编辑推荐: |
本文主要介绍了协作机器人的实现方式,及其上游、中游和下游介绍,希望对您的学习有所帮助。
本文来自于知乎,由火龙果软件Linda编辑、推荐。 |
|
1 协作机器人的实现方式
各大机器人厂商的机器人有配备各自的安全技术,例如ABB的SafeMove,Fanuc的DCS,KUKA的KUKA.safe,但其安全功能本身还比较初级,例如将物理的围栏换成了虚拟围栏、检测到有人靠近时自动停止,与完整的协作安全技术仍有差距,那么什么是真正的协作技术?
UR协作机器人的关节是模块化中空电机+中空减速器+双编码器构造,这种模块化关节质量轻,可以低成本检测外力干扰,从而实现机器人与人协同工作。
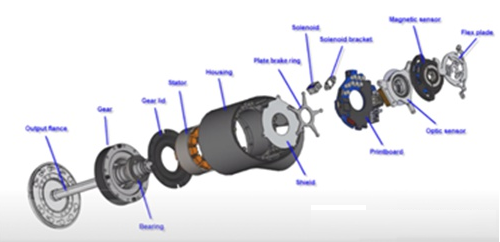
KuKa则是基于含力矩检测的模块化关节,这类关节是目前最复杂最先进成本最高的关节,代表下一代机器人的方向。它相比UR类型的关节多了力矩传感器,更安全更灵敏,可实现更高级力控。
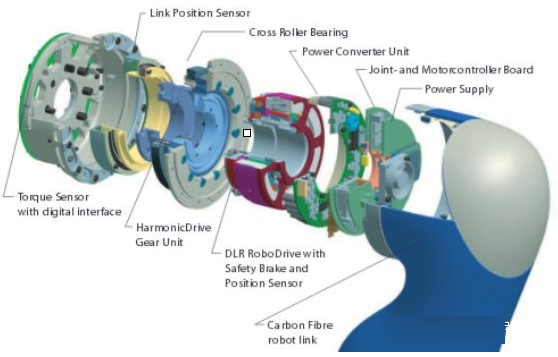
以雄克和ABB Yumi为代表的协作机器人,都是直流无刷电机驱动减速器,靠检测电流实现碰撞检测和拖动示教。这种关节功率小,质量轻,本质上就比较安全,但负载也无法做到普通工业机器人那样。还有一些厂家是通过在底座或末端法兰添加六维力传感器,在软件算法改进后就称为协作机器人。
协作机器人产业链分为上游零部件、中游本体和下游集成应用三部分。上游核心零部件与传统工业机器人类似,主要掌握在外资厂商手中,由控制器、伺服电机、减速器、传感器等零部件的生产厂商组成。
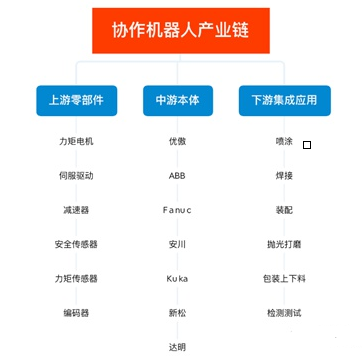
中游本体新兴的协作机器人厂商与传统四大家族展开竞争,负责工业机器人本体的组装和集成,即机座和执行机构,包括手臂、腕部等,部分机器人本体还包括行走结构。
下游是集成应用商,负责根据不同的应用场景和用途对机器人进行有针对性地系统集成和软件二次开发,应用在各行各业。
其中,上游核心零部件,占据了工业机器人整机大部分的成本和利润,也是技术上的核心和难点,是影响机器人性能最重要的部分。控制器、伺服电机、减速器这三大核心零部件的成本占传统工业机器人总成本约70%,其中减速器占整机成本约35%,伺服占整机成本约20%,控制器占整机约15%,而本体和其他部分仅占整机分别为15%、15%。
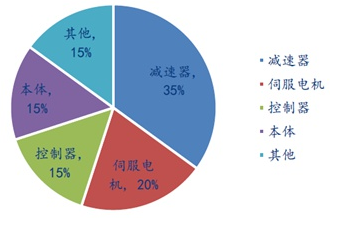
绝大多数协作机器人在设计上都要遵循轻量化安全设计准则,因此对关节集成度提出了非常高的要求,所需核心零部件也与传统工业机器人有很大区别,如中空伺服电机、谐波减速器、模块化编码器、伺服驱动器以及安全控制器等。
目前,协作机器人很多关键零部件还没有实现大规模生产,不仅选择受限,价格也十分昂贵,这就对开发人员提出了很高要求。因此,协作机器人的设计绝不是简简单单的零件拼凑,而是要将尽可能多的零部件集成在尽可能小的空间内。
2 上游:伺服电机、减速器、控制器
目前核心零部件的国产化一直没有得到很好的解决,这个问题在协作机器人产品中更为突出,因为协作机器人使用了很多传统机器人没有使用的零部件,例如直驱电机,模块化的编码器,关节力矩传感器,安全控制器等等。由于协作机器人关节的集成度很高,很多看似不起眼的小部件都会影响最终的产品定型和量产。
