项目报价提供一版初始PFMEA;
2.TKO后1个月更新PFMEA;
3.T0前更新试制版的 PFMEA,用于指导试制阶段生产,之后每阶段进行评审更新;
4.PPAP前提供正式版PFMEA,用于指导量产阶段生产。
要求:
1.定点前初始PFMEA是报价文件的必要文件
2.设计变更,过程变更,材料或生产场所变更时,需评估PFMEA,必要时更新
3.跨功能小组共同编制PFMEA,并确定控制计划的KCC参数
4.按PFMEA 风险系数列出前10的高风险项,与SQE共同确认需改进项目并制订改进措施, 每月更新的基础上监督进展情况
;
5.确保PFMEA和生产过程流程图、控制计划相关联;
交付物:
PFMEA---PPAP交付物
14
Control Plan(控制计划)
目的:
控制计划的编制、更新、落地
时间:
1. 项目报价提供一版初始CP;
2. TKO后1个月更新CP;
3. T0前更新试制版的CP,用 于指导试制阶段生产,之后每个阶段进行评审更新;
4. PPAP前提供正式版CP,用于指导量 产阶段生产
要求:
1. 根据类似零件控制计划编制初始控制计划,并作为报价文件的质量内容提交
2. 以初始控制计划为基础,制定试生产控制计划和生产控制计划;
3.生产场所须证明保留过程控制计划,并针对KPC,PQC制定独立的过程控制图并保留;
4.在控制计划上标注KPC,PQC已经对应的KCC控制点;
5.分供方的控制计划评审 ;
6.控制计划与流程图、PFMEA的关联
交付物:
控制计划---PPAP交付物
15
Gage Review(检具)
目的:
检具制作跟踪,按照最新发布的GD&T图纸及ME发布的测点图进行量检具设计、制造和认可, 确保检具开发符合产品要求和进度要求
时间:
Gate 1建立检具开发/评审、制作、验收、使用计划,每阶段review,
Gate 2图纸释放后进行评审并完成A/B表(检具设计认可/检具制造认可)认可,
Gate 3 MC进行验收,
Gate 5 PPAP上传所有认可
要求:
1. 检具供应商必须在SGM清单内选择
2. 与检具工程师制定检具评审计划,需检具工程师,DRE ,SQE参加,输出评审问题清单进行跟踪并有效关闭
3. 参与设计评审,确保图纸方案的发布,确保KPC、PQC、AQC等要求反映到最终的检具设 计中;
4. 检具TKO前完成检具A表的签署, MC走访前完成C表签署,MC2完成检具B表的签署;
5. 必须对检具进行测量系统分析;
6. 完成设计、制造及检具尺寸方面的认可,满足GM1925的要求。检具制造批准完成后将相 关文件归入PPAP
交付物:
检具评审记录
检具加工进度表
ABC表及其他文件( CMM 测量报告、GR&R报告、检具操作指导书、检具图纸) ---
PPAP交付物
16
Equipment & Facility Review
设备/工装/产线&厂房
目的:
对新投厂房,新投设备/工装/生产线进行充分评估,满足项目节点要求
时间:
新投设备/工装/产线&厂房在Gate 1 Kick off建立计划及跟踪,每阶段review生产线评审在Gate
2 完成( Deadline TKO+1M )
Gate 4 厂房、生产线Ready(Deadline PPV)
要求:
1. 新工厂/厂房计划,包括审批,各项许可证完成,厂房施工、厂房验收等;新建/扩建工厂 必须在PPAP前通过PSA评审,否则SGM将指定第三方对供应商零件进行100%检测,且供应
商承担所有相关费用;
2. 新投设备、工装计划,包括合同签订,采购周期,进厂,组织调试等;
3. 根据最新的数模,设计,制造工装、设备;
4. 厂房、设备、工装需满足项目节点要求,每周定期进行review,有问题(变更、进度等) 第一时间通知SQE;
