编辑推荐: |
本文主要介绍了大数据建模应用案例,从方案简介、详细方案说明及BMS应用示例三个方面进行讲解的。希望对你有帮助。
本文来自BONA,由火龙果软件Linda编辑、推荐。 |
|
随着新能源汽车的发展,汽车新产品推向市场的速度越来越快,对汽车厂商的开发周期和设计方案快速验证的要求越来越高。
汽车电子控制器嵌入式软件开发也需要在研发早期阶段开展更充分的验证与测试,以便达到一次设计正确的目的,节省开发成本,缩短研发周期。
ETAS作为汽车行业一流的嵌入式软件研发工具与服务供应商,提供的新能源汽车嵌入式软件开发测量与验证解决方案。
一、方案简介
客户能够方便的采用数据测量与数据分析的方式建立虚拟车辆及ECU仿真模型,并基于该模型开展模型在环(MIL)仿真测试,软件代码在环(SiL)仿真测试以及硬件在环(HiL)测试以及车辆故障模拟与诊断等验证与测试工作,以达到一次设计正确的目的。
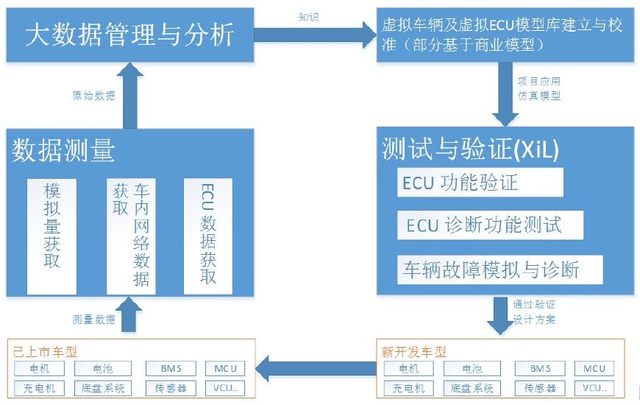
图1-1基于大数据建模的新能源汽车仿真测试方案
新能源汽车包含电机,电池,充电装置,发动机,底盘相关组件以及大量电子控制单元及传感器。各部件的功能参数的测量大致可以分为模拟数据信号,ECU变量参数以及网络总线信号等三类。
从图1-1中可以看到ETAS采用数据测量设备在实车及功能台架上对该部分数据进行测量,并将测量结果上传到大数据库。
ETAS大数据管理与分析工具对大数据参数进行分析,提取有效的数据信息并结合相关商业化的车辆子系统模型进行参数校准和迭代优化,从而帮助用户建立准确的虚拟车辆及虚拟ECU模型库用于ECU功能测试与验证以及车辆故障模拟与诊断环节。
在测试验证(XiL)环节调用虚拟车辆及虚拟ECU模型库中的虚拟车辆仿真模型开展模型在环,软件在环以及硬件在环测试验证,能够完成ECU功能验证,ECU诊断功能测试以及车辆故障模拟与诊断方面的开发工作,达到快速高效验证新的设计方案的目的。
二、详细方案说明
基于大数据建模的新能源汽车仿真测试系统包括数据测量,大数据管理与分析,虚拟车辆及虚拟ECU模型库建立与校准,测试与验证(XiL)四个环节组成。四个环节的工作逐步开展,循环迭代。
1)数据测量
数据测量包括ECU内部数据获取,车内总线数据获取以及模拟量数据获取,特别是对于新能源汽车电机、逆变器和整流器等设备频率高达100KHz的信号测量,ETAS提供完整的解决方案。
如下图2-1所示, 整个数据测量系统分为通讯总线/协议、硬件接口和上位机软件三个层次。ETAS提供从通讯总线/协议及仿真存储器(ETK)的软硬件集成、硬件接口模块ES8xx/ES5xx和模拟量采集硬件ES41x,到测量标定一体化的上位机软件INCA。
有了这样完整的解决方案,用户能够方便高效地对整个汽车嵌入式控制系统进行测量与标定,使车辆拥有完美的性能表现。