2.1 核心零部件——伺服:中高端市场为国外企业垄断
电机是机器人的动力来源,直接影响其有效负载、工作半径等关键参数。传统工业机器人大多使用交流伺服系统,工艺成熟,可选范围广。协作机器人通常要在内部走线,必须使用中空电机。同样扭矩下,直驱电机的价格大约在交流电机的3~4倍,使用这样的零部件成本较高,国产机器人就失去了“价格”优势。除科尔摩根(Kollmorge)外,目前市面上还没有非常合适的替代品。
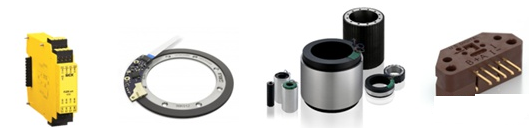
伺服系统是用来精确地跟随或复现某个过程的反馈控制系统,由伺服驱动器、伺服电机、编码器三部分组成,是工业机器人主要的动力来源。伺服电机可使控制速度,位置精度非常准确,可以将电压信号转化为转矩和转速以驱动控制对象。
根据《伺服与运动控制》的统计与预测,2018年年底伺服市场规模93.8亿元,同比增长4.7%。较2015年底,复合年增长率达13.2%,预计2021年中国伺服市场将突破100亿元。根据《伺服与运动控制》的统计,2018
年机器人占伺服系统下游应用的9.3%
传统机器人的伺服电机中、高端市场主要被国外企业垄断,进口产品在我国工业机器人伺服市场上占有率达70%以上,他们主要来自日本和欧美。其中,日系产品以超过50%的市场份额雄踞首位,其著名品牌包括安川、松下、三菱电机、三洋等,这些都是老牌的日本工业自动化设备生产商,技术上都很全面,其产品以良好的性能价格比和较高的可靠性获得了稳定且持续的客户源。以西门子、施耐德、博世力士乐等为代表的欧美品牌产品过载能力高,动态响应好,驱动器开放性强,但价格昂贵,体积重量大,在高端设备和生产线方面比较有竞争力。
国产伺服电机技术相对落后,产品主要在中低端领域。目前我国企业在中低端伺服领域已经可以实现大规模量产,以性价比的优势满足中小型和经济型用户的需求,例如汇川技术、埃斯顿、英威腾、华中数控、广州数控等企业的伺服驱动器及电机产品已相继进入批量化生产阶段。
2.2 核心零部件——减速机:技术壁垒最高,国产化率最低
精密减速器是工业机器人最重要的零部件,工业机器人运动的 “关节”就是由它构成,每个关节都要用到不同的减速器产品。减速器是多个齿轮组成的传动零部件,利用齿轮的啮合改变电机转速,改变扭矩及承载能力,也可实现精密控制。工业机器人对减速器的精度、负载和寿命等要求极高,其技术壁垒是工业机器人核心零部件中最高的一个,是对工业机器人本体性能影响程度最高的核心零部件。
目前,机器人领域使用较多的精密减速器是RV减速器和谐波减速器。谐波减速器体积小、传动比大、零背隙、高传动/体积比,多用于小臂、腕部或手部等轻负载的位置,因此广泛应用于协作机器人;而RV减速机则具有更高的刚度和回转精度,惯性小,具有良好的加速性能,广泛用于机座、大臂、肩部等20KG以上的重负载位置。
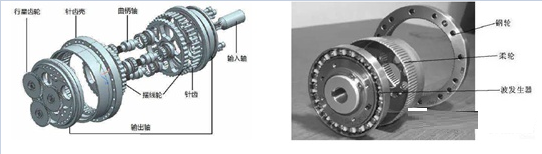