5. 生产线布局(包含防错)及生产线整体评审(工艺流程、防错、与BP对比、LL输入、产能)
6. 评审过程确保GD&T,KPC,PQC和AQC的要求涵盖在工装、设备和功能性测试设计中;
交付物:
设备/工装/产线计划及跟踪 厂房计划及跟踪
生产线评审记录
17
ToolingReivew(模具)
目的:
模具制作review,确保模具开发符合产品要求和进度要求 p时间:Gate 1 Kick off建立计划及跟踪,Gate
2完成模具评审及检具A表签署(Deadline模具TKO之前),Gate 5 完成模具B表签署(Deadline
PPAP 前)
要求:
1. 确保模具开发符合产品要求
2. 确保模具开发符合进度要求
交付物:
模具开发计划及跟踪
模具评审记录、模流分析
模具A/B表及其他文件---PPAP交付物
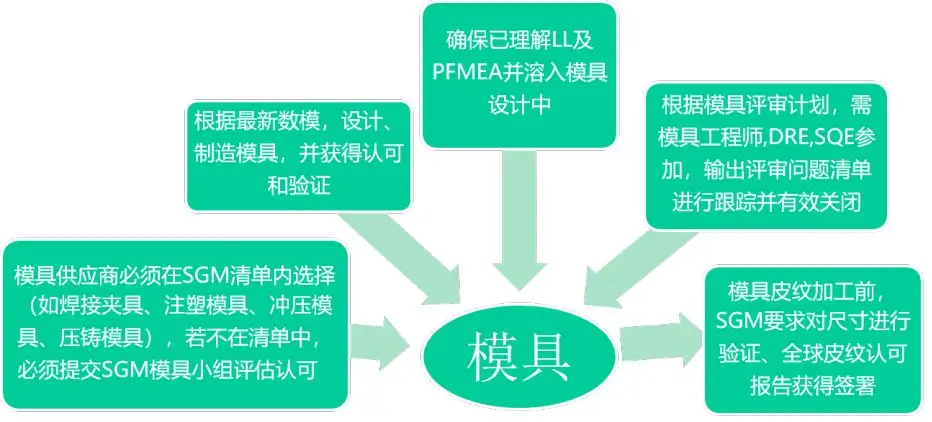
18
.0 Error Proof(防错)
目的:
对于有防错要求的产线或零件,有效进行防错评估与评审。
时间:Gate 2数据释放进行防错清单建立及评审,Gate 4 完成防错落地( Deadline
PPV前) Gate 5 完成SGM认可( Deadline PPAP前)
要求:
1.充分识别产线或零件要求(SORLL工程技术要求等),对产品关键特性进行评估;
2.防错设计方案评审及加工进度跟踪(见设备工装计划);
3.有效的防错验证(PPAP前完成),并获得批准。
交付物:
防错清单
防错设计方案
设备工装计划及跟踪
18
.5 SPC
目的:
项目阶段对过程进行研究监控,识别一个过程、数据统计分析、规范和控制,通过数 据的分析,作预防性调整和维护,使过程达到受控的要求;
时间:
T0开始
要求:
1. 供应商必须确认所有的特殊特性(SGM或供应商指定)的初始过程满足SGM要求。
2. 工程输入、KCDS&工艺评估、加工设备过程能力、测量系统稳定性
3. 测量系统的准确性,对SPC数据的真实性和正确性十分重要,否则会影响SPC数据的准确 度,导致浪费甚至起误导作用。因此,对实施SPC工序的测量系统必须进行严格地分析和检
查
交付物:
过程能力分析---PPAP交付
19
GP12
目的:
建立GP12流程;在早期生产阶段, 自主发现问题并及时解决;确保缺陷不溢出;验证在启动、加速期间或工艺修改后过程控制的稳定性;确保产品在量产阶段的质量
时间:
首次正式交样前至SOP+3并满足退出标准,每阶段review
要求:
1. GP12区域内发现的问题,根据定义原则(严重度、频次)进入Open issue list并跟踪;
2. GP12每阶段检查清单/问题均要反馈内部责任部门、管理层、主管SQE ;
3. 要求所有分供方需遵守GP12,并监控和维护GP12数据记录;
4. 原则上GP12区域的100%检查必须在成品检验后执行,不允许在GP-12区域进行任何返修;
5. GP12标签,由管理者签名的绿色圆形(直径3.2 ~ 5 CM)标贴,黏贴产品或发运标签旁
。
6. GP12的退出需满足标准(时间、质量问题解决、无新增问题、SQE批准);
7. 延伸:外观及功能性零件,GCA/Audit流程建立及实施;
8. GP-12期间在顾客处出现质量问题可能直接进入CS-1/2。
交付物:
GP12作业指导书
GP12问题检查清单 GP12缺陷记录
GP12标准化,将GP12归纳为: “1/2/3/7”:
1个场地:GP12需要一个独立于生产现场的区域,充足的照明,必要的工装、有效的量检具,确保检验有效性。
2个物料框:黄色框用于放置有缺陷但可以返工的物料,红色框用于放置直接报废的物料。