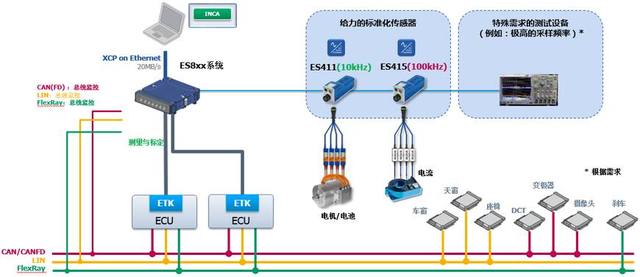
图2-1嵌入式软件开发测量与验证方案
2)大数据管理与分析
目前的汽车嵌入式控制系统开发环境下,人们可以通过各种各样不同的途径(如真实物体、仿真环境、模拟计算等)获取描述目标系统行为和表现的海量数据。
正如前文所述,ETAS数据测量环节获取了大量的ECU内部以及模拟量数据,如何存储并有效地利用这些数据,并从中发掘出目标系统的潜力,用以指引进一步的研发过程,成为极其重要的课题。
ETAS为此提供整套系统化解决方案,从数据采集(DAQ)、数据存储、数据索引/快速检索,以及数据报告自动生成。如下图2-2所示,ETAS
EADM(汽车电控系统数据管理)软件提供灵活多变的索引/检索条件,以便用户能够快速、有效地定位目标数据,ETAS
Analytics Toolbox(数据分析工具箱) 提供多种可定制化的报告模板,并依据EADM检索结果自动生成报告。
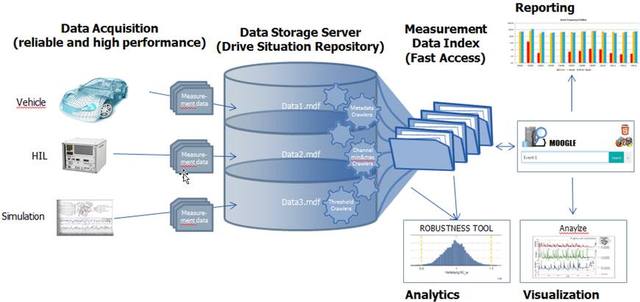
图2-2嵌入式软件开发测量与验证方案
3)虚拟车辆模型建模与校准
基于大数据管理与分析环节对测量数据进行的分析,我们得到了一些参数之间的相互影响关系,以及相关物理变量的特性曲线。如何将这些隐含在大量数据中的宝贵的知识和数据保存下来并为我们后续的系统仿真分析所用呢?
模型是一个比较好的保存方式,我们可以通过建立虚拟车辆及虚拟ECU模型库,为后续车辆及ECU的开发验证提供标准化的仿真模型。ETAS除提供相关车辆子系统模型,还提供基于数据的建模和参数校准等完整解决方案。
如下图2-3所示,ETAS提供的 ASCMO软件以现代化实验设计(DoE)方法,对目标系统进行快速地测量(台架或整车),依据这些反映真实系统行为的数据,建立数学模型以拟合和仿真目标系统,可用于对目标系统的虚拟标定/优化,更进一步地可将模型导出到其它环境(如硬件在环测试系统HiL,甚至是量产控制器)中作联合仿真和模拟控制。
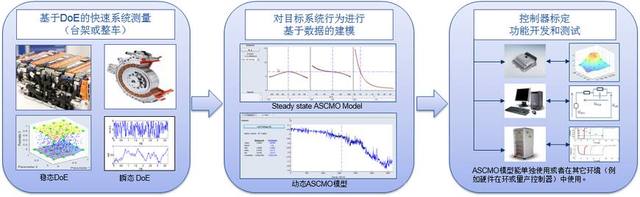
图2-3嵌入式软件开发测量与验证方案
4)测试与验证(XiL)
在测试与验证环节,通常包含模型在环验证(MiL),软件在环验证(SiL),虚拟测试系统验证(VTS)以及硬件在环验证(HiL)四个阶段,ETAS
提供COSYM实现在同一软件平台上开展四个环节仿真验证工作,如下图2-4所示。
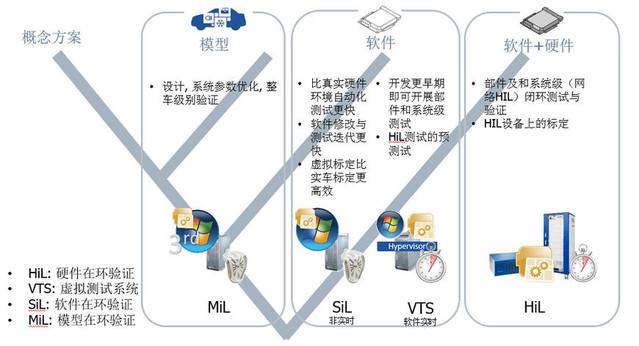
图2-4测试与验证(XiL)四个阶段
COSYM包含如下功能支持上述ECU测试与验证的四个阶段的工作:
① 能够方便的集成ETAS虚拟ECU模型,被控对象模型和环境模型,以及第三方模型和支持FMI2.0接口的模型。