精密减速器制造因其对材料、设备、工艺等多个环节都有严格要求,而造成极高的投资和技术壁垒。当前全球机器人减速器市场呈寡头垄断格局,行业集中度较高。其中,日本纳博特斯克(Nabtesco)是生产RV减速器的世界巨头,约占60%的全球减速器市场份额,在中大负荷工业机器人领域,其RV减速器产品在全球RV减速器市场占有率更是高达90%以上。哈默纳科(Harmonic)则在谐波减速器领域拥有绝对优势,约占15%的全球减速器市场份额。除此之外,住友市场份额也有10%,旗下产品包括FINECYCLO系列零齿隙精密摆线减速器等。全球减速器市场呈现出以日本企业一派独大的高度集中化局面。
相比日本企业,国内企业切入减速器领域的时间较短,国产厂商技术水平仍有待提高。GGII数据显示,国内机器人减速器70%以上的市场份额被外资减速器企业垄断,国产化率不足30%。在减速器国产化进程中,尽管目前已有苏州绿地、来福、南通振康、秦川机床、中大力德等多家减速器厂商实现量产,市场接受度逐年提升,但与日系两大家依然存在一定的差距,主要体现在产品的综合性能,如精度、稳定性和使用寿命等。
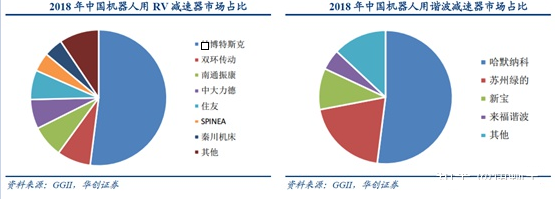
绿地谐波携最新研发的长寿命机型“N”系列谐波减速器参加第三届东京机器人展,该系列谐波减速器的精度寿命大于2万小时,具有精度高、承载高、温升小、效率高、运行平稳、抗冲击能力强等特性,逐渐成为国产谐波齿轮的中流砥柱。
2.3 核心零部件——控制器:工业机器人大脑(本体厂家自产居多)
对于智能装备生产制造企业而言,掌握运动控制的核心技术,非常有利于形成自身的竞争力,这个观点从机器人四大家族的发展中我们可以得到启示:运动控制技术是核心竞争力。
在涉及防护功能的安全控制器方面,市面上虽然也有不少现成的产品,但大多是面向流程工业的安全PLC。这些控制器不但价格昂贵,还无法实现协作机器人的某些专用安全功能,如速度限制,力矩限制,空间限位等。
Fanuc成立之初,就从事数控系统和伺服系统,是最典型的起家于运动控制的机器人公司。早在1971年,Fanuc就是全球最大的专业数控系统生产厂商,占据着全球70%的市场份额。基于扎实的数控系统和伺服系统技术,1974年开始推出工业机器人,公司具备核心技术,机器人性能卓越。到2017年,发那科机器人全球销量超过50万台,成为全球第一品牌。
安川机器人的崛起,更是基于其在伺服电机方面的优势。安川成立于1915年,自创始至今,一直深耕电机市场。1958年发明了DC伺服电机,1977年推出日本首台全电动型工业机器人MOTOMAN
L10。由于公司伺服电机性能全球领先,因而配备控制器之后,产品性能得到市场认可,早在2008年MOTOMAN累计出货超过20万台。
ABB由ASEA和BBC两家公司合并而来。ASEA早期从事照明电器和发电机业务,随后发明了发电机、变压器和电机使用的三相系统,1978年推出自主品牌的工业机器人。BBC公司早期负责输送高压电,后建成全球最大容量的变压器。两家公司1988
年合并后,基于两家公司在机电产品多年的布局,推出自主研发的控制器,加上一流的本体制造技术,最终占据全球工业机器人重要位置。
库卡早期一直探索焊接技术,1973年,库卡推出全球首台拥有六个机电驱动轴的工业机器人FAMULUS
,一举进入机器人领域。1996年,库卡作为首家机器人制造商着手研发开放式、以计算机为基础的控制系统PC