3个标识:绿色,GP12检查通过。黄色,GP12不通过,需返修。红色,GP12不通过,直接报废。
7个文件:
GP12区域组织机构/检查人员矩阵图;
GP12报警机制流程;
GP12检查清单(最新版);
GP12作业指导书;
GP12缺陷记录(描述,数量,时间,etc);
GP12质量数据趋势图表(生产合格率图表、柏拉图等)
GP12问题解决跟踪表(Open issue list内)
20
DimensionPlan(尺寸认可)
目的:
保证产品尺寸开发质量与进度;确认测量位置,测量零件尺寸是否满足图纸要求(包 括尺寸公差和技术要求)确保零件合格,确认零件和测量系统的稳定性
时间:
Gate 2 完成测量计划(Deadline TKO+1 ),各阶段review, Gate 3
完成尺寸认可(MC)
要求:
1. 供应商必须按照SGM确认的有效图纸、数模和特殊特性,制订零件的全尺寸测量计划;
2.测量计划,包含各阶段( IV/OTS/MC/PPV/NS/S/SORP) 测量策略(测量计划、工具、
人员、频次等);
3. 阶段合格率要求:IV 70%;MC1 80%;MC2 90%;PPV 100%
4. 每次交样前,尺寸报告反馈SQE;如有超差点,与MEQESQE针对超差部分进行评估,
供应商制定并实施相应纠正措施。
5. 对于有MC要求的零件,供应商必须获得SGM ME批准的MCAR
交付物:
尺寸测量计划
测量计划---PPAP交付物 尺寸报告---PPAP交付物
21
.0 AppearancePlan(外观认可)
目的:
保证产品外观开发质量与进度;对产品的外观状态进行策划和认可
时间:
Gate 1 Kick off供应商提供外观开发计划,各阶段review
Gate 2外观图纸释放后供应商完善外观开发计划
Gate 4 完成光板认可/皮纹认可( Deadline NS前)
Gate 5 完成外观认可( Deadline PPAP前)
要求:
1. 供应商根据工程释放的的外观图纸要求,明确零件外观要求及开发计划(包括:光板认可, 皮纹加工、皮纹认可、外观认可等);
2. 皮纹件认可之前必须通过光板件认可,光板件底色必须为黑色,色板需在指定的网站购买;
3. 皮纹加工前必须通过尺寸认可(特别设计A面区域);
4. 对于有外观要求的零件,供应商必须获得SGM 外观工程师批准的AAR。
交付物:
外观开发计划
GIF---PPAP交付物 AAR---PPAP交付物
21
.5 BuildPlan(零件生产计划)
目的:
根据正向零件开发制定生产计划,满足项目节点交样要求
时间:
Gate 1根据项目节点定制定零件生产计划,各阶段进行review更新
要求:
1. 计划包含各阶段样件生产操作人员、生产地与设备、原材料、生产方法(手工件or软模件 or硬模件、正式工装or非正式工装等)、生产数量、生产时间(包括T0试模)
及各工序计 划;
2. Build Plan按照项目正向样件生产时间安排,但需要满足交样时间MRD;如有特殊情况与
SQE进行沟通。
3. PPV1及MC2交样零件尽量要求在Home Line生产;
4. 原则上要求:Salable~SORP+3Months之间不允许移地生产;
交付物:
Build plan
22
TierSupplier Manage(分供方管理)
目的:
传递对下级供应商的开发要求,实现对整个供应链的有效开发与管理
时间:
Gate 1建立分供方管理计划,
Gate 2确定初版分供方清单并得到SGM签署确认(Deadline 数据释放+1M )
Gate 3 完成最终版分供方清单(Deadline PV实验前)
Gate 5 认可核实一致性( Deadline PPAP )
要求:
1.供应商必须按照APQP开发计划形成材料及分供方清单,并得到认可。