② 采用虚拟总线或真实总线集成多个ECU,并能支持BUSMASTER,CANoe等总线监控工具的连接。
③ 方便配置测试工程和测试用例脚本,确保MIL/SIL/HIL应用之间的方便切换。
三、BMS应用示例
针对BMS系统的开发过程中也需要对电池单体,电池包,BMS控制器和充电控制电路和设备开展数据测量与获取,模型建立以及测试验证三个环节的工作。现结合实际项目对该测试系统在BMS开发应用流程做如下示例说明。
1)电池单体,电池包和BMS控制器的数据测量与获取
电池包与BMS控制器形成闭环控制系统,对其数据测量与获取通常我们需要开展三方面的工作。
首先在主正回路,预充回路以及充电回路上需要对各回路电压和电流进行测量,通常该回路电压较高(800V),电流采集精度要求也比较高。
其次对BMS中的相关变量和参数也需要进行获取,以确认控制执行的准确性。
最后需要在电池实验台上上对电池单体的特性参数进行测量,包括不同温度条件下的电池充放电特性,电压波动特性等。
如下图3-1所示,ES415测量模块配合CBN401系列探针测量电池单体电压,配合CBN400和CBN422系列探针测量电池包高压回路的电压和电流,ETAS专用测量标定接口ETK连接BMS控制器获取相关变量和参数信息。
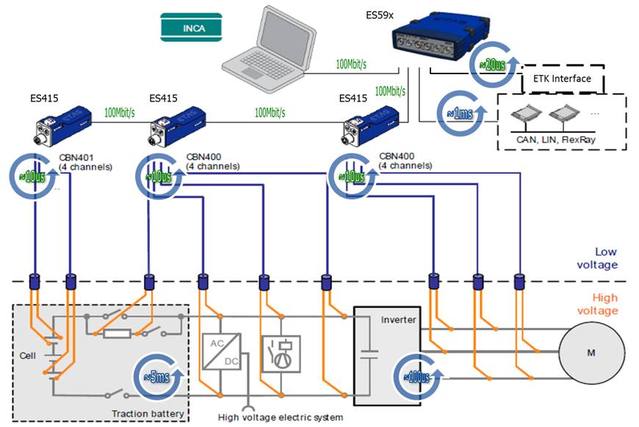
图3-1动力电池数据测量与获取
2)电池模型的建立与校准
对于电池模型我们通常采用二阶RC模型来模拟,模型中的部分参数需要根据实际电池单体测量数据进行拟合优化得到。具体拟合优化流程如下图3-2所示。比如电池模型中需要输入的电池内阻,电感以及电池不同温度下充放电特性参数等,都不能直接在试验台测量得到。
通常我们将电池单体不同工况下测量获取的电压,电流数据导入到ASCMO软件中,通过ASCMO内部高效的数据拟合与优化算法得到相应的电池特性校准参数,输入到电池模型中,以便获取更准确的电池模型。

图3-2动力电池模型建立与校准
3)采用HIL设备开展BMS测试验证
在HIL测试验证环节,如下图3-3所示,ETAS提供电池单体模拟设备和LABCAR软硬件设备建立HIL测试环境,将前期建立的电池模型下载到LABCAR系统与BMS形成闭环,开展BMS的测试与验证工作。
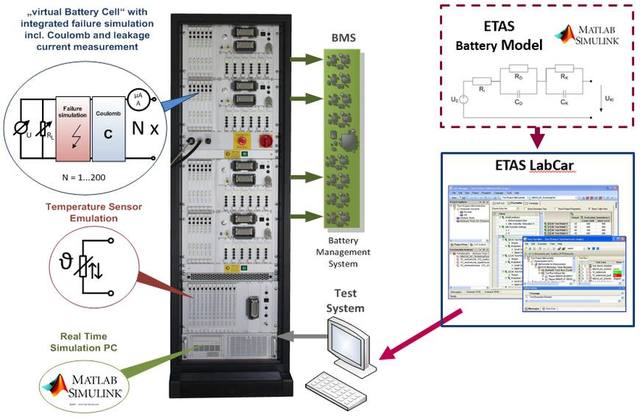
图3-3 BMS应用HIL测试验证
上述控制器开发仿真测试系统除能够应用于BMS开发过程,也能应用于MCU,VCU,ADAS等开发流程。
四、总结
ETAS提供完整的基于大数据建模的新能源汽车控制器嵌入式系统的开发解决方案,能够支持客户方便的开展数据测量,大数据管理与分析,模型校准优化以及系统测试验证等环节的工作,提高系统开发效率,以便达到一次设计正确的目的,节省开发成本,缩短研发周期。
|