Based运动控制器,再次领先同行。
总结来看,四大家族中,有两家起步于运动控制,另外两家在进入工业机器人领域发展过程中,亦选择了重点攻克运动控制系统,最终造就了各家机器人顶尖水平,最终在大浪淘沙的行业发展中,成为全球工业机器人龙头品牌。
工业机器人的控制系统主要由硬件和软件两部分构成,硬件即工业控制板卡,软件主要是控制算法、二次开发等。控制系统的表现是一家工业机器人厂商设计理念的集中体现,成熟的机器人厂商一般自行开发控制器和伺服系统,从而保证机器人的稳定性和技术体系。因而全球控制系统的市场份额与工业机器人本体情况接近。
控制器作为工业机器人三大零部件之一,是工业机器人的大脑,对机器人的性能起着决定性的影响。工业机器人控制器主要控制机器人在工作空间中的运动位置、姿态和轨迹,操作顺序及动作的时间等。
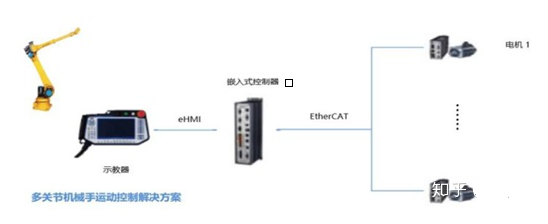
控制器硬件芯片依赖进口,软件算法差距较大。经过多年的沉淀,国内厂商的控制器硬件方案已经达到国际性水准,但物料受到限制,底层芯片依赖进口,国内尚无研发基础。在软件上,国际工业机器人品牌起步较早,经验与数据非常丰富,国产品牌在稳定性、响应速度、易用性等还有一些差距。
目前运动控制器主要分为三类:PC Based 运动控制器主要运用于半导体、机器人、包装机械、EMS电子制造服务等行业;专用控制器运用于机床、机器人、
包装机械等行业;PLC在纺织机械、包装机械、EMS 等行业运用较多。
3 中游
3.1 协作机器人本体
柔性机电一体化技术使机器人的安全性得到进一步保障。更安全的电机和执行机构是重要的科技创新,其中包括柔性机电一体化机械手和其他执行机构。
3.2 力感知
力感知是智能机器人与外界环境交互的一项重要功能,特别是对于抓取、轮廓检测、避障、人机交互以及力反馈控制等操作尤为重要。例如:在工业机器人生产线中,力传感器被用来做碰撞检测和反馈控制;在机械灵巧手系统中,力传感器被用来实现触觉感知;在手术机器人系统中,力传感器被用来辅助安全控制和碰撞检测等等。可见,碰撞(位置)检测和反馈控制是力感知的两个关键功能。
协作机器人力感知方式如下:
1. 基于关节电流的安全防护。优势在于成本低,但获取困难,其中协作机器人研发的先驱之一,丹麦UR机器人公司部分协作机器人采用该技术,在遇到一个超过设定值的阻力(如50~150牛顿,阻力值可以调整)就会自动停止运行,这确保了机器人在运动过程中不会误伤人类和其他设施。
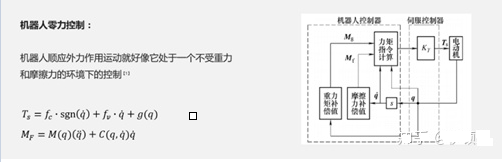
2. 基于单轴力传感器的安全防护。如KuKa iiwa,单轴一维力传感器增加了设计难度,降低了关节的刚度
,同时目前量程相对受限。
3. 六维力传感器。该方案便于集成,一般可以安装在底座或者末端,但价格昂贵且量程受限。力的感知误差主要由机器人姿态角度误差引起,
力矩感知误差主要由采样数据的随机误差引起。
在静态条件下,机器人腕部六维力传感器测得的力与力矩数据由三部分组成,即:1)
传感器自身系统误差; 2) 负载重力作用;3) 负载所受外部接触力。若要得到负载所受外部接触力, 需要消除传感器系统误差、负载重力作用两方面的影响(低度运动时,惯性力的影响可忽略)。其中UR的E系列是通过安装末端六维传感器实现力控制。