2.该清单必须经泛亚DRE、泛亚Material Team及SQE三方签字认可。
3.供应商对于该清单中任何项目的更改,必须提前通知SGM SQ和泛亚工程,并进行相应的
验证与认可。
4.分供方清单应包含:原材料、外协二级零件、DB零件等
交付物:
分供方管理计划
分供方清单---PPAP交付物
23
PPAP
目的:
PPAP是用来确定供应商是否已经正确理解SGM工程设计记录和规范的所有要求,以 及该制造过程是否在实际生产运行中,按照生产节拍持续生产满足SGM要求的产品
p时间:
Gate 2 完成PPAP审核计划(一级零件及分供方), Deadline TKO+1M Gate
5 完成PPAP(S-PPAP/FULL-PPAP) , Deadline S前4周
要求:
1. 与SQE共同确认的时间,安排在正式的生产条件下生产指定数量的零件,并通过SQE的现 场评审;
2. SQE在进行总成零件PPAP前,供应商必须完成分供方处的PPAP,并提交相关证据;
3. 当PPAP提交时,若不能完全满足生产批准要求,需在提交有SQE及其他相关人员签字认可
的GM1411,GM1411中需包含详细的行动(补救)计划;
4. 只有PPAP批准状态(EP中PPAP状态)是批准或可销售批准的零件才可用于可销售车制造;
5. 与PPAP审核时相比的任何过程变化都应在PPAP重新提交前通知SQE ;
6. 根据PPAP检查清单跟踪交付物准备情况;
7. 违反PPAP程序(如擅自更改原材料、分供方、工艺、检验标准等)进入CS1。
交付物:
PPAP交付物跟踪清单
24
Package
目的:
确保零件妥善存储,避免在周转、运输过程中受到各种撞击、挤压等造成的破坏
时间:
Gate 2 完成包装方案计划,
Gate 4 完成正式包装方案签署( Deadline NS阶段前) Gate 5 使用正式包装交样(
Deadline S阶段前)
要求:
1. 包装计划与包装工程师确认完成,包括:内包装、外包装,各阶段临时包装、正式包装;
2. 包装方案根据零件进行设计,并进行有效的验证,最终得到包装工程师认可;
交付物:
包装方案确认单---PPAP交付物
25
Run @Rate/Capacity
目的:
要依据SGM项目开发的需求制定生产计划和产能爬坡计划;在正常的生产条件以及满 足所有客户需求(质量/产能),验证供应商对于该零件的实际生产/排序能力是否能够满足
时间:
报价阶段提供初始产能评估,Gate 2完成初始产能设计(产线规划),各阶段生产能 力验证评审,Gate
6 产能正式认可
要求:
1. GP9包括质量和产能两方面要求;
2. 严格按照Run @ Rate/Capacity流程进行;
3. 供应商必须于正式运行前模拟运行一次,以确保准备就绪,并且正确填写A、C、C-1、C- 2、C-3表,提交给SQE。
交付物:
生产计划
产能爬坡计划
产能分析(5个附件)---PPAP交付物
26
关键特性
目的:
促进产品设计的有效性、合理性和实用性;支持制造和装配过程中,对变差的降低和 保持及监控活动,从而改进产品的质量和制造经济性
时间:
Gate 1根据工程要求/类似产品LL等形成初版关键特性清单,并与PDT评审, Gate 2数据释放后确定关键特性清单,各阶段进行review更新。
要求:
1.关键特性清单落地到产品设计评审、产线工艺评审、防错、PFMEA、CP、GP12检验等;
2.关键产品特性KPC控制要求:Cpk≥1.67,或通过100%检验或者防错措施等手段实现;产 品质量特性PQC控制要求:Cpk≥1.33,或通过100%检验或者防错措施等手段实现。
交付物:
KCDS清单
27
GammaDeviation
N.A.
28
追溯性
目的:
项目开发阶段策划零件追溯性,满足SGM对产品的追溯要求;获取和保存与产品相 管的关键信息,实现零件-整车-车主之间关键信息互查,降低SGM和供应商的质量安全风险。
时间:
Gate 1根据SOR、 Special SOR、 工程其他技术要求明确零件追溯要求; Gate
2产品评审、工艺策划、产线评审等实现追溯要求,每阶段review; Gate 5 PPAP完成零件追溯性(
WMS系统)
要求:
1. 根据要求零件确保达到SGM对产品的总成级追溯要求,精确追溯性、一般追溯性(评审表)
2. 建立和保持满足SGM要求的质量追溯系统,包括关键二级零件;
3. 当发生召回或质量溢出时,提供SGM精确的可疑范围区间
4. 总成产品要有唯一标识性标签,且标签条码符合SGM要求(GM1737/GMW15862),通过
总成条码标签,要能追溯到次级零件的生产批号,反之亦可
交付物:
零件追溯性方案及评审跟踪、一般追溯性评审表
29
清洁度
目的:
对产品生产过程、运输过程、储存过程中的清洁度要求,需要进行测量、监控、控制、 预防,防止异物对质量的影响
时间:
Gate 2明确零件清洁度要求,体现到产品设计、工艺设计、PFMEA、CP等, Gate 3 第一次交样前完成各区域清洁度管控落地。
要求:
1. 所有零件的清洁度 按要求会在产品设计 的SOR及图纸上注明;
2. PFMEA开发过程应该考虑零件和过程的清洁度;
3. 根据异物控制要求,生产各个区域都要有对于产品周围环境的清洁度要求文件;
4. 具体其他要求请参考BIQS-25异物控制条款。
交付物:
无具体格式要求,满足要求即可
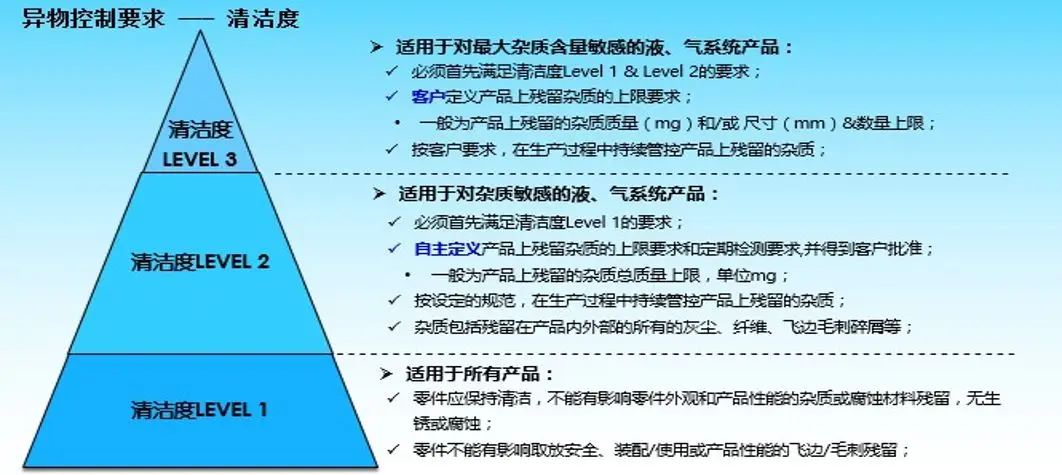
30
BIW时效性
目的:
项目开发阶段定义明确BIW时效性零件控制;车身上的部分零件受材料物理、化学特 性影响需要进行时效性(包括温度)控制,超过期限、温度限制条件会影响最终产品质量
时间:
Gate 1根据SOR(H1表)、Special SOR、工程时效性零件清单明确时效性零件要求;
Gate 2完成BIW时效性零件控制方法;
Gate 3、4验证控制方法并review,最终落地到控制文件
要求:
1. BIW时效性零件主要5类
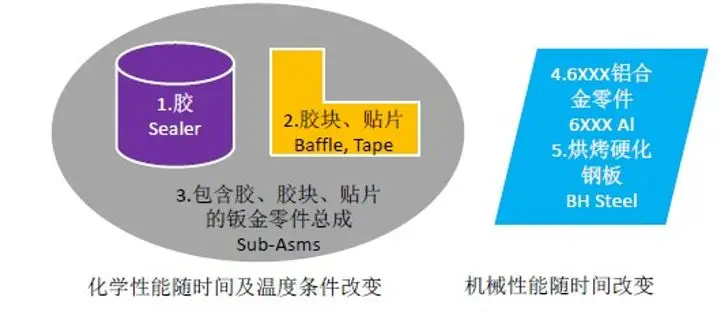
2. 管控方法涵盖:采购订单管控、原材料管控、生产管控(工艺、工装、操作方法等)、检 验管控、物流管控(周转、存储、运输)
交付物:
BIW时效性零件清单 BIW时效性零件管控方法
31
VIAQ
目的:
项目阶段对VIAQ工作的策划;车内空气质量,测试汽车车向内空气中允许存在的挥 发性和半挥发性有机化合物(VOC和SVOC)含量的法规。
时间:
Gate 1根据SOR、工程技术要求等,明确零件VIAQ要求及测试计划;