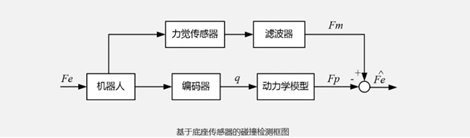
4. 基于压电式电子皮肤。该技术检测灵敏,但大大的增加了设计和布线难度。
协作机器人各个力感知方式的使用场景(文件来自于Jaka)如下:
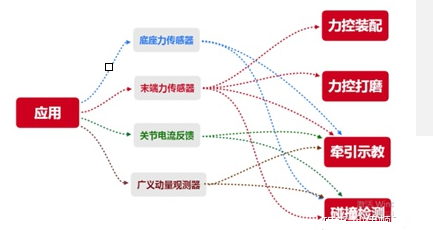
4 下游:分散到各行各业的系统集成
工业机器人系统集成负责根据不同的应用场景和用途,对机器人本体进行有针对性地二次开发,并配套周边设备,实现工业化应用。与上游核心零部件、中游本体相比,下游系统集成的技术壁垒最低,且具备本土化服务竞争优势,国内企业纷纷涌入下游系统集成领域,但集成商一般规模都不大,企业中营收规模超过1亿元的不超过100家,绝大部分企业系统集成也不不超过3000万元。其中,营收规模超过3亿元的企业也主要集中在汽车焊接集成领域,整体市场竞争格局较为分散。
2020年MIR Databank对7888家系统集成商中的5627家厂商进行了行业覆盖分析,其中1906家覆盖汽车行业,占比33.9%;698家覆盖食品饮料行业,占比12.4%;588家覆盖家电行业,占比10.4%;413家覆盖医疗行业,占比7.3%;571家覆盖消费类电子行业,占比10.1%(有些厂商会涉及覆盖多个行业)。
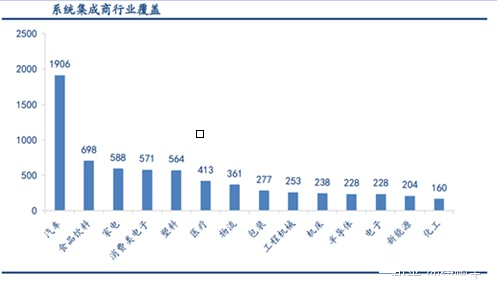
造成这种现象的原因,来自于行业特性:(1)系统集成商是以人为核心的订单型企业。系统集成商的核心竞争力是人才,因此系统集成商实际是轻资产的订单型工程服务商,核心竞争优势是销售人员、项目工程师和安装调试人员的经验,没有太多的核心技术,或者固定资产,所以系统集成商很难通过并购的方式扩张规模。(2)几乎每个项目都是非标的,项目之间无法完全复制,不能简单复制上量。(3)系统集成项目通常采用"3-3-3-1"付款模式,即图纸通过审核后、发货完成后以及安装调试后分别拿到30%的资金,最后剩余的10%为质保金,一般在产线平稳运行
1-2 年后获得。按照这种付款流程,系统集成商通常需要垫资经营,因此限制了其同时实施项目的数量及规模;(4)相较于机器人核心零部件与本体业务,大多数系统集成是一个技术壁垒较低的领域,行业进入较为容易,在近年市场爆发增长的情况下,诞生了一大批中小微系统集成商,低端重复建设,市场更加分散。
拓展系统集成业务是工业机器人制造商下探趋势:系统集成环节的技术难度比工业机器人本体、核心零部件等环节低,但其商业模式更倾向于轻资产,市场空间大约是本体环节的3-4倍,是大多数优秀的工业机器人厂商希望拓展的环节。
与此同时,拥有庞大应用场景的下游企业通过资本手段切入机器人领域。无论是以美的为代表的家电企业,华夏幸福、碧桂园等地产企业,还是京东、阿里等电商物流企业,都是资本充足的机器人下游大型企业,拥有庞大的应用场景,在自身需求驱动与政府扶持下进行产业布局。下游企业的加入将加快整个行业的发展,或将使我国机器人行业竞争格局发生变化。
长期来看,真正具有技术和渠道的全产业链布局的公司将能够成长为巨头。一般具备如下条件的企业能够胜出:一方面规模较大、资金充裕、项目经验较多的集成商;另一方面细分领域占优的集成商。
|