Gate 5 PPAP前完成连续稳定的三次袋子法测定。
要求:
1. 根据计划在SGM认可实验室进行VIAQ测试;
2. 零件PPAP节点前完成连续稳定的三次袋子法测定结果 至少MC/OTS、PPV、NS各一次;
3. 结果均需要作为交付物更新于APQP Review中,并且最后三次测试都合格才能拿到Full
PPAP,如有相关VIAQ问题导致的PPAP风险尽早识别;
4. 新项目VIAQ要求向Tier2和材料供应商进行延伸;每次测试包含总成和同批次关键子零件
交付物:
VIAQ测试计划及跟踪;VIAQ测试报告
32
GP10
目的:
即对零部件供应商开发、验证及质量控制实验室的评估和认可程序
时间:
Gate 2进行DV/PV实验时实验室选择关注;
GP10申请和文审必须在Gate 3完成(DV/PV前),现场评审在Gate 5完成( PPAP前)
要求:
1. 所有的试验项目都必须由获得SGM GP10认可的实验室完成;
2. 如需委托第三方进行试验,此第三方实验室必须通过ISO17025认可以及SGM的GP10认可;
3. GP10认证的试验范围和认证有效期符合要求。
4. 注意GP10使用范围,实验室及在线的生产检测设备和检测方法(如果SGM-SOR等技术协议有要求)。
交付物:
GP10认可证书
33
BIQS
目的:
对供应商的管理体系进行评估及跟踪,保证供应商的质量体系更符合SGM的要求。
时间:
Gate 1提供实施BIQS差距分析评审及推进计划;每阶段review;
原则上Gate 5完成BIQS认可( PPAP前)。
要求:
1. SGM对于供应商基础质量管理体系的要求;
2. 每阶段review BIQS推进进展;
3. 现阶段Level 3是合格的最低要求;
4. 其他要求详见BIQS培训教材。
交付物:
BIQS推进计划及跟踪 BIQS认可证书(系统)
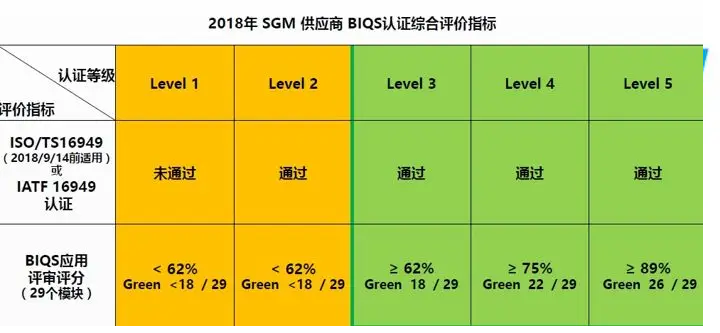
34
3C
目的:
策划3C零件3C认证与报备,满足项目节点
时间:
Gate 1根据要求确定零件是否有3C要求,
Gate 3零件T0/T1/T2后进行3C申请认证,
Gate 4(-33周)完成零件3C认证与报备(泛亚)、实物核对照片。
要求:
1. Gate 4阶段要确认零件3C标识的一致性确认;
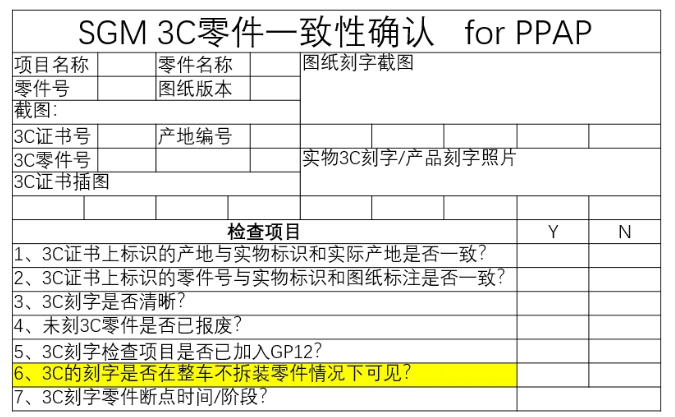
2. 零件申报周期是90天(13周)
3. 零件在申报3C后,如有更改,要进行更新或说明,具体流程可咨询泛亚相关部门。
4. 供应商关注:
法规标记加施方式(模制/模压、印刷、喷码、打印在标签上、贴于产品包装袋上);
带法规标记物料上线时间及对应造车阶段;
GP12检查清单是否包含对法规标记的检查;
交付物:
3C认证证书 实物3C照片
3C一致性确认清单